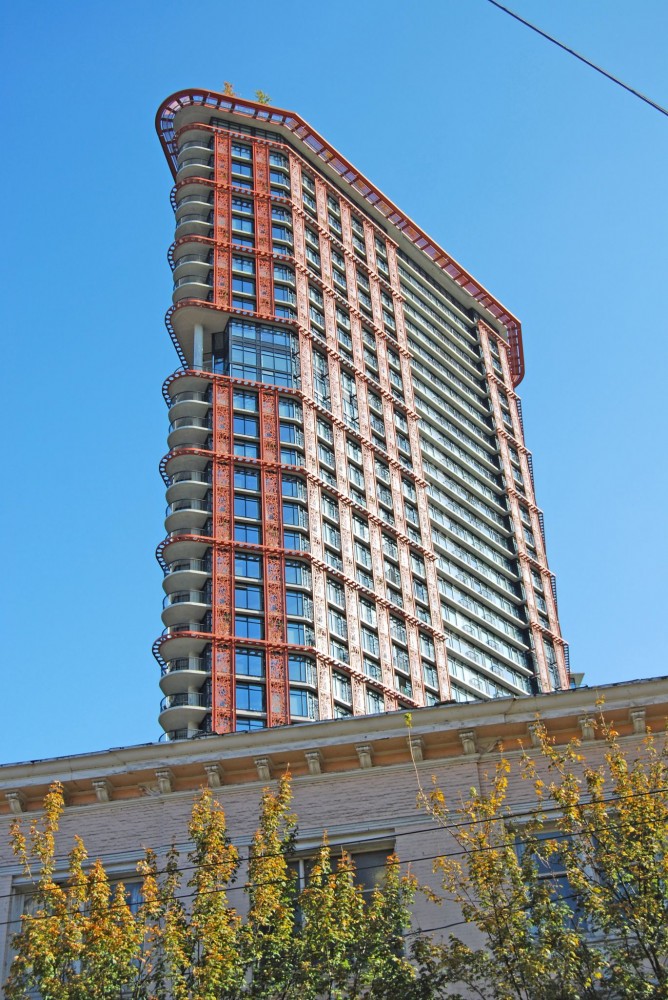
by Melissa Lindsley
Brightly painted stadiums in team colors, rainbow-hued artistic sculptures, instantly recognizable safety markings—all these items can be hiding a powerful secret beneath their vibrant paint or powder coatings: hot-dip galvanized steel.
Hot-dip galvanizing is the process of dipping fabricated steel into a kettle or vat of molten zinc. The process is inherently simple, which provides a distinct advantage over other corrosion protection methods. While the steel is in the kettle, the iron in the steel metallurgically reacts with the molten zinc to form a tightly-bonded alloy coating that provides superior corrosion protection to steel. In the duplex method discussed throughout this article, the hot-dip galvanized steel adds the benefit of durable, low-maintenance corrosion protection beneath a superficial coating.
Though many people are familiar with one or the other type of corrosion protection system, few realize the intrinsic value of using both in tandem—a duplex system—to grant a project the protection of hot-dip galvanized steel, while allowing a desired color/aesthetic using paint or powder coating.
It is a common misconception to think painting or powder-coating over galvanizing is difficult or not worth the extra step. To the contrary, it is often possible to duplex with minimal additional effort, and the results can greatly extend the project’s life. A duplex system can withstand some of the toughest environments imaginable, with little to no maintenance. In fact, due to the synergistic effect, a structure can last up to 2.5 times longer, maintenance-free, by incorporating a duplex system. By following a few simple preparation steps outlined in ASTM specifications, a galvanized piece can be painted or powder-coated to meet any color requirement.
