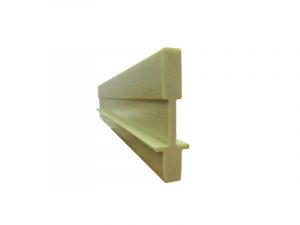
According to the Fenestration & Glazing Industry Alliance (FGIA),1 curtain wall sightlines are typically 57.15- to 76.3-mm (2.25- to 3-in.) wide, with a system depth of approximately 152.4 mm (6 in.) to 254 mm (10 in.). Regardless of which construction type or dimensions are selected for the curtain wall, FRP manufacturers can recommend how to best integrate these components into new or existing curtain wall systems to expedite the production process for the fabricator and the installation process for glazing contractors.
The industry as a whole is now realizing advanced FRP is available as an option for curtain wall design too. Therefore, many curtain wall systems used today are similar to those designed back in the 80s and 90s. Since FRP products only add about 20 percent more to manufacturing costs, the price should not be an issue. Often, it is through industry conferences such as The Buiding Envelope Conference and GlassBuild America that designers are seeing these materials firsthand.
An example of FRP technology in use was in the upgrade an old, drafty curtain wall at a Porsche/Maserati dealership in Cincinnati, Ohio. Owners needed a new curtain wall that would parallel the performance of the brands’ industry leading supercars, considering the previous wall was letting in air leaks and would fog up when it was cold outside. FRP pressure plates were incorporated into thermally broken curtain wall hardware components designed to meet or exceed the industry’s most stringent energy codes. The FRP pressure plates allowed the project to achieve a condensation resistance factor of 80 in the frame and 70 in the glass. In addition to thermal performance, