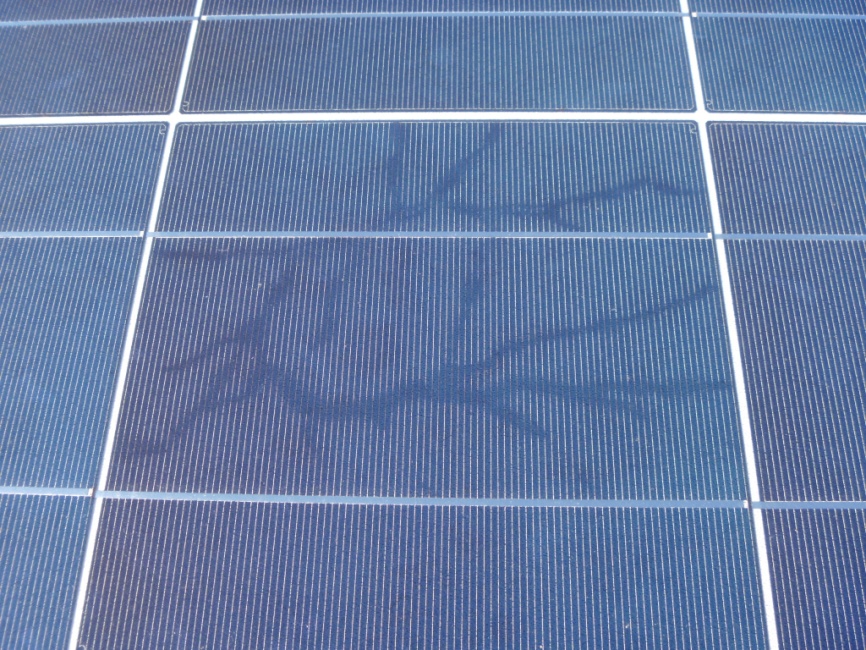
All images courtesy Motech Industries
by Sam Tsou
For construction specifiers making client recommendations when moving to a renewable energy system, photovoltaic (PV) solar power can be a daunting challenge. This is especially the case when one only considers the impressions of earlier years that do not reflect today’s economic picture. Current U.S. government statistics aggressively support the reality commercial and residential installations are proving to be a valuable approach—with a return on investment (ROI) that means the client payoff is becoming shorter and shorter.
Quality tends to be about longevity—how does one know the recommended module can really be expected to last? This can be a big question if a specifier does not have the thorough background on solar power to determine the right direction. Therefore, this article intends to provide some insight about basic details that can be explored with potential solar providers to ensure they can deliver what the client needs.
For example, it is practically a given most solar panels have undergone the ubiquitous design and safety qualification tests as a prerequisite to marketplace participation. These include:
– International Electrotechnical Commission (IEC) 61215, Crystalline Silicon Terrestrial PV Modules–Design Qualification and Type Approval;
– IEC 61730, Photovoltaic Module Safety Qualification?Part 1: Requirements for Construction; and
– Canadian Standards Association/Underwriters Laboratories (CSA/UL) 1703, Flat-plate Photovoltaic Modules and Panels.
In their current form, these tests are widely acknowledged to weed out designs susceptible to many infantile failure mechanisms. Unfortunately, important degradation mechanisms are left completely unexamined or inadequately probed by this basic suite of tests. A manufacturer must be cognizant of these blind spots and eliminate them by extending the duration of a subset of the basic qualification tests, as well as conducting supplemental tests to access sensitivity to otherwise untested degradation pathways.
There is a host of ‘beyond-the-basics’ tests a manufacturer should conduct to assure its customers of a quality product:
– extended temperature cycling potential induced degradation testing;
– extended ultraviolet (UV) light exposure;
– bypass diode thermal runaway testing; and
– dynamic mechanical load testing.
Manufacturing quality management system
A large-scale PV power plant contains thousands of individual panels, and each must be produced consistently. In many cases, manufacturing occurs at multiple factories in different countries, each with a unique equipment set. These disparate manufacturing conditions must be unified by a consistent quality management system (QMS). All sites must manufacture product to the same in-process inspection criteria, material-handling procedures, verification frequency, calibration standards, defect definitions, and operator training levels.