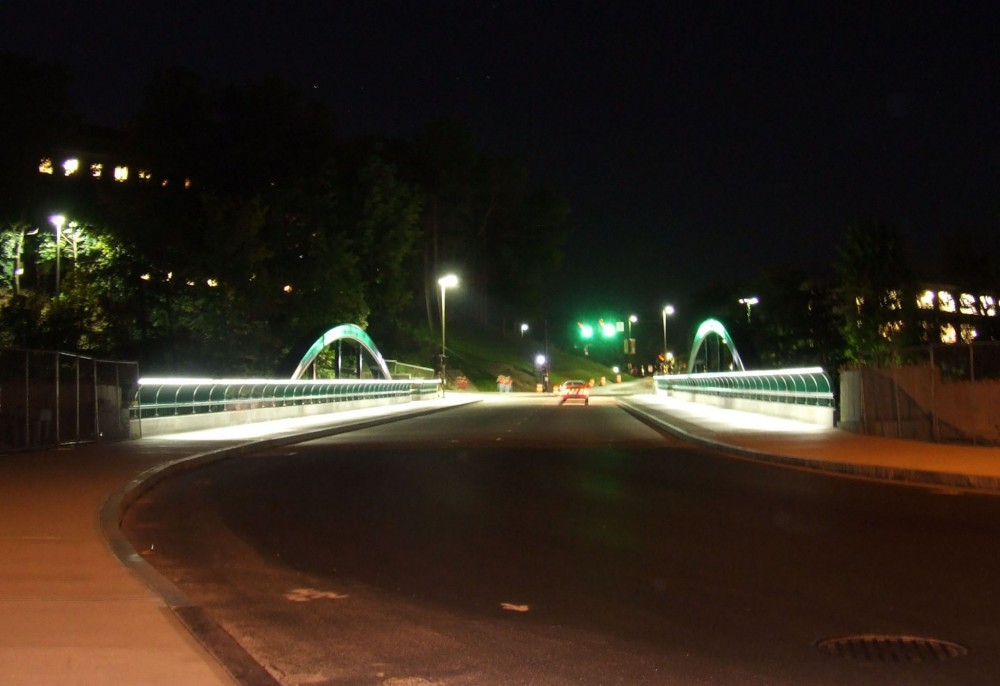
Duplex applications
A duplex system can be applied to structures from public and private sectors; everything from radio towers, bridges, pipes, stadium structures, and artistic sculptures can successfully implement a system of paint or powder coating over galvanized steel. Specifiers may elect to call for duplex for numerous reasons, but ‘aesthetics’ is often the chief one. For instance, many sport stadiums want to take advantage of durable hot-dip galvanized steel, but need to feature team colors in the stands or bleachers. Painting or powder coating over galvanized steel allows the best of both worlds.
Perhaps the structure is meant to blend in to the surroundings, or maybe to stand out with a vibrant color, as with the Chinatown Park Entrance Gate. Duplexing opens up a world of visual options, without sacrificing low-maintenance corrosion protection.

A duplex system also might be used to accommodate safety regulations. Duplexing can enable color-coding of gas, steam, or chemical pipes. It can also identify hazardous work areas and walkways, and mark high-voltage electrical lines and equipment. For example, the Federal Aviation Administrations (FAA) requires structures taller than 61 m (200 ft) to be painted in the alternating pattern of white and international orange. Duplexing these types of projects will ensure the proper color-coding is in place without sacrificing corrosion protection on often difficult to maintain structures.
Perhaps more important than superficial appearance concerns, an overlooked benefit of duplexing is the extended corrosion resistance. When galvanized steel is painted or powder-coated, the system provides a more sophisticated manner of corrosion protection through a synergistic effect. The exterior layer of paint or powder coating provides barrier protection to the underlying zinc coating, slowing down the rate at which it is consumed to greatly extend the galvanized steel’s life. In return, once the exterior layer has been weathered down or damaged, the hot-dip galvanized coating beneath is still available to provide both cathodic1 and barrier protection to the base steel.
As a result of the two systems working in synergy, the substrate steel is granted corrosion protection for 1.5 to 2.5 times the sum of the expected life of each system alone. With ‘M’ representing the length of time to first maintenance, this can be mathematically shown as:
Mduplex = 1.5 to 2.5 (Mgalvanizing + Mpaint)
For example, if a galvanized coating alone on black steel would provide 50 years of protection before maintenance, and a paint coating for 10 years,2 then the combination duplex system would provide maintenance-free protection for 90 to 150 years.
It is important to remember this equation assumes no maintenance will be performed on the paint or powder coating and, as it naturally wears away, the underlying galvanizing would provide the majority of the corrosion protection. This is only likely to be applied in theory, however—in practice; the project owner will maintain the topcoat system to preserve the aesthetic appearance. Therefore, in practical terms, the synergistic effect is realized in the delayed maintenance cycle (1.5 to 2.0 times the cycle on bare steel) of the paint/powder top coat of the duplex system. This extended maintenance cycle translates to less capital spent on routine maintenance and upkeep, as there are fewer maintenance cycles required.
