Painted or anodized finishes
Similar to the curving process, the end application of the part will determine the best practice for how curved parts should be finished. If an extrusion has been painted or anodized, and has been tempered to a T5 or T6 hardness before being curved, the parts will need to be annealed. The high heat associated with the annealing process will likely cause painted finishes to burn and anodized finishes to discolor or craze. For this reason, when parts require annealing it is best to finish them after the curving process has been completed.
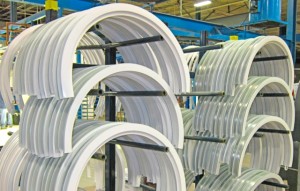
For extrusions tempered to a T1, T4, or T52 hardness, parts can be finished before curving. However, some marring or slight damage to the finished surface should be expected due to the parts being stretched across a hard die surface during the curving process. Depending on the tightness of the radius, anodic coatings may also craze or discolor as a result of being curved. If the T1 or T4 tempered extrusions require oven-aged tempering after curving, the high heat will likely damage the coating.
Regardless of the effect the curving process has on the finish, nearly all manufacturer and applicator warranties are voided when extrusions or brake metal are finished prior to curving. To obtain the best finish quality and keep parts fully warranted, it is best to finish after curving—regardless of the temper of the extrusion.
For parts that require a poured thermal break, it is best practice to have extrusions poured and thermally broken after curving. This helps avoid cracking of the thermal break, and the manufacturers’ warranties stay intact.
To ensure the optimal quality and convenience, some finishers provide a single-source solution where stretch forming, thermal improvement and finishing are synchronized and retain the full warranty. When available, utilizing the finisher’s trucks also can reduce material handling and packaging. Working with a single source not only eases the burden of multiple contacts, it also reduces opportunity for errors and damage, while saving costs and time.
Tammy Schroeder, LEED Green Associate, is a senior marketing specialist at Linetec. She has more than a decade of experience working with architectural aluminum products and finishes. She also develops the company’s American Institute of Architects/Continuing Education System (AIA/CES) programs, and serves on the American Architectural Manufacturers Association’s (AAMA’s) Tactical Marketing Plan Group and Value Proposition Work Group committees. Schroeder can be reached at tammy.schroeder@linetec.com.
Would love to post this article in product news on our website and e-newsletter if we can work out the details!