
by John Woestman
The purpose of building insulation is to reduce heating and cooling energy consumption, contribute to durability, and provide comfort for occupants. However, there are numerous locations where significant exposure to moisture—which severely affects a material’s thermal performance—occurs, such as in protected membrane roofs, vegetative assemblies, below grade, and frost-protected shallow foundations (FPSFs). Polystyrene foam insulation has unique properties differentiating it from other such materials, making it a suitable choice for such applications.
When specifying polystyrene foam insulation for building applications where exposure to moisture is expected, it is important to understand ASTM C578, Standard Specification for Rigid, Cellular Polystyrene Thermal Insulation. This industry standard lists all polystyrene foam insulation types, defining the minimum physical properties for each. Both extruded polystyrene (XPS) and expanded polystyrene (EPS) foam insulation are represented, as shown in Figure 1.
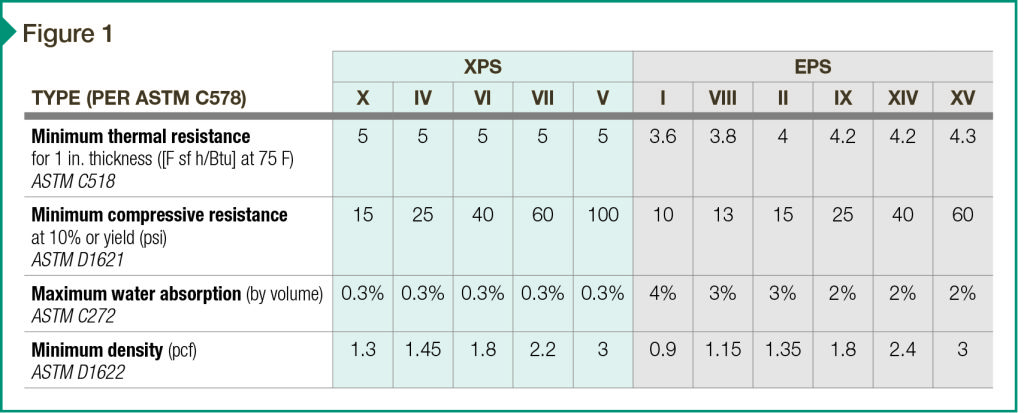
There are important differences between the different offerings of XPS and EPS insulations. The former is available in Types IV, V, VI, VII, and X, all with minimum R-values of 5.0 per inch, and minimum compressive strengths ranging from 104 to 690 kPa (15 to 100 psi). EPS, on the other hand, comes in Types I, II, VIII, IV, XIV, and XV, with minimum R-values ranging from 3.6 to 4.3 per inch, and minimum compressive strengths ranging from 69 to 414 kPa (10 to 60 psi).
ASTM C578 requires XPS insulation allow no more than 0.3 percent water absorption (by volume), whereas EPS must allow no more than two to four percent water absorption (by volume), depending on the material type—this is six to 13 times more than XPS. This is because there are fundamental differences between the properties of XPS and EPS that are critical to understanding which material to specify for applications requiring high resistance to moisture intrusion.
XPS is manufactured through an extrusion process. Essentially, a molten material is extruded through a die where it expands into a uniform closed-cell rigid foam insulation board with no voids or pathways for moisture to enter. EPS is manufactured with small foam beads placed in a mold and steam-expanded into a large form from which foam boards are cut. This method of manufacture can result in interconnected voices between the beads that can provide pathways for water to penetrate into the insulation. The water-resistance specifications for XPS and EPS in ASTM C578 are reflective of the physical structures of the two materials (Figure 2).
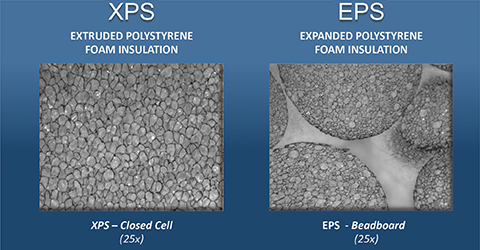
Why is moisture absorption resistance important? Water is an excellent conductor of heat—a fact illustrated by how people tend to feel cold (or at least cool off) when they get wet. This is the same concept with a building where the insulation absorbs moisture—any moisture absorbed by insulation can degrade that material’s R-value, negatively affecting energy savings and the comfort of those inside the building.
Insulation for roofs
A protected membrane roof (PMR) is an assembly that is designed with the waterproofing membrane installed on the roof deck, and the insulation and ballast installed atop the membrane. In this configuration, the insulation and ballast protect the roof membrane from environmental exposures and physical damage. Consequently, insulation used above the membrane must have superior moisture resistance and durability. For such applications, the moisture-resistive properties of XPS often make it a suitable choice when specifying foam insulation to protect the roof.
Commonly designed as in this PMR setup, vegetative roofs are becoming more common because of their environmental benefits. There are two basic types of these green roofs—extensive and intensive—differing in terms of cost, depth of growing media, and choice of plants.
I visited many websites except the audio feature for audio songs current at this site is in fact excellent.