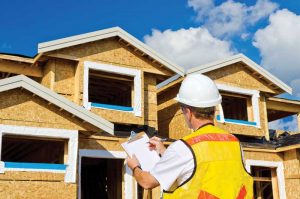
Since the outdoor temperature at the time of installation can affect performance and adhesion levels, manufacturer-provided installation temperature ranges should be followed. If the installer must work outside of the recommended range, the flashing manufacturer must be consulted.
Many manufacturers recommend primers compatible with their products and specify how they should be used. For less-than-ideal conditions such as very low temperatures, dusty conditions, or rough surfaces, primers are an effective way to enhance the adhesion of self-adhering flashing.
Bubbles, wrinkles, and blisters all increase the risk of water intrusion. Many manufacturers recommend using rollers to help installers avoid these application inconsistencies.
The release liner backing should be removed immediately prior to installation to avoid contamination of the adhesive surface and loss of its properties. As best practice, the number of penetrations through the flashing should be minimized.
Self-adhering flashing products can also be used as sill pans to divert incidental moisture that enters the rough opening cavity to the exterior drainage plane. In this situation, it is possible that standing water can collect on the self-adhering product. Care must be taken to ensure proper damming at the jambs and interior portion of the sill (rear upturned leg) to direct the standing water to the exterior. Sloping the sill to the exterior is recommended. Installers should ensure the sill pan is integrated continuously with the WRB and that penetrations, seams, or other discontinuities do not allow water intrusion through the sill pan.
Liquid-applied flashing
Like all FGIA published standards, AAMA 714 was developed in an open and consensus process. It establishes the minimum performance requirements for liquid-applied flashing, which is used to create water-resistive seals around exterior wall openings in buildings. This includes fenestration products such as windows, doors, and skylights as well as other through-wall penetrations.
Specifiers can use this information to evaluate and select the appropriate liquid-applied flashing materials for their project, based on three different levels of heat exposure classification.
AAMA 714 recognizes that certain local codes and regulations may take precedence. All products must meet regulatory volatile organic compound (VOC) content requirements and other environmental considerations. In addition, proper personal protection equipment (PPE) should be used when handling liquid applied flashing.
Prior to performing any tests, the liquid applied flashing must be allowed to fully cure per the manufacturer’s instructions.