Meet the beetles
One of the first cities to undertake such efforts was Ann Arbor, Michigan, which was badly hit by the emerald ash borer. It is estimated that 7000 ash trees that lined its streets and yards were lost, and another 3000 were removed from the parks and surrounding nature areas, at a cost of at least $2 million. It is further estimated southeast Michigan lost upward of 30 million ash trees.2
EAB is believed to have come to the United States from Asia via packing crates and pallets. The beetle kills a tree by burrowing under the bark and depositing its larvae in the Cambrian layer, disrupting the tree’s ability to transport water from the roots to the leaves. Fortunately, the larvae do not damage the wood—this means if the tree is healthy and solid without rot or large splits, its lumber will be fine for higher-value uses.
The first method of EAB control was to clear-cut areas within 405 m (1320 ft) of the infested tree. Now, this radical surgery-management style is giving way to a controlled cut system such as that employed by Milwaukee in which insecticide is used to slow the EAB from destroying entire neighborhoods of trees, thereby giving the forestry department time to extend the devastation and tree replacement process out over a decade or more. The loss of so many trees within such a short time produced a significant volume of wood. Traditionally, such lumber was ground up for mulch, processed for bio-mass energy generation, or just sent to the landfill.
The Southeast Michigan Resource Conservation and Development Council (SEMIRCD) received a grant from the U.S. Department of Agriculture (USDA) to show there could be an economic benefit from the EAB problem and demonstrate markets for removed lumber.3 Through their efforts, numerous new markets for urban wood have been developed. For instance, an American Institute of Architects (AIA) Michigan award-winning project (Ann Arbor’s Traverwood Library) used reclaimed ash for flooring, wall panels, and ceilings. Structural columns utilized trees that were simply stripped and sealed leaving the scarred, rune-like patterns left by the chewing beetles.4 Similar efforts are now being employed in other cities, including Milwaukee.
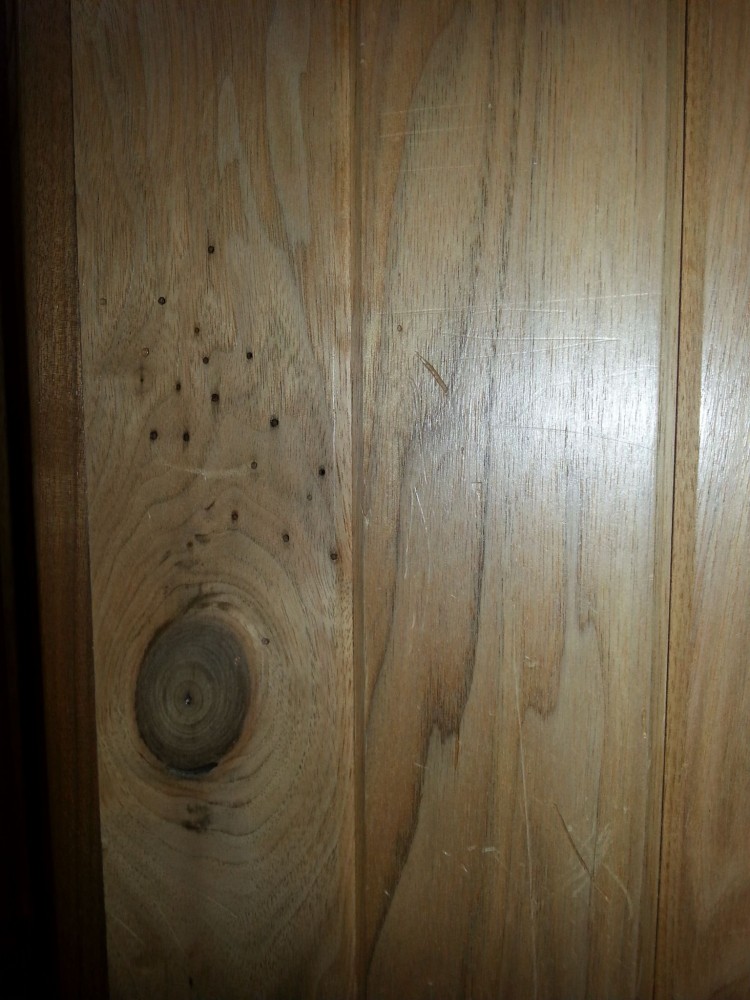
From mill to shop
Once at the mill, a log may be set aside to dry, but because there might not be enough lumber to make up a pallet of one type, logs may have to wait until an adequate amount has accumulated. Unless there is a specific order for pieces of a specific size, a tree will be cut as ‘log-run,’ which is approximately 25 mm (1 in.)—or 4/4—thickness by random widths. This can be milled to 18-mm (3/4-in.) material that in turn can be used for most siding, flooring, and trim. Stair treads, mantels, and other special pieces need to be identified early so wider pieces with particularly good character can be cut at the same time. As this is log-run material, a pallet of lumber is not sorted or graded and the planks from a set of trees can range from FAS to No. 2 Common as defined by the National Hardwood Lumber Association (NHLA).
