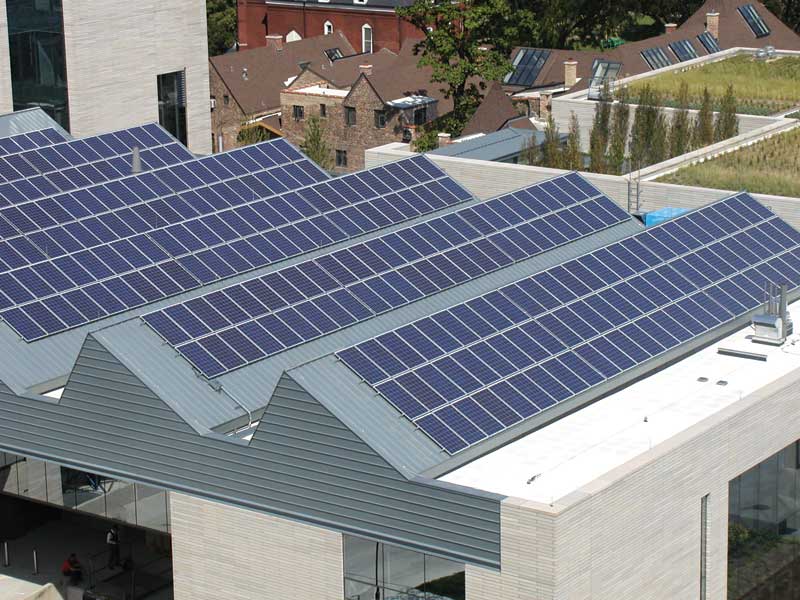
Assembly components
All attachment components should be fabricated from stainless steel (Type 304) or exterior-grade polymer-coated steel.
Fasteners, clips, and cleats
Fasteners for panel clips will typically be #10 screws, at least 25 mm (1 in.) long with a drill point appropriate for the substrate (e.g. plywood, 1x lumber, or steel decking). With so many fastener penetrations, specifying an added waterproof membrane gasket under each clip base can be
an added option for leak prevention. Generally, exposed rivets or screws connecting two zinc profiles should be avoided unless specifically approved by the architect in advance.
Concealed clips should be fabricated from light-gage (26 to 28 ga.) type 304/316 stainless steel. The thin metal section is important to reduce resistance during the final seam-closing operation. This lighter design may also increase clip length or decrease clip spacing to achieve uplift requirements. Two-piece expansion clips designs vary (butterfly and hooked designs are common) and offer different levels of wind resistance. Clips should allow the roof panel to move freely during periods of thermal stress. A 110 C (200 F) temperature change for the zinc should be considered, which in extreme conditions translates to 3.2 mm/m (50 mils/ft). Based on metal temperature at the time of installation, the contractor should calculate the maximum movement and ensure panel ends do not disengage or ‘bottom out’ in extreme conditions. Clips can be sized to equal the sum of the vertical seam plus ventilation mat, or match the seam dimension (compressing the mat).
Concealed offset cleats used to retain the leading edge of the panel should be corrosion-resistant metal (stainless steel, coated steel, or zinc) sized appropriately, often 22-ga. metal and attached with the appropriate fastening method (often screws). To facilitate moisture drainage from the vented space, the roof panel should have a soft bend past the cleat that produces an acute angle and finishes parallel to the ground (rather than a closed panel return). This open hook promotes water drainage from the end pocket formed by the panel hook. Zinc profile end folds should also be ‘soft’ with the raw zinc edge parallel to the ground and not closed tight. Final instruction for clip and cleat material thickness, sizing, spacing, fastener pattern, and spacing requirements should be confirmed by a licensed engineer.
Sealants and solder
While a zinc profile will not allow the passage of water, the joinery can be compromised if the seam is not properly designed or executed. On occasion, the forces that move water ‘uphill’ can also cause a leak to appear. It is possible for a properly lapped water-shedding zinc connection to leak. The solution may or may not be to waterproof the joint with sealant or solder. Concealed sealants often create more problems for zinc than they prevent. The zinc manufacturer should be consulted for any proposed use of tube or tape sealants within laps or other concealed applications.
Excessive use of sealants by an unsuspecting contractor can plug weep holes, limit airflow, trap moisture, create adverse reactions, or restrict the metal’s movement. In-seam sealant at the top of the vertical seam is rarely a problem; it is recommended when the roof slope drops below 2/12. One should specify a non-curing butyl sealant for any moving joints. For other high-point termination conditions where weeping cannot occur, a zinc-compatible pH-neutral sealant can be used.
Due to the high coefficient of expansion of zinc, limited details should be soldered. When a small roof area requires a permanent waterproof connection, soldering may be a solution after consulting the zinc manufacturer. The keys to successfully soldering zinc include:
- surface prep and zinc-specific flux;
- 50/50 solder (or silver solder for a lead-free solution); and
- a ‘cool’ iron (i.e. no open flame torch).
Strength in the solder joint is achieved by the solder concealed in the tight space between the two layers of zinc. The joint overlap should measure only 13 mm (½ in.) so solder flow can be seen on the back side. Plumbing vent flashings, chimney crickets, and gutter joints are zinc roofing details that are soldered.
Rigid insulation
Insulated metal deck roof assemblies are also possible for zinc. Nailbase insulation composite
or structural insulated panels (SIPs) can provide a solid substrate (e.g. oriented strandboard (OSB) or plywood) to attach the panel clips. In the absence of a nailable substrate, rigid insulation (at least 172-kPa [25-psi] polyisocyanurate [polyiso]) with metal bearing plates matching the seam clip pattern can be fixed to the metal deck. The steel bearing plates will compress the ventilation mat when fastened to the structural deck and help distribute the compressive load of the seam clips. The size, metal thickness, and spacing of the bearing plates should be confirmed by the system fabricator as recommended by the zinc manufacturer.