For these reasons, one should ask questions to see whether the QMS helps ensure:
– ‘first in, first out’ material usage;1
– incoming material inspection to ensure compliance with engineering specifications;
– module power measurement calibration and adjustment procedures; and
– process audit measurement of solder peel strength, ethylene vinyl acetate (EVA) encapsulant degree of cross-linking, and interface t-peel adhesion strength at all material interfaces.2
The organization should apply suitable methods for monitoring processes.
This is just a short list of items the QMS is required to enforce. A manufacturer should be able to produce the pedigree of any PV module including:
– date of manufacture;
– material lots used in the production of that module;
– incoming inspection results of those materials;
– flash and final test results; and
– process audit records that bookend the module’s production date.
Product change
When considering ways to protect a client’s investment, one may find a vendor with quality products and quality manufacturing systems—however, will that company still exist in the longer term? This largely depends on a company’s ability to incorporate product changes in a timely manner without compromising quality.
Given the fact module materials will remain fixed in production for less than two years (and often much less), how are good material changes differentiated from the bad? This may seem simple since IEC actually publishes a list of the minimum design qualification and safety tests that must be passed to incorporate a change into an already certified product—these are the so-called IEC Retest Guidelines.3 However, passing only these boilerplate tests can leave the product’s reliability in question. Enhanced test methods should be used to identify materials worthy of assimilation into the product bill of material (BOM).
Solar cell
One of the most decisive factors for quality and performance of solar modules is the solar cell. Some of the critical quality checkpoints performed that go beyond the IEC Retest Guidelines for a cell change are:
– extended thermal cycling performance for metallization chemistry or solder pad geometry/area changes;
– metallization sensitivity to acetic acid formation within EVA (changes to silver paste formulation and sintering conditions can result in dramatic changes to acetic acid corrosion sensitivity); and
– limits on shunt resistance (Rsh) and reverse current leakage (Irev) at maximum substring operating voltage during cell production (proper limits prevent localized hotspots).
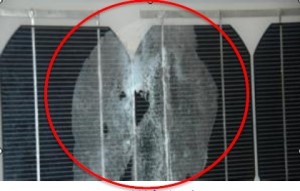
EVA encapsulation
Ethylene vinyl acetate remains the most commonly used encapsulant in PV module production. EVA functions to bond all the material layers into a uniform laminate, provides an important electrical barrier to leakage current through the glass side of the module, and allows high light transmission into the solar cell.
Screening tests able to distinguish robust EVA formulations from poor performers should include methods for determining:
– leakage current mapping as a function of temperature, humidity, and applied voltage (all things being equal, higher leakage currents will accelerate certain degradation mechanisms such as potential induced degradation [PID] and electrochemical corrosion);
– rate of yellowing versus UV exposure dose and damp heat exposure time; and
– acetic acid formation rate versus damp heat exposure time (an EVA with more rapid acetic acid formation will present a harsher environment for the solar cell over the long term due to a slow corrosion of the silver gridlines).
Backsheet
The majority of today’s PV modules still employ a glass/encapsulant /backsheet structure. The backsheet protects against electric shock and electrical faults by providing a mechanically robust, high dielectric barrier over the panel’s back surface. Most backsheets derive their electrical properties from a layer of polyester (i.e. polyethylene terephthalate [PET]) at their core 100 to 300 m (4 to 12 mils ) thick. This core is typically surrounded with an outside layer designed to protect the PET core from UV light degradation and an interior layer which promotes adhesion between the backsheet and EVA encapsulant.
