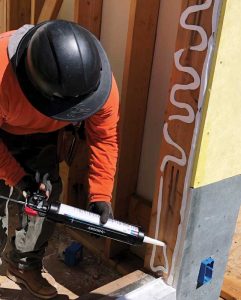
As noted previously, OSB and fiberglass can provide a highly variable or loosely bonded surface, resulting in difficult adhesion conditions without the use of a primer. For liquid-applied flashing, the same applies to fiberboard. As a highly variable substrate, it is difficult to predict the adhesion performance of liquid-applied flashing products to OSB. Although adequate adhesion is often achievable on warm, dry OSB, it is generally advisable to use an adhesive/primer.
Common in the southeast U.S., exterior stucco facade is often directly applied to CMU walls without the use of a drainage cavity (surface barrier wall system). For these applications, it is essential to have a strong bond between the stucco and the CMU wall. When a liquid-applied flashing is used, it should not act as a bond break to the stucco. Consequently, provisions are made either in the formulation of the liquid-applied flashing or with a secondary application of an adhesion promoting substance for the direct applied stucco.
Meeting a growing need
With the increased application of self-adhering and liquid-applied flashing for water protection, these updated standards come at an opportune time.
“Liquid-applied flashing products are realizing increasing application for sealing building interfaces, including flashing around windows and doors,” says Jim Katsaros, chair of the FGIA Flashing Committee.
AAMA 711-22 and AAMA 714-22 are referenced in both the International Residential Code (IRC) and the International Building Code (IBC) as a requirement for using these materials in door and window flashing applications.