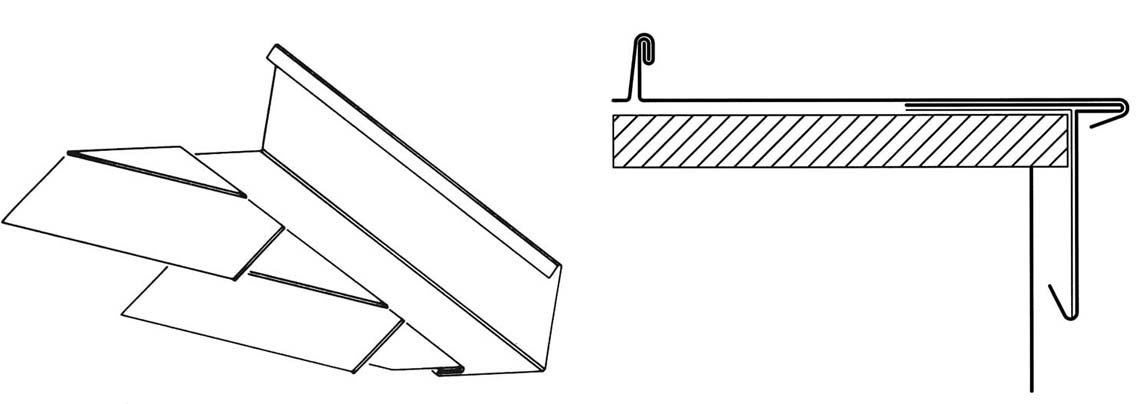
Panel surface textures
A vertical seam roof panel oriented perpendicular to the eave will reveal oil-canning (i.e. panel waviness). This aesthetic phenomenon should be expected and is not a cause for rejection. In normal cases, zinc is a metal that will never achieve a truly flat surface. Although a smooth zinc panel surface without intermediate bends is the norm and will provide a more traditional look, any of the following measures can help minimize oil-canning:
- increase zinc thickness from 0.7 mm (27 mils
[24 ga.]) to 0.8 or 1 mm (31 or 39 mils); - reduce the panel width (304 mm [12 in.] is often the narrowest seen);
- add additional bends within the pan (e.g. striations, stiffening ribs, pencil ribs);
- select a pre-weathered treatment providing a gray aesthetic (rather than mill-finish zinc);
- tension-level zinc sheet and coil prior to fabrication; and
- add an embossed texture/pattern (e.g. stucco, pebble, woodgrain, or any raised design).
Specifying crafted-metal details
A big advantage of soft, natural-weathering metals is malleability. With the ability to fold the metal rather than ‘cut and caulk,’ zinc allows knowledgeable craftsmen (and architects) to execute project details that will last the lifetime of the roof. Providing water-checks (soft hems) is an easy way for every architect and contractor to make it more difficult for water to get into the building. Cut metal edges should typically not be allowed. Premium metal-working tools help make the execution of many crafted-zinc details not only possible, but also easier. One should consult a zinc mill for recommendations.
Vertical-seam panel closures: Bread-pan ends
Folding the zinc rather than relying on J-channels and sealant to close off the roof panel end is a fail-safe detail. ‘Bread-panning’ is a crafted metal technique used to create a folded ‘dog-ear’ or ‘boxed’ end.
The best way to eliminate the possibility of roof leaks at the up-slope end is to fold a vertical seam across the pan’s width. Requiring ‘folded’ zinc detailing eliminates the need for cuts, rivets, sealant, or solder at the ridge termination or at the head flashing details.
Changes in plane: The ‘pinched’ seam
Pitch-break transitions (or vertical roof-to-wall transitions) can expose the weaknesses of many rigid roofing materials. Zinc’s ability to be folded allows it to retain the weatherproof integrity of the vertical seams without cutting the profile. This dry-joint technique provides a designed solution that does not rely on sealant. Execution involves:
- straightening of the vertical seams and ‘twisting’ the flattened metal legs with needle-nose pliers;
- a pan ‘crease’ along the pitch break line to keep the standing seam panels in alignment; and
- folding and ‘tucking’ the overlapping metal to shed water to effectively eliminate the need for cutting the roof panel—which can expose the roof to more termination points and the potential for leaks.
Roof edges: Valley pans, ridge caps, and eave terminations
Intersecting roof planes with opposing slopes are vulnerable details. Improvements to the traditional valley profile design can help make this condition a lifetime solution. Valley pans collect and direct water toward the roof edge. An improved zinc valley will include:
- ventilation mat underlays (as required for
roof panels); - a W profile at valley centerline (for lateral expansion and better water management);
- a wide-open valley channel (at least 152 mm [6 in.] each side of centerline);
- clip attachments (allowing movement and eliminating any pan penetration);
- soft bend water-check ends;
- integral S-fold cleats or non-penetrating soldered cleats;
- an extended distance between cleat and watercheck; and
- a profile step 50 mm (2 in.) below the cleat.
The top of the roof is where the water, wind, and blowing snow can create havoc for zinc or any roof. Attention to function and aesthetics is especially important for a zinc roof expected to last for generations. Consulting with a zinc manufacturer may expose the design team to new ways to solve common metal roofing issues with more style.
Soldered pipe boot
Long-term and watertight plumbing vent penetrations are possible with natural metals like zinc. Specifying a prefabricated or field-fabricated zinc flashing boot soldered to the roof pan will provide a durable and watertight solution. Eliminating rubber boots, fastener penetrations, and sealants is an important aesthetic and durability consideration, while soldered zinc flashings are another specification requirement.
Other panel preparations should include communicating with the plumbing contractor so penetrations occur in the panel center without interfering with standing seams. Peening the panel cut prior to soldering the boot also provides a secondary water check for added protection.