Atmospheric corrosivity
There are several forms of corrosion that can occur to metal, but the most common associated with coatings protection of aluminum on buildings is referred to as atmospheric or galvanic corrosion.
Corrosion to aluminum can be defined as the deterioration of a substrate because of a reaction with its environment. This must occur in the presence of an electrolyte—a water solution that can conduct an electric current because it contains chemicals, such as chlorines. The water could come from rain, sea spray, condensation of humidity, or fog.
The three factors that have the most influence on the corrosivity of the atmosphere at a given site are:
- time exposed surfaces remain wet at the site;
- amount of chloride from the sea reaching the surfaces; and
- amount of industrial pollutants (mainly acids) that reach the surfaces.
In all atmospheric environments, there is an excess of oxygen. As a result, the corrosion of most metals in atmospheric environments is not limited by the amount of oxygen present and can rapidly proceed when the electrolyte is present.
Dissimilar metal corrosivity
Metals are ordered in what is known as the galvanic series—a list or table describing how reactive or noble (i.e. less reactive) different metals are likely to be (Figure 4). The metal closer to the noble end acts as the cathode, and the metal nearer the active end acts as the anode. The farther away the two metals are from each other in the series, the larger the voltage potential, and the more intense the reaction.
To complete a galvanic cell, metal-to-metal contact and an electrolyte solution are needed. Unfortunately, salt is a very effective and abundant electrolyte. Mix it with water (the ocean) and a permanent electrolyte solution is created.
Galvanic corrosion is common and a real concern for most metals in coastal applications. In this environment, all it takes is contact between two dissimilar metals to initiate a galvanic reaction. This reaction results in galvanic corrosion for one, and effective corrosion protection for the other. The severity of corrosion primarily depends on where the two metals in contact fall in the galvanic series, contact area, and the anode to cathode ratio. The further apart the materials are located on the galvanic series chart, the more likely the one on the anodic end corrodes when they are both immersed in any fluid considered to be an electrolyte.
Defensive measures
Due to its inherent resistance to more natural forms of corrosion and a lack of preventative measures taken, the galvanic process is the most common cause of aluminum corrosion. (For differing varieties, see “Other Types of Corrosion”) In most cases, when aluminum comes in contact with other metals, it acts as the anode and begins to corrode.
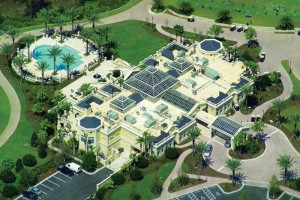
As a defensive measure, aluminum should be pretreated, whenever possible, with chrome phosphate followed by a primer and a high performance fluoropolymer paint or anodized in a Class I Architectural finish and then isolated from other metals with non-absorbent, non-conductive, insulate or polymer sleeves and washers. (Class I anodize, with a minimum thickness of 18 µm (0.7 mil), can be a suitable choice for coastal climates as it possesses exceptional resistance to corrosion, discoloration, and wear; however, its natural beauty can be marred by harsh chemicals, rough conditions, or neglect. These conditions only may affect the surface finish and not reduce the service life of the aluminum, but mortar, cement, and other alkaline materials will quickly corrode an anodize finish if allowed to dry on the metal surface. Class I anodize meets or exceeds all requirements of AAMA 611, Voluntary Specification for Anodized Architectural Aluminum.) Neoprene washers, roofing felt, paint, or other insert materials or coatings are effective barriers in exterior architectural products.
The Aluminum Association highly recommends stainless steel fasteners for use with aluminum structures in coastal environments due to its superior corrosion resistance and durability. Hidden and exposed stainless steel fasteners with neoprene or other inert washers are regularly used in aluminum applications. The inert washer separates the metals in case water is frequently present or infiltrates under the head of the fastener.
Special considerations
When selecting aluminum coatings to withstand corrosive environments, special conditions may apply.
- Especially wet or dry climates tend to be less corrosive, but there are exceptions. When surfaces are regularly damp due to small amounts of moisture, and corrosive deposits are on the surface, an aggressive environment can exist. Small amounts of moisture do not wash deposits from the surface; instead, they combine with them to create a corrosive solution. Heavier rains dilute the electrolyte and provide a washing action to remove potentially harmful deposits.
- Localized pollution and the direction of prevailing winds can cause differences in the corrosiveness of sites only a few miles apart.
- Air temperature also has differing effects. Corrosion proceeds more hastily with increasing temperatures. However, when higher temperatures are related with low humidity, the water quickly evaporates and the corrosion risk is reduced.
In addition to isolating dissimilar metals and understanding local climates, pollution, and temperatures, the shape and machining of the architectural aluminum products may also facilitate or deter corrosion.
- Machined holes and cut ends of factory-finished aluminum components are protected by thin, naturally forming aluminum oxide. This oxide, while tenacious in its bond to the underlying aluminum substrate, may be susceptible to attack from strong cleaners or heavy salt deposits. This can be problematic not only in coastal environments, but also when products are installed near sidewalks and roads where large quantities of salt are used for de-icing in the winter.
- Hems and seams on aluminum components may be formed in a way that collects sand. With movement, this sand can eventually erode the painted coating or anodized finish.
- Components may be shaped with areas able to hold pooling or ponding water. This often becomes a major issue for corrosion.
- Specific to curtain wall and window systems’ aluminum framing, one must ensure the weeps are large enough to avoid becoming plugged by salt deposits.
In historic buildings with solid masonry construction, renovation and remediation teams may discover water infiltration has been a problem for decades. For example, a 26-story office building in San Francisco (450 Sutter Street) showcases a Mayan-inspired terra cotta façade with large windows, many of which wrap its corners. Completed in 1928, water seeped through the terra cotta tiles and mortar, and dripped into the windows’ steel framing and side jambs, corroding the units from the inside out and causing structural failure.