In addition to electrical insulation, typical backsheets have a much lower water vapor transmission rate (WVTR) compared to EVA—this slows the permeation of moisture into the panel (although the package remains breathable resulting in daily and seasonal variation in module moisture levels). Recommended enhanced test procedures for screening backsheet materials include:
– extended UV exposure from both the front and backside of the panel to a cumulative dose of 300 kWh and 200 kWh, respectively (extreme yellowing and/or a loss of backsheet/EVA adhesion on glass-side UV-exposed samples are signs of improper EVA/backsheet combinations; some high-UV EVA types can allow excessive transmission to the backsheet layer if proper precautions are not taken);
– damp heat exposure at 85 C (185 F) /85 percent relative humidity (RH) for 1000 hours as a check for excessive hydrolysis and backsheet yellowing; and
– adhesion strength testing of frame and junction-box (j-box) adhesives to the backsheet before and after damp heat exposure (adhesives with excellent bonds to one backsheet can utterly fail to adhere with another).
Junction box
The j-box provides a strain-relieved transition from the interior laminate conductors to flexible leads terminated with quick connectors. It also houses bypass diodes or, with increasing frequency, more advanced safety/energy conversion electronics.
Standard bypass diode thermal testing establishes the diode maximum expected operating temperature, but does not verify bypass diode functionality/rectification in reverse bias at this temperature. Thermal runaway testing addresses this shortfall by switching the diode, heated from forward operation, immediately back into reverse bias operation to verify thermal runaway does not occur as a result of the elevated leakage current at high temperature.
Extended thermal cycling to 400 cycles is also recommended as it ensures wire seals and potting compounds maintain resistance to moisture penetration. It is not uncommon for wire nuts to become less than finger-tight or for potting compounds to lose adhesion following TC400—both conditions result in capillary channels that wick water into exposed conductors of the junction box.
Key components in a quality approach
Panels from different manufacturers are not necessarily alike, so understanding a few basics can be helpful in selecting a product with the likelihood to provide long-lasting quality. Producing quality solar products involves an ongoing effort of research and development, durability assessment, real-world sustainability, and survival across a multitude of climactic environments. As a result, a company with a proven and longstanding track record will offer the greater chance for success.
To provide customers with all the products needed to take full advantage of the sun’s energy, the manufacturer must possess knowledge of cells, modules, and overall systems, along with a diverse set of solar products. As a renewable energy source, ‘solar’ is the most promising because the planet’s most abundant source of energy is waiting to be harvested for future needs. While the sun’s energy will be constant for eons, the companies in this industry may not.
It is also important to take a close look at the physical properties of a solar panel. True value depends on several considerations when conducting the physical product assessment:
– precision cell efficiency sorting procedures;
– control of wafer source and quality;
– superior performance in high-temperature and low-light conditions; and
– proven long-term reliability with strict soldering and adhesion tests.
Remember, aside from the practical aspects of selecting a reliable solar product, ensuring a cost-effective approach to any solar installation can have a significant impact on one’s clients’ gaining government-sponsored subsidies supporting renewable energy initiatives.
Notes
1 This is a method of rotating inventory so the oldest materials coming in first will be handled first, and what comes in next waits until the first one is finished. It represents a condition that is necessary and consistent with the efficient materials control. (back to article)
2 These components are due diligence all the way as the International Organization for International Organization for Standardization (ISO) 9001, Quality Management Systems. The QMS requirement involves an ongoing, periodic monitoring program to ensure consistency of aspects of manufacturing that may affect safety, performance, and reliability. (back to article)
3 In fact, reliability is neither well-defined, nor covered by the existing IEC standards. The lack of reliability standards is partially due to the fact that, to date, there are not enough statistical data collected from the PV fields. The IEC standard, or even the IEC Retest Guidelines clearly state reliability is not addressed therein, thus the design qualification to those standards does not imply the PV module’s reliability. Therefore, experts from manufacturers, testing houses, and standardization bodies are coming together in an effort to elaborate the basis for a PV reliability standard. (back to article)
Sam Tsou is the vice president of quality management for Motech Industries. His previous positions include vice-president of U.S. sales/marketing at Semiconductor Manufacturing International Corporation, director of customer engineering/planning at TSMC-Wafertech, assistant vice president at Worldwide Semiconductor Manufacturing Co., and general manager of field operations in Taiwan and Singapore for Lam Research. Tsou graduated from the National Taiwan University with a bachelor’s degree in physics. He can be reached at sales_marketing@motech.com.tw.