Stainless steel possesses structural properties that are much greater than that of aluminum. Bearing this in mind, lighter materials can be considered when the profile or geometry of the design is more important than the colors. Some designers prefer the metallic appearance of these façade assemblies. Risk of corrosion for a stainless-steel element is reduced by the composition of this material. In these cases, a stainless-steel anchor clip is the logical solution for attachment. If it is a coastal installation, T316 stainless steel alloy is preferred over a common T304 alloy.
Structural substrate considerations
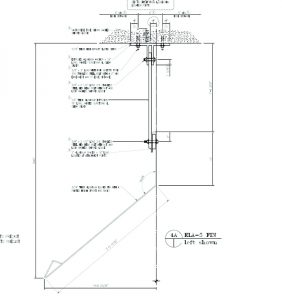
The next important question to ask: Is the attachment to cast-in-place concrete, precast concrete, steel, aluminum, or a composite structure?
Often, architectural metal assemblies are designed to span from slab to slab of a building structure. In many cases, the structure is precast or cast-in-place concrete. Whether the attachment clip is mounted to the structure using a drilled expansion anchor or an embedded steel insert channel the same basic principles will apply.
As noted previously, protecting the aluminum anchor clips on all surfaces is critical. This is particularly important when the risk of exposure to salt spray or concrete runoff is present. When an anchor clip is attached to or adjacent to a concrete substrate, it is essential the coating is applied after the part is fabricated so all edges and clear holes are completely coated. Coatings can be spray-applied polyvinylidene fluoride (PVDF), dry thermally cured powder coatings, or a wash coating such as anodizing. If the clip is exposed to view and a part of the design, then a PVDF color may be selected.
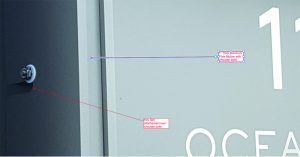
Salt- or concrete-laden moisture intrusion is destructive to an aluminum substrate, especially if the moisture is not permitted to dry in between weather events. Anchors situated on vertical surfaces are more likely to be ‘washed’ during a weather event and are able to dry out. Anchors on skyward-facing surfaces are more vulnerable to exposure to a solution of runoff and should be avoided. If these situations are impossible to avoid, then a stainless-steel anchor clip is a much better alternative (see Figures 1, 2 [page 19], and 3, for examples of full coating protection).
Protection steps are critical at each layer of the anchor assembly.
Connection surfaces
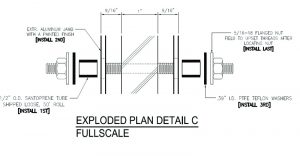
Where the actual assembly is bolted to the anchor clips, nonmetallic bushings and bearing sleeves should be used to isolate stainless steel hardware from penetrating the coated aluminum surfaces and exposing an unprotected aluminum substrate (see Figures 4 and 5 for illustrations of hardware protections).
Bearing surfaces
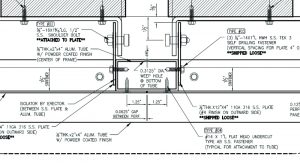
It is important to isolate the clip from the structural substrate. An aluminum anchor clip must be carefully coated and isolated from the concrete or steel structural substrate with a nonmetallic isolation material of sufficient thickness and strength to resist the compression of the loads imposed and interrupt the conductivity of an electrolytic current. Ultraviolet (UV) and weather-resistant high-density plastic shims or spacers are commonly used here.
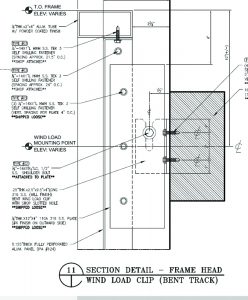
In Figures 1, 2 , and 3, there is a double-tee extruded anchor clip with a nonmetallic spacer pad (shim) to isolate the coated aluminum from the concrete structure. There is a standoff plate inserted into the double-stemmed tee to create the desired cantilever off the face of the structure. The holes between the anchor clip and the standoff plate are isolated from the stainless steel through bolts using polytetrafluoroethylene (PTFE) washers and sleeves to prevent the stainless steel from damaging the finished aluminum. The same isolation is needed between the coated aluminum fin feature and the stainless-steel hardware that attaches the fin to the standoff plates. Even though these surfaces are coated, the movement of the parts during installation or in service under thermal and wind loads could cause the threads in the fasteners to gouge the aluminum and make the substrate vulnerable to corrosion.