In fact, there are tremendous economic advantages provided by using a duplex system—the extended time to first maintenance and delayed maintenance cycles contribute considerable savings over the project’s life. Initially, the cost of a duplex system can be significant because of the expense for both corrosion-protection systems. Nevertheless, the synergistic effect means the initial costs are quickly amortized over the life of the project and, in the end, are less expensive than coating bare steel. Also, if the duplex system is used solely to prolong project life and color finish is not critical, the initial cost can be the final cost.
Implementing a duplex system
Achieving the benefits of a duplex system only requires a little extra planning and effort. First, it is important to communicate with the galvanizer, forewarning of the plan to paint or powder-coat afterward. This way, the galvanizer can ensure the pieces will not be post-treated (i.e. quenched), and any coating imperfections are remedied before the topcoat’s application.
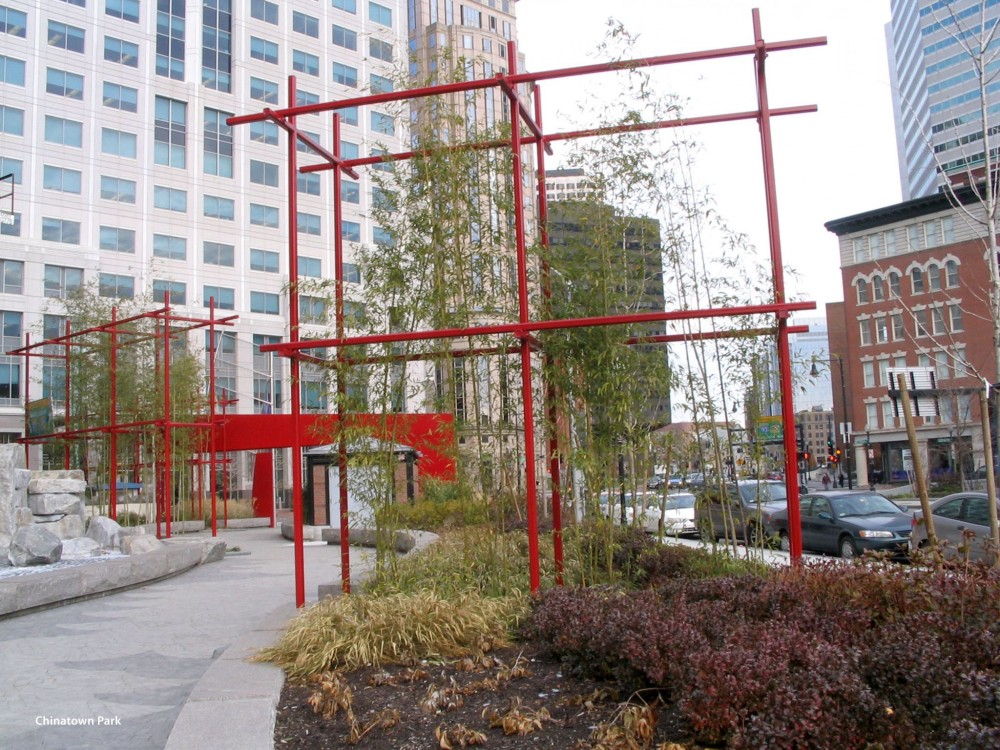
Before preparing the steel for paint or powder, it is critical to determine the age and condition of the galvanizing coating. As it ages, zinc corrosion products build on the surface, naturally developing what is known as patina. When a fresh zinc coating of galvanized steel is exposed to oxygen and moisture, it forms loosely attached particulates of zinc oxide and hydroxide. Since these particles can be dissolved in water, the duplex may have adhesion problems if a coating is applied at this point without preparation.
The surface prep required for a successful duplex system is dictated by the stage of patina development, defined as:
- newly galvanized: little to no zinc oxide on the surface, typically found within 48 hours of galvanizing;
- partially weathered: combination of zinc oxide and zinc hydroxide, usually present from two days to six months after galvanizing; or
- fully weathered: fully developed zinc patina consisting of zinc carbonate, typically develops about six months to two years after initial galvanizing (depending on climate) and has a rougher profile that should not be removed before painting.
