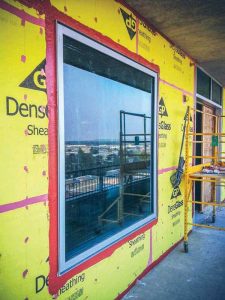
Sealants, adhesives, and other building materials that come in to contact with liquid-applied flashing must be chemically compatible. Always check with the product manufacturer(s) to confirm compatibility. This could also be confirmed through testing in accordance with AAMA 713 where necessary.
Installation guidelines
Successful flashing performance depends on adequate adhesion between the flashing and the substrate it is adhered to, as well as the installation conditions. The flashing product must be used in a way that allows it to remain attached to the substrate while maintaining a moisture seal throughout its service life. AAMA 714 includes optional recommendations for field applications. The information in Appendix A should be considered optional and are intended to address field application, not laboratory.
When using a liquid-applied flashing product, the following issues should be considered:
- Where the product is used (i.e. on a wall or a flat surface, such as a sill)
- The presence of dust, dirt, or other contaminants
- Moisture conditions
- Fastener penetrations
- Installation issues, for example blisters
or non-adhered areas - Temperature conditions
AAMA 714 Appendix A provides a table which the flashing manufacturer can fill out to indicate the lowest temperature at which the specific liquid-applied flashing product provides an adhesive bond strength of at least 0.9 newtons per mm2 (5 lb per linear in.) to the substrates indicated. If a product must be installed at temperatures lower than what is recorded in the table, then an adhesive/primer should be used as an aid.
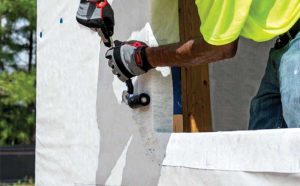
When an adequate adhesion is not achieved at any temperature, which is often the case for loosely bonded surfaces such as fiberglass-coated gypsum board, the flashing manufacturer is permitted to indicate “use adhesive primer” in the table, in place of a minimum temperature. If this is provided in the table, users of liquid-applied flashing are advised to take caution as the effectiveness of the flashing depends on the temperature at which it is applied. AAMA 714 Table A1 provides a means to request the lowest temperature to achieve minimum adhesion for the following substrates:
- OSB
- Plywood/wood framing and studs
- PVC (classifications 1-4)/ABS
- Fiberglass-coated gypsum sheathing
- Fiberboard; fibrous sheathing board
- Bare metal surfaces; aluminum/steel/others
- Aluminum with primed/painted surface
- Steel with primed/painted surface
- WRB building paper, asphalt impregnated
(all weights) - WRB felt paper (all weights)
- WRB – polyolefin
- WRB – films/coated laminates
- Concrete masonry unit (CMU)
- Poured concrete
- Foam-insulated sheathing
- Exterior gypsum board (not fiberglass coated)
- Laminated fiber sheathing board