Specifying and installing flashing around exterior wall openings
August 11, 2023
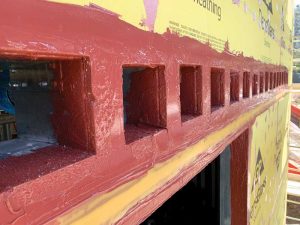
Testing requirements
AAMA 711 provides testing requirements for the following performance characteristics:
- Breaking strength and elongation, previously referred to as “tensile strength” in the 2020 edition of AAMA 711. Both values are tested to a modified ASTM D3759/D3759M-05 (2019), Standard Test Method for Breaking Strength and Elongation of Pressure-Sensitive Tape. After testing, samples are measured by percent elongation to break.
- Water penetration resistance around fasteners. The flashing is adhered to oriented strand board (OSB), plywood, or treated gypsum board. Next, two fasteners, a galvanized roofing nail and a zinc-plated #8 pan head wood screw, are driven through a slotted vinyl shim, through the self-adhering flexible flashing and into the substrate. An open-ended watertight cylinder encircles the area and is filled with water and another container is placed under the assembly being tested. After the test period, if water is found in the bottom container, on the fastener shanks, or on the side or underside of the substrate, the test is reported as a failure. This test is performed both before and after thermal cycling.
- Peel adhesion. The 90-degree peel adhesion test must be performed according to ASTM D3330/D3330M-04(2018), Standard Test Method for Peel Adhesion of Pressure-Sensitive Tape’s Method F
and AAMA 711 requires this testing for adhesion to OSB, aluminum, vinyl, and plywood. However, this test method can also be used to test adhesion
to other substrates. - Accelerated aging with ultraviolet (UV) light exposure. A specimen of self-adhering flashing that has been adhered to anodized aluminum is exposed to a light source per ASTM G154-23, Standard Practice for Operating Fluorescent Ultraviolet (UV) Lamp Apparatus for Exposure of Materials and G155-21, Standard Practice for Operating Xenon Arc Lamp Apparatus for Exposure of Materials. After exposure, the specimen must pass a peel adhesion test per ASTM D3330/D3330M.
- Elevated temperature exposure. A specimen consisting of self-adhering flashing applied to anodized aluminum is exposed to an elevated temperature for seven days. After exposure, the specimen is re-conditioned to standard temperature and a peel adhesion test is performed per ASTM D3330/D3330M.
- Thermal cycling. A specimen is exposed to a high temperature for eight hours, followed by a low temperature for 16 hours. This cycle is repeated
10 times and after cycling, the specimen must pass a peel adhesion test per ASTM D3330/D3330M. - Cold temperature pliability. This test is performed per ASTM D1970/D1970M, C734-15(2019), Standard Test Method for Low-Temperature Flexibility of Latex Sealant After Artificial Weathering, or C765-97(2015), Standard Test Method for Low-Temperature Flexibility of Performed Tape Sealants and should reveal no cracking or loss of adhesion to the panel.
- Adhesion of self-adhering flashing after water immersion. A peel adhesion test is performed per ASTM D3330/D3330M over one half the bonded length of a specimen and then the specimen is immersed in water for seven days. After immersion, a second peel adhesion test is performed. Adhesion levels are examined and any apparent swelling or change in appearance or contour is noted.
- Peel resistance. This test method is used to determine the resistance of self-adhering flashing to peeling from itself. This procedure is detailed in Annex A of AAMA 711.
Got News? Click here to share your story!