Both ASTM D6386, Standard Practice for Preparation of Hot-dip Galvanized Steel for Painting, and D7803, Standard Practice for Preparation of Hot-dip Galvanized Steel for Powder Coating, provide detailed information on surface preparation techniques—including cleaning and profiling—for all ages of galvanized steel. It is important to note the process to prepare a galvanized surface differs significantly from preparing a bare steel surface for paint/powder coating.
Once proper preparation steps are completed, specifiers must choose a paint or powder coating system compatible with the galvanized coating. For both cases, it is important to discuss compatibility with the manufacturers. When powder-coating, requirements for the finished project must be outlined. Will it be exposed to road salts and chemicals? What about ultraviolet (UV) rays?3 One must discuss potential performance challenges before making a selection. Pairing the correct paint or powder coating will lead to structures that withstand the test of time.
Another hidden benefit of using a duplex system is the ease of touchup to the paint or powder coating. When performing maintenance on paint or powder coatings applied to bare steel, there is often corrosion, requiring tedious cleaning prior to repainting. When the structure has a ‘primer’ of hot-dip galvanized steel, there is no corrosion present where the paint/powder coating has failed because the zinc has simply begun protecting the steel. The exposed zinc surface can be painted over with minimal surface preparation and without the risk of underfilm corrosion spreading from the area.
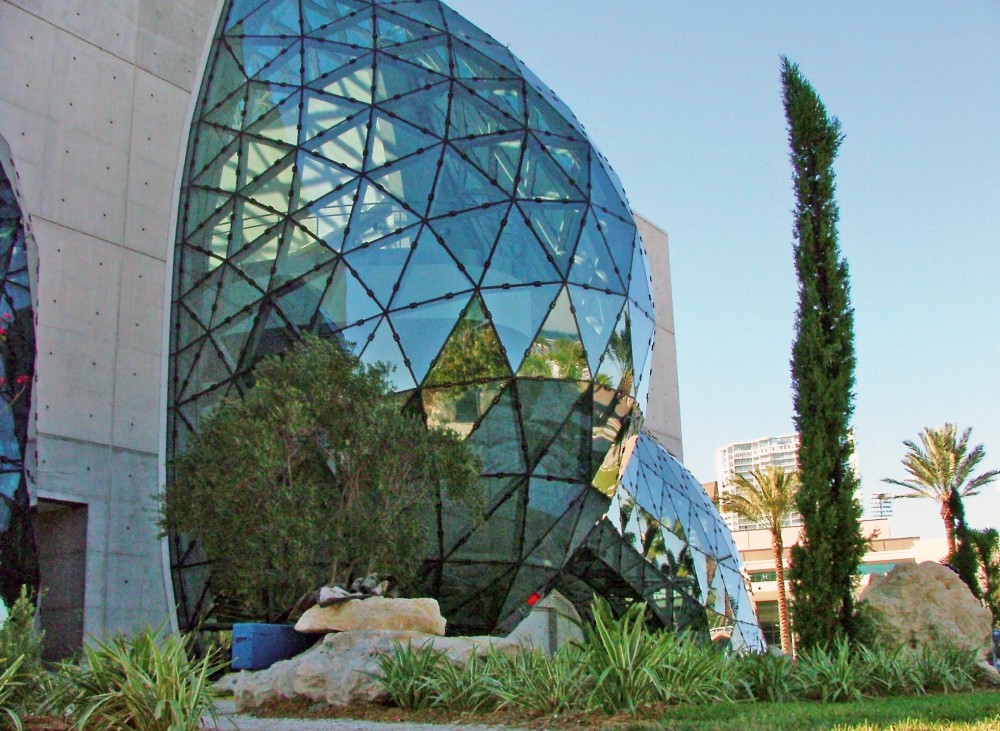
Case studies
Here are a few examples of structures that have extended their longevity and reduced their maintenance costs by specifying a duplex system.
Center for Great Apes
With a winding maze of chutes and walkways woven throughout the treetops, the Center for Great Apes (Wauchula, Florida) is a charitable organization created to provide sanctuary for chimpanzees and orangutans that have retired from the entertainment industry, completed research, or formerly served as pets.
After working in Borneo observing orangutans, Patti Ragan developed a passion for apes, and wanted to help provide long-term care for the animals. She created the facility in 2010 to offer the animals with a habitat as close to natural as possible. The clinic, night house, and all habitats are connected by a system of chutes and walkways elevated 3 to 4.5 m (10 to 15 ft) above the ground to give the animals the feeling of traveling through the trees.
