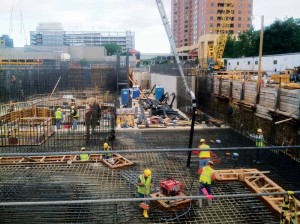
62,053 kPa (9000 psi).
Photos courtesy GRT Admixtures
Fly ash and LEED milestones
The $53-million Boulder Community Foothills Hospital (Colorado) was the first hospital in the U.S. to receive LEED-NC. With a LEED Silver rating, the 18,580-m2 (200,000-sf) facility contains many sustainable features, including a concrete mix incorporating 25 percent fly ash to improve durability, enhance performance, and obtain LEED points for recycled content. The cast-in-place concrete structural system used for the hospital building frame and floor systems was selected based on functionality and environmental impact considerations.
Concrete strengths included:
- 20,684-kPa (3000-psi) foundations;
- 27,579-kPa (4000-psi) columns;
- 34,474-kPa (5000-psi) floor slabs; and
- 41,369-kPa (6000-psi) concrete core and shear walls.
The use of locally produced concrete eliminated the environmental impacts of transporting it from other regions and helped the design team achieve its performance, cost, and sustainability goals. The project obtained a total of 33 LEED points, including five points for a 35 percent improvement in energy performance over American Society of Heating, Refrigerating, and Air-conditioning Engineers (ASHRAE) 90.1, Energy Standard for Buildings Except Low-rise Residential Buildings.
The first hospital to receive LEED Platinum, Dell Children’s Medical Center of Central Texas, also relied on fly ash to achieve its performance and sustainability goals. As part of its LEED effort, the project team made the most of the $200-million facility’s location on a brownfield site originally part of a former airport in Austin, Texas. Approximately 47,000 tons of runway materials were reused onsite, and the building’s concrete mix incorporated 40 percent fly ash in the 31,347 m3 (41,000 cy) used for the foundation and walls. During construction, 92 percent (more than 32,000 tons) of waste was recycled. Additionally, local building materials were used on the structure’s exterior.
On the same brownfield site is the adjacent Ronald McDonald House of Austin, which provides nurturing programs and a supportive home-like environment for families while children receive treatment in local medical centers. Sustainable design elements that qualified the 2648-m2 (28,500-sf) facility for LEED Platinum included:
- building products selected for their contribution to a healthy indoor environment;
- construction materials procured within an 800-km (500-mi) radius of the site; and
- use of concrete containing fly ash for structural components.
Ternary blends: the right prescription for Gundersen Lutheran and Mayo ClinicOne of the largest healthcare construction projects in Wisconsin, Gundersen Lutheran Health System’s campus renewal initiative in La Crosse includes a new six-floor hospital designed to meet LEED-HC standards. Many of the project’s construction materials are being produced locally, including the concrete supplied by La Crosse-based River City Ready Mix.
Work on the 37,161-m2 (400,000-sf) hospital began in January 2011 and is scheduled to be completed late this year. The 15,290 m3 (20,000 cy) of concrete placed for the slab, walls, and other structural applications relied on a ternary mix design of 20 percent slag cement, 15 percent fly ash, and 65 percent portland Type I/II. This enabled the material to achieve specified strengths of 31,026 kPa (4500 psi) at 28 days.
About 120 km (75 mi) from La Crosse, the Mayo Clinic is building a 10,220-m2 (110,000-sf), $188-million proton beam therapy center in Rochester, Minnesota. The specialized cancer treatment center’s design includes 14,847 m3 (19,419 cy) of concrete containing a ternary mix of 33 percent Type I/II portland cement, 33 percent fly ash, and 33 percent slag cement to achieve a low heat of hydration and 28- and 56-day strengths exceeding 62,053 kPa (9000 psi) for the multiple mass concrete placements.
In March 2012, crews from Rochester-based Ready Mix Concrete placed 1246 m3 (1630 cy) of concrete for more than eight hours to complete a base slab 20 m wide by 57 m long by 1.1 m deep (66 by 187 by 3 ½ ft). Two months later, this was followed by the ‘big pour’—the largest in the history of Rochester—that involved more than 500 truckloads of concrete. Over the course of 28 hours, three pumps were used to place 4205 m3 (5500 cy) of concrete for the mass concrete foundation walls, the thickest of which measured 6.6 m wide by 4.3 m high (21 ft, 9 in. by 14 ft). The first treatment rooms are expected to be open in the summer of 2015.
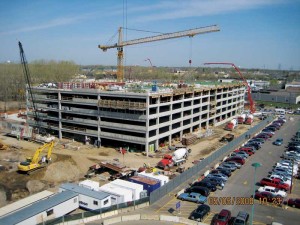
Green medical facilities going beyond hospital walls
While healthcare organizations are demanding sustainable design and construction as a matter of course, green building is no longer limited strictly to hospital projects. Sustainable building materials and design options with low carbon footprints are being prioritized to minimize environmental impacts and safety concerns, as well as achieve operational and wellness goals, throughout the medical campus, including parking facilities, ramps and sidewalks, healing gardens, and other specialized applications.
On Gundersen Lutherans’ campus, a new three-level underground parking ramp was designed with many green qualities, including concrete containing a silica fume-portland cement blend to achieve a life expectancy of 100 years. Park Nicollet Methodist Hospital in Minneapolis also relied on a silica fume-portland cement blend for the concrete in the post-tensioned decks of its 55,742-m2 (600,000-sf) parking garage, as well as for loading docks and sidewalks to ensure a durable surface that can withstand snowplows and harsh de-icing chemicals.
Slag cement is also increasingly being specified in sustainable parking structures, such as the transit center serving Tuality Hospital and Pacific University’s Health Services campus in Hillsboro, Oregon. More than 4205 m3 (5500 cy) of concrete containing slag cement were used in the columns around the perimeter, the post-tensioned cast-in-place concrete beams, and post-tensioned concrete elevated decks in the parking facility.