by Dan Rea
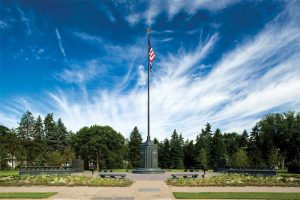
In today’s business climate, the focus on domestic-manufactured products has reached an all-time high. While the discussion of the tariffs for imported goods still remains in progress, decision-makers are faced with carefully weighing all the options. Yet, the process for navigating the choices often proves challenging, as both domestic and imported natural stone are readily available for building projects. Is a North American stone, or an imported one, the right choice for the project? Many times, an international stone is selected based on price, but there are many other factors to consider.
Timeframe and color considerations
A project’s schedule is one of the first factors to consider when weighing domestic and imported stone options. Although the actual fabrication times for natural stone are similar for both domestic and international product sources, transportation from the factory to the project site can be significant with an international quarry or fabrication facility. Ocean voyages can range from three to five weeks, not including delays occurring at the point of origin, or customs at the port of entry.
Keeping these potential delays in mind, a safe timeframe for standard stonework from an international source is 16 to 24 weeks from release of the order. For complex stonework or large pieces, additional time should be allowed. It is important to be cautious on tight timeframes, as it is difficult to expedite any of the process steps if the schedule begins to slip.
On the other hand, a domestic supplier seldom requires more than five to seven days for transport from the factory to the project site. When the project schedule is critical, a North American stone source is essential to ensuring a successful outcome. The supply chain is almost always shorter with a North American source, allowing for better control from the quarry to fabrication facility, or in a best-case scenario, completely controlled by the manufacturer with quarry ownership.
In addition to timeframe, color must be evaluated carefully. Is it a legacy project? Does the stone need to match or complement existing buildings and nearby structures? Then, a domestic stone may be the best source. The stone industry in the United States expanded during the 1980s, when natural stone surged in popularity as a cladding material. In response, many cities established legacy colors around key domestic stones. Today, many projects return to these domestic stone colors to provide continuity in design.
Legacy color
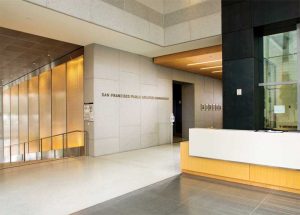
Perhaps one of the best examples of a city with a legacy color is San Francisco. Since the late 1880s, granite quarried from Raymond, California, has been used throughout the city. In downtown San Francisco, many of the classical, historic buildings are clad in pure white granite, and as people walk around the city, many of the curbs are still the original Sierra White granite.
When the San Francisco Public Utilities Commission (SFPUC) needed a new building, the design team wanted to use Sierra White granite to complement the existing architecture. Building the structure called for a combination of styles.
“What we tried to do is to create architecture that appeal to the neo-classical Civic Center Plaza but also is clearly a building that looks to the future—aesthetically and technologically,” said Michael Rossetto, senior associate, KMD Architects. “Additionally, one of the primary goals we had was to build something sustainable—to build something durable and beautiful so you are not compelled to tear it down in 20 years.”
Specifically, the goal was to create a 100-year building, so the materials’ durability was important. Granite was a suitable transitional material between the newer innovations and the civic center’s original design. Additionally, the design called for tremendous use of glass in the building, and the granite provided a good anchor and balance with the glass.
“Our granite fabricator helped us when we were focusing on the technological aspects of the stone,” said Rossetto. “We spent a lot of time studying the different corner joints, the pros and cons on how the stone would meet at the corners, the ability of the stone to be cut and beveled, and anchoring to a curtain wall system. The most rewarding sensation is to look at this monument and know it will be around for another 100 years.”