The humid coastal environment, coupled with abuse from apes scratching and chewing, provides extreme challenges for corrosion protection. A duplex system of paint over hot-dip galvanized steel was the ideal solution for the structure as it would blend with the natural environment, without sacrificing long-lasting, maintenance-free durability. Now home to more than 40 residents, the Center for Great Apes will stand strong and achieve Ragan’s dream of an efficient, safe, and happy home for these retired animals.
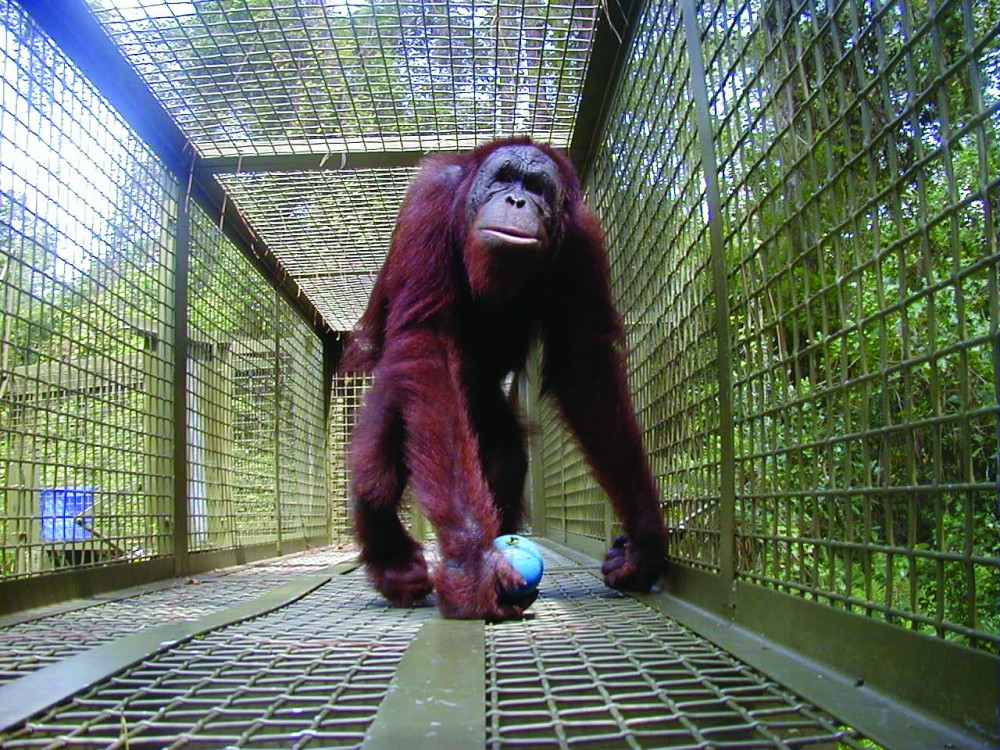
Woodwards Building
Reaching high into the Vancouver, B.C., skyline, the windowed walls of the Woodwards Building—or ‘W Tower’—are laced with columns of intricately etched decorative panels depicting tangled branches. These panels take advantage of the increased corrosion protection of a duplex system.
The tower contains more than 760 housing units, as well as the David Suzuki Foundation and Simon Fraser University downtown campus. With the protection of the duplex system, ivy-filled planter boxes on every third floor of the building will be free to grow and mimic the floral patterns on the screens themselves, unperturbed by touch-up crews and high-rise maintenance equipment—the goal is consistent, corrosion-free beauty for years to come.
Thurston Avenue Bridge
Set above a dramatic gorge in the midst of a copse of trees, the Thurston Avenue Bridge is located on the campus of Ivy League school, Cornell University in Ithaca, New York. The renowned institution, visited by scholars around the world, is highly visible to the public, and is passed over by up to 8500 vehicles, 950 pedestrians, and 60 bicycles per day.
The city wanted the bridge’s railings and metal structure to complement the light-emitting diode (LED)-illuminated railings, as well as blend with the other structural steel used in the bridge. A duplex system of powder coating over hot-dip galvanized steel was implemented to battle the corrosive effects of winter weather and road salts in this upstate New York location.
Hot-dip galvanized steel, which provides decades of maintenance-free longevity on its own, often outlasts the design life of the project for which it is specified. However, the combined protection of galvanized steel with powder coating means this bridge will be in service for generations.
