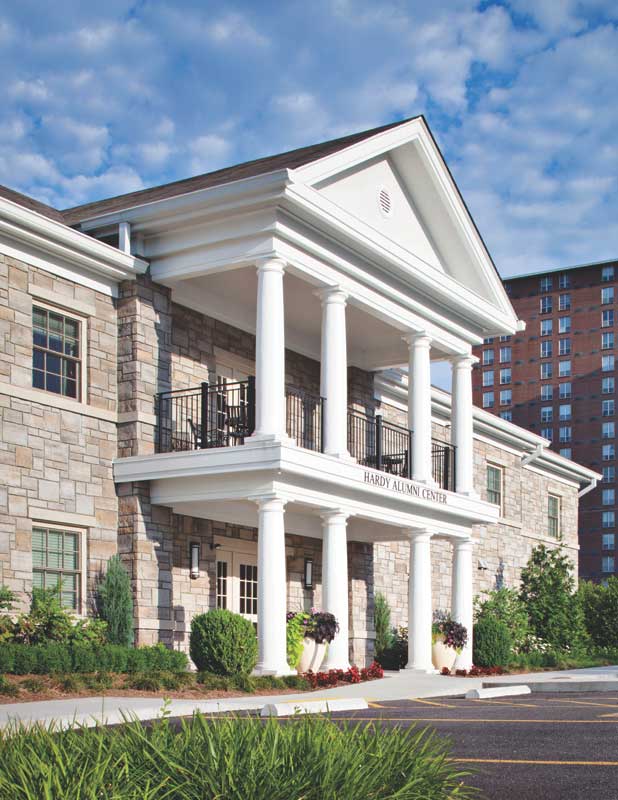
Full-depth vs. lightweight veneers
Choosing full-depth or lightweight veneers can vary by personal taste and comfort level, and largely depends on the application. Wall height can be a factor as well. Some design professionals are less comfortable with having adhered manufactured lightweight veneers installed on high walls, given the rare possibility one might come loose. In such an application, the builder or retailer may prefer to spend more on a cavity wall to accommodate a full-depth anchored veneer, which is typically 92 mm (3 5/8 in.).
Lightweight veneers will frequently be chosen as economical façades in applications such as retail buildings or senior living facilities because mixed-material looks for siding, stucco, and stone foundation façades and accents are a popular trend.
Another possibility for dressing up a light commercial building is to blend manufactured stone and brick. A sill is typically required to separate the materials, but the bed depth can accommodate a set-in product like full-depth veneer. However, the cost is higher than an adhered application. Stone veneers are easy to match to natural stone, which can be cut to the same width as a full-depth or thin veneer.
Manufactured stone veneer color choices
When measuring wet- versus dry-cast advantages, one should consider colors for dry-cast can be customized before arriving onsite. This can be especially important for structures opting for a more architecturally distinctive structure than a traditional retail building. For example, a recent large-scale, 3700-m2 (40,000-sf) museum in Kansas, designed by Jonathan Kharfen, AIA (Boston’s Verner Johnson Architects), used this customization option to match colors in the natural environment. The project saved significant cost by blending manufactured full-depth veneers with locally sourced stone onsite in the way the architect desired.
For national retailers, manufactured stone veneers add speed and economy to the building process, while also effectively dressing up the building as compared with painted block. For example, a popular trend for retail is to combine integral colors of split-face block with manufactured structural concrete masonry units (CMUs) and stone or brick veneer at half the price of a traditional cavity wall.
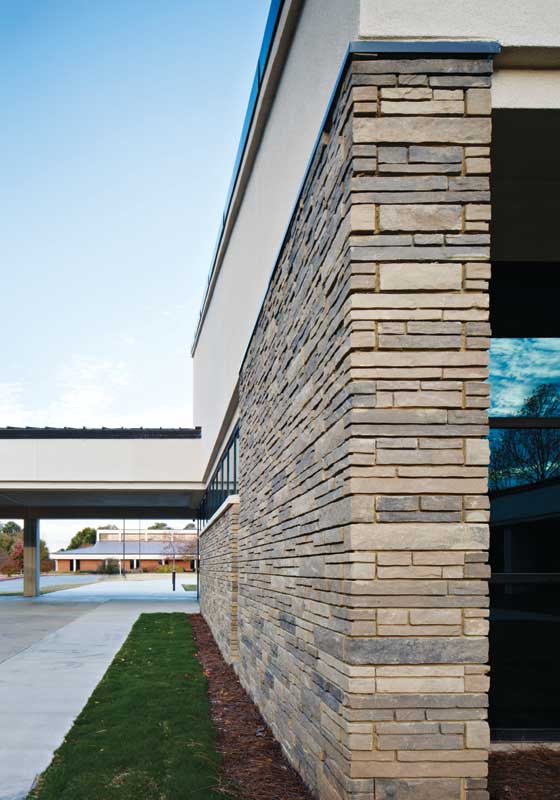
As aesthetics in communities come into play, more retail buildings are adopting the mixed-material veneer look, which will likely be manufactured stone—either thin or full-depth, based on cost. Smaller retailers, condos, hotels, and senior living facilities are going in this direction to blend in with the community and meet local ordinances.
The growth of senior living facilities (due to the aging baby-boomer population) provides a prime example of making a residence building feel like home, both on the exterior and interior. These structures are typically one to five stories, with
a band of stone veneer around the lower level and stucco or siding on the upper wall. Manufactured lightweight veneers can provide beautiful textures and colors in these applications, but with much higher performance and lower moisture and cost than other materials.
For light-commercial application exteriors, it pays to look at the overall project—what are the aesthetic needs, thermal and moisture considerations, and
de-icing chemicals used? For long-term performance, dry-cast manufactured stone veneers provide easy installation, fewer headaches, significant cost savings, and simple installation.
As more and more jurisdictions mandate continuous insulation per the 2015 International Energy Conservation Code (IECC), lightweight veneers offer another advantage—they can be installed atop such assemblies, with builders using longer screws for the wire mesh going into the studs.