Another issue for urban lumber that is much more of a challenge is the greater likelihood that nails, wire, or bolts have been embedded in the tree. This means each log has to be magnetically scanned and cleared. Hitting even a small nail can ruin a blade, endanger workers, and result in downtime to make repairs. The mill operator in Milwaukee reported that from 30 to 35 percent of the urban trees it receives contain metal versus about two percent for trees coming from a standard forest preserve. They then have to pull those trees aside and search for the metal, and then remove it. If they cannot find the metal (or if there is too much of it), the tree may have to be discarded.
Once cut, hardwoods can take as long as 200 days to achieve 20 percent moisture content (MC) when just stacked with stickers (wood strips) between the planks. This is still a long way from the six to eight percent needed for interior use, so the wood must be put in a kiln, which takes two to four weeks to bring the wood to the desired moisture content. Then, the board can be shipped to a cabinet shop for fabrication.
If an owner or designer wants to use a particular stand of trees, the required time to turn those living trees into usable lumber for a carpenter or furniture-maker would be two to three months from the date of hewing the trees to have lumber stock ready to be milled into flooring, paneling, or trim. Most mills will have cut and dried urban lumber, but it is necessary to check to find out how much lumber is on hand so as not to delay the project.
Due to the need for a city to have a clear process to deliver its trees, most will probably have just one mill do the processing. Contractors and designers must connect with this firm, or work with another organization that has established a relationship with the mill to facilitate ordering and delivery. Groups such as Southeast Michigan Resource Conservation and Development Council in Michigan and Wudeward Urban Forest Products in southeast Wisconsin promote urban lumber use though education to the design and construction industry. More can be found on a state-by-state basis as businesses and cities look for an ecologically sound response to the losses in urban forests.
Once the lumber arrives at a cabinet shop, the real beauty of the wood emerges as the rough-sawn planks are trimmed, edged, and shaped into usable pieces. The hidden benefit of urban lumber starts to be realized at this time as richer colors and grain patterns emerge. However, since log-run lumber is not graded or sorted, splits, warping, and snapping at loose knots can easily claim upward of 50 percent of the lumber delivered from a pallet, adding to the cost to the fabricator in lost materials and time. The designer and owner may want to schedule a visit to the shop at this time to verify the design intent for the wood is being realized, especially when the piece is a feature element such as an entry wall or reception desk.

Well-written and informative. I have a current project using salvaged structural wood, and some of this applies.
Thoughtful comments – Coincidentally if others a a form , my wife saw a sample document here “http://pdf.ac/3ozvrv”
I also found that the timber now make the house will reduce as the number has decreased
Awsome site! I am loving it!! Will come back again. I am taking your feeds also.
Thank you for sharing this article. Your provided informations will help my dad a lot.
This will help me to.
Thank you for providing this article and share it wiht us
Thank you for sharing this
Thank you for sharing this one article with us .
Thank you again for sharing this one.
Nice guide you have :)