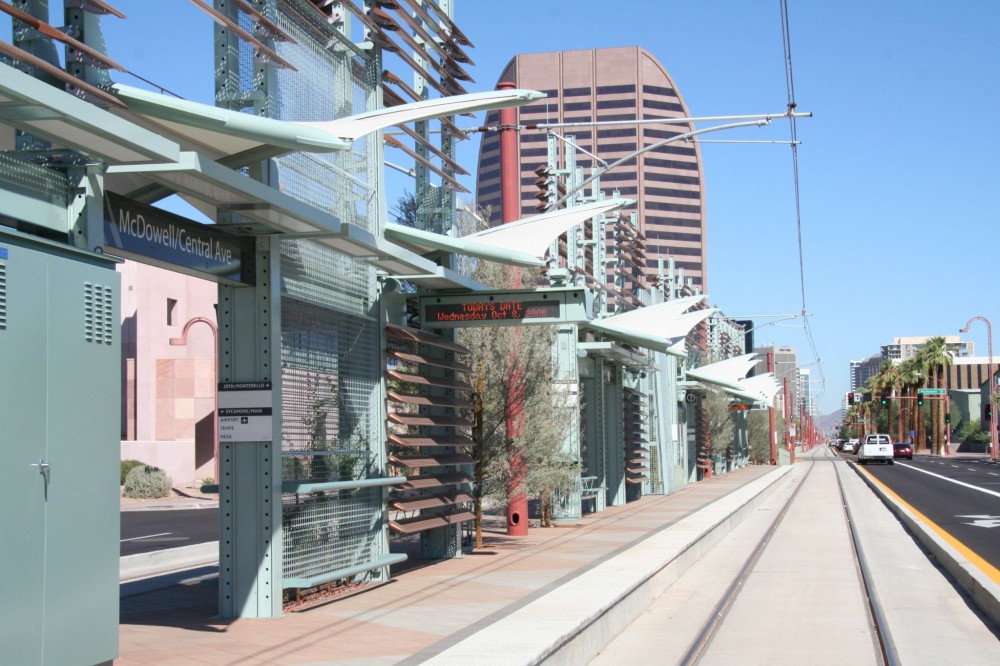
Conclusion
Duplex systems have been used for more than 40 years, but their specification is increasing in North America and worldwide because of the design freedom provided. In the past, some specifiers opted to sacrifice corrosion protection to achieve a particular aesthetic. However, by employing a duplex coating, specifiers can create projects with stunning, bold colors and superior corrosion protection.
Successful duplex systems begin at the drawing board, and require communication with the galvanizer upfront. The AGA has a number of additional resources (publications, technical articles, etc.) on painting or powder coating hot-dip galvanized steel including the instructional DVD Guide to Preparing Hot-Dip Galvanized Steel for Paint. SSPC has worked with AGA to develop recommendations and guidance on paint selection and application for duplex systems.
Notes
1 ‘Cathodic protection’ means the zinc coating sacrificially corrodes to protect the underlying steel. This means even if the zinc coating is damaged, no corrosion begins until all the surrounding zinc is consumed. (back to top)
2 Hot-dip galvanized steel typically lasts 70 years or more before maintenance—a half-century is an ultra-conservative figure used for ease. Paint coating can last for various years before maintenance is required, but a decade is a good average. (back to top)
3 Different paint formulations perform differently in different conditions. Some, like certain epoxies, degrade in UV light, while others are more resistant to chemicals. (back to top)
Melissa Lindsley is the marketing director for the American Galvanizers Association (AGA), and has been with the organization since 2005. She develops AGA’s marketing initiatives and is recognized as a leading voice for the galvanizing industry. Lindsley educates architects, engineers, fabricators, owners, and other specifiers about the technical aspects and benefits of hot-dip galvanizing. She can be contacted via e-mail at mlindsley@galvanizeit.org.
Hello, I am seeking permission to use the photo of the Chinatown Park project in Boston. I would credit Duplex (or other- please specify) below the photo. The photograph would be used in Portland, Oregon’s Historic Design Guidelines for New Chinatown/Japantown Historic District-
Kindly reply as soon as possible (this week, hopefully).
Thank you for your consideration,
Kristen Minor, Peter Meijer Architect (project manager)