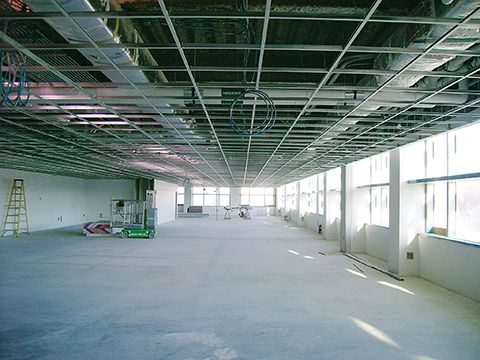
Concrete slabs
There are two main problems with trying to specify an elevation tolerance for concrete slabs supported on a steel frame. First, the elevation tolerance for a concrete slab on structural steel is specifically excluded in ACI 117. This is because the concrete contractor cannot control the elevation of steel on which the concrete slabs are cast. ACI 117 Commentary further explains the architect/engineer should specify, or mutually agree with the contractor, a satisfactory procedure for developing an acceptable tolerance.
Second, finished slab elevation tolerance in relation to the steel frame is not explicitly included in AISC 303 for floors above the lowest level of the structure. The elevation tolerance for the top of a steel beam at each end is to be +4.8 mm (+3⁄16 in.) or −7.9 mm (−5⁄16 in.) from the column finish line, not the proposed slab elevation. Considering the column finish line is also affected by column base plate elevation and column finish length, the slab’s elevation tolerance would typically range in ±19.1 mm (± 3⁄4 in.) deviation from design elevation. This is only valid at each end of the steel beam and is not applicable within its span due to deflection and cambering. Again, the concrete contractor cannot be held responsible for the steel fabrication tolerance of the columns which in turn affects the finished slab elevation.
Specifying flatness and levelness criteria is a little more complicated. Generally speaking, the levelness is a measurement of how much slope is in the floor, and the flatness is a measurement of floor smoothness. Floor levelness and flatness are specified by FL and FF numbers, respectively. The higher the number, the flatter or more level the slab. For example, an FL number of 20 and an FF number of 25 would be adequate for a carpeted office space, but a warehouse with air-pallets would require a FL number of 35 and a FF number of 45.
FL and FF are computed in accordance with ASTM E1155, Standard Test Method for Determining FF Floor Flatness and FL Floor Levelness Numbers, and are typically measured by running a device over the finished floor in both directions in a grid pattern. The device records the levelness and flatness values along the grid and computes an average value. The flatness may also be checked using a 3-m (10-ft) straightedge. With this method, the straightedge is set on the floor, and the maximum value between high and low points is recorded. The straightedge method is considered somewhat outdated, and there is no direct correlation between the value obtained by the straightedge method and an FF value.
The slab levelness numbers (FL) are only applicable to slabs-on-grade and suspended slabs that are shored; they are not applicable to unshored beam construction that deflects or to suspended slabs after the shoring is removed. As explained previously, the contractor cannot be held responsible for deflection of the slab after the shores are removed. The slab deflection is the responsibility of the design structural engineer, and the tolerances are in place to measure the workmanship of the structure’s construction and not deflection.
Figure 3 shows an excerpt from a typical specification for concrete finishes for an elevated slab supported on structural steel (i.e. unshored construction). In this example, the specification wrongly specifies a FL and a grade tolerance for the project.
To add even more confusion to the finished floor tolerance, most architectural finish materials have their own tolerances and state their material finish requirements using the 3-m straightedge values. For example, carpet tile requires a 9.5-mm (3⁄8-in.) gap under a straightedge while ceramic tile requires 3.2-mm (1⁄8-in.) gap.
Thus, if the architect or engineer refers to ACI 117 and AISC 303 for the composite steel-concrete floor construction without any additional requirements, the floor contractor’s workmanship is held to the FF number only for elevated slabs supported on structural steel. To achieve the level floor finish for elevated slabs supported on structural steel, the project specification needs to specify FL and FF numbers only, without referencing the ACI 117 document.
Additionally, elevation tolerance needs to be addressed in the steel erection tolerances rather than in the concrete finish work. Further, concrete slab thickness tolerance needs to be adjusted, due to potential accumulation of additional concrete, instead of directly using the ACI 117 requirement.
Material and design philosophy
In the past decade or so, there have been changes in design philosophy, as well as considerable advancements in material properties for structural steel. ASTM A36, Standard Specification for Carbon Structural Steel, was the most prevalent material type for structural steel shapes years ago. This steel had a specified yield strength of 250 MPa (36 ksi). Most steel mills today are only producing structural steel shapes using ASTM A992, Standard Specification for Structural Steel Shapes, with minimum yield strength of 350 MPa (50 ksi). The increase in steel yield strength has significantly reduced the size of steel members.
Further, since 2000, the International Building Code (IBC) has adopted Load Resistance Factor Design (LRFD) for designing structural steel members. This design philosophy has further reduced the size of structural steel members. The 14th edition of the AISC Steel Construction Manual includes both Allowable Stress Design (ASD) and LRFD.
The reduced section size in steel shapes utilizing the current industry standards can be quite significant. Figure 4 offers an overly simplistic example to demonstrate these changes. It shows how smaller and lighter sections resulted from the high-strength steel and LRFD design. While the beam sections are adequate for strength, beam deflections also need to be checked.
Pre-composition deflection limit is not clearly indicated in current industry standards, but L/240 is generally used. From Figure 4, the first example with AISC’s ninth edition of Steel Construction Manual ASD and 36-ksi steel satisfies the L/240 limit, but the others do not. To meet the deflection requirements, a deep and/or heavier beam would have to be used. This is usually not a viable option due to increased floor-to-floor heights. Instead, beam cambering is used.
Light steel beam sections can also cause another potential construction issue—ponding in fresh concrete placement on the floor. If the steel section is flexible and induces relatively large beam deflection, additional concrete is required to make up the level floor finish. The additional concrete induces more beam deflection, and the concrete ponding effect occurs. While the stiff beam member converges fast in the beam deflection with additional concrete and does not create a concrete ponding issue, the flexible beam member designed with the higher steel strength, LRFD, and larger span length often causes this issue.
Ponding can be significant and can increase the concrete volume up to 30 percent. (For more, see Erika W. Downerys’ article, “Specifying Camber,” from the July 2006 Modern Steel Construction.). Supporting steel members should be designed to resist such additional loads and satisfy any serviceability requirements.
It is really interesting that shored and unshored composite floors use different strength and hardness in the steel beams. It makes sense that you would need a stronger material if you have to support the weight of wet cement. The diagram was really helpful, it made it much easier to follow along with your descriptions. Thanks for the info about composite floors.
You really covered a lot of great points here. Thanks so much for sharing all of this information!