Specifying architectural zinc
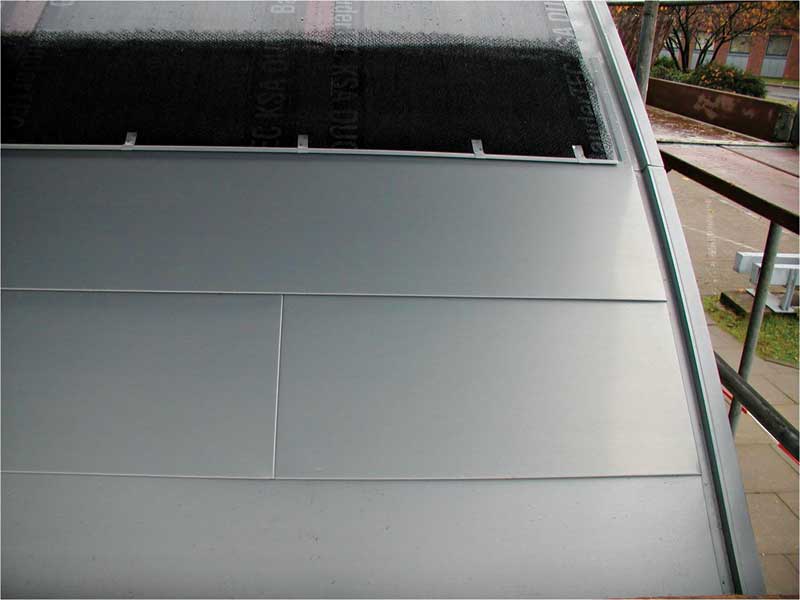
Zinc roof design considerations
Long before the specification is written, the groundwork for a 100-year zinc roof should be laid. Good zinc design may be facilitated by a specification writer who understands the metal and is involved by the design team early in the process.
Slope
Steep slope is the best roof design strategy an architect can provide. While three degrees (5/8 in 12 in.) can be an acceptable roof pitch, it does not make any zinc joinery or profile acceptable. Double-lock standing seam (DLSS) is the most popular zinc roof panel application and is the required joinery for the low-slope zinc applications (often with in-seam sealant). There can be exceptions, as a limited section of a barrel roof will demonstrate.
A coping is theoretically a hybrid low-slope roof and façade panel in one application. Seaming and expansion details for coping applications can be easy for those who understand zinc. As the roof pitch becomes lower, the durability can be reduced as the zinc ion loss is elevated. Large roof areas without a lot of slope (e.g. < 3/12 pitch) may require an engineered standing-seam system. Designers should consult a zinc manufacturer for recommendations. (Zinc is a reactive metal and those atoms at the surface of the zinc sheet are more vulnerable to atmospheric influences. Zinc ions are formed as atoms at the surface lose electrons through the interaction with oxygen, water, etc. These charged ions have a weaker bond to the sheet surface and can sometimes be removed by rainwater(some remain to complete the patina process).
Expansion and contraction
Zinc alloy has a high coefficient of expansion. Indirect attachment with concealed clips is the preferred attachment method for any panel. For those longer than 3048 mm (120 in.), this becomes more important. All zinc profiles should be ‘fixed,’ but only for a short distance—914 to 1219 mm (36 to 48 in.) is a good rule of thumb.
Locating the fixing zone will depend on the roof slope. Steep slopes require fixing the panels closer to the ridge allowing more downslope movement. While fixing a 4000-mm (157-in.) panel in one climate may work, the same application executed in a different location, exposure, or season will produce different aesthetic results regarding panel waviness. Attachment of all zinc panels should accommodate panel movement of approximately 6.3 mm (1/4 in.) per 3048 mm (120 in.) per 55-C (100-F) temperature change. The total design temperature fluctuation should be 67 C (220 F).
Above-sheathing ventilation
In some respects, zinc roof applications may look familiar to rainscreen or ‘drain-screen’ façade designs. Zinc roofs should not be the primary waterproof ‘barrier.’ Instead, zinc roof profiles should be applied as a ventilated dry-joint cladding or a ‘rainscreen roof’ strategy. This design alternative allows for pressure equalization, backside drying, and moisture escape, rather than damaging the zinc (or creating a roof leak).
While the airflow may be limited and the ‘ventilation’ label overstated, an 8- to 10-mm (3/10- to 4/10-in.) structured underlay comprising entangled nylon wire that elevates the zinc—keeping the profile underside dry— should be used. Substitution of this air space and capillary break with a backside paint coating or other ‘barrier’ strategy should never be accepted. Above-sheathing ventilation mats must be a requirement of every zinc roof assembly.
Roof underlayments
Synthetic felts applied with cap nails can provide fewer seams and better weather protection than conventional #30 felt. Self-adhered high-temperature (HT) roof underlayments are often specified at vulnerable roof conditions (e.g. perimeters, penetrations, and valleys) where openings in the deck are found. Other underlayment properties to specify include:
- good slip resistance;
- unreinforced membranes for better self-sealing capabilities;
- good adhesion; and
- extended exposure time (i.e. three to six months).
Red rosin paper and any other moisture-holding materials should be prohibited in every zinc application. Moreover, forbidding use of red rosin paper within any zinc application should be cited in every zinc (and zinc-coated metal) specification.
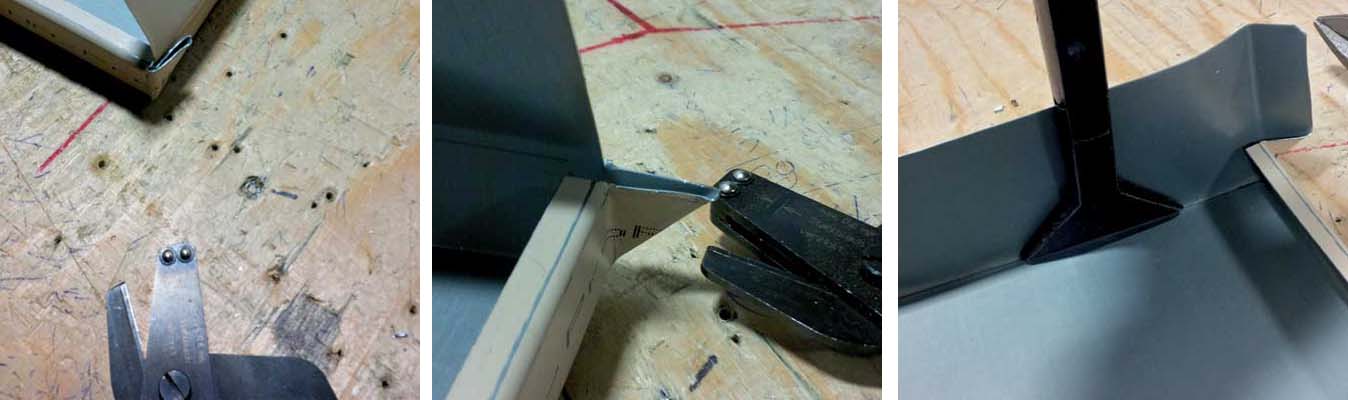