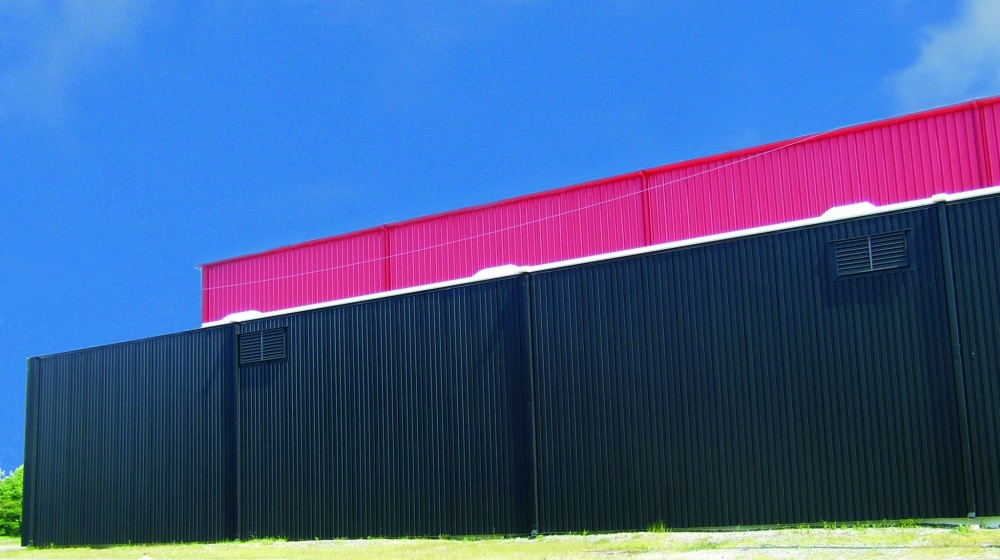
The Cigas Machine Shop in Pottstown, Pennsylvania, is located in a building previously owned by the Bethlehem Steel Corporation, with parts of the structure dating back to the late 1880s. Back in that era, Bethlehem Steel was involved in the production of fabricated components used in the construction of the Golden Gate and many other familiar bridges.
When Cigas took possession of the building in 2007, it was a typical steel mill structure. With no heat or insulation, inadequate ventilation and a black exterior skin, the temperature extremes inside were unbearable in the summer and winter months. While the temperature was more moderate in the spring and fall, it was dimly lit and as unpleasant inside as it was unattractive outside.
Despite its age and problems, the basic structure was in remarkably good condition and far superior to current building standards. With readily available utilities and services, the site was an excellent candidate for renovation. The design team’s challenge was not only to bring the site up to contemporary building and safety standards, but also to make it as energy-efficient as possible while maintaining as much of the original architectural character and craftsmanship as practical.
In its original condition, using conventional methods and 2006 fuel prices, the annual cost to heat the 6875-m2 (74,000-sf) building in the winter was estimated to be $350,000. A strong steel structure and thick concrete slab are positive attributes, but the uninsulated space with 20-m (65-ft) high interior volume created significant operation inefficiencies. There was also no effective method of moderating the dangerous summer heat.
The challenge was to find a way to provide a comfortable and safe environment for employees, while also reducing the operating overhead for the building. No single technology could address both needs and the solution came from a blend of carefully selected sustainable building materials and green technologies.
High R-value insulation was added to walls and ceilings. Daylight harvesting was achieved with the extensive use of high performance skylights. A rainwater harvesting system was implemented to significantly reduce the demand placed on municipal water, sewer, and storm water management systems. A Galvalume metal roof was installed, which has special ‘cool’ coatings, offering superior performance characteristics and extreme durability. Improving the appearance of the building, a new exterior metal skin also helped to reject the summer heat.
A total of 1084 m2 (11,670 sf) of black, transpired solar collector wall panels were installed on the building’s southern facing vertical surfaces. They both added aesthetic appeal to the structure, and serve as an integral part of the system that provides the primary source of heat in the winter.
The system collects heat from the sun and transfers it inside the building, even on the coldest winter days. It also provides passive cooling in the summer and fresh air exchange for a healthy interior environment year-round. In extreme winter conditions, the solar system is supplemented with heat from a high-efficiency natural gas fired system. With 20-m high ceilings, some mechanism to mix the air inside the building was necessary. Small, efficient destratification fans were used for this application.
The facility’s owner, Craig Cigas, explained actual fuel costs to heat this building in the first year were reduced to just $890 versus the projected $350,000.
“We turned a six-figure problem into a three-figure solution,” he said. “It’s an incredibly simple, yet effective, design that immediately appealed to me. Moreover, we were able to achieve a 12-month return on our investment.”
The industrial shed was harmonized with a superior workplace that resulted in reduced energy consumption, while offering employees better air quality. This helped move Cigas’ manufacturing operation to the forefront of green industrial facilities.
The renovation hit the mark, said project architect, Martin Breen, formerly with AP3C Architects and now with Philadelphia’s KDA Architects.
“The machine shop now has a contemporary aesthetic that represents the world-class manufacturing processes taking place inside,” he explained. “It stands out in the stark industrial landscape and is a shining example of how industrial facilities can be environmentally responsible.”
While the project did not pursue certification under the Leadership in Energy and Environmental Design (LEED), it still looked to the green building program for certain principles.
“Continuously searching for ways to apply LEED design guidance and sustainable technologies as they mature and come to market is not only the responsible thing to do, it’s the smart thing to do,” Cigas said. “We should all be thinking green and sharing what we learn.”
To read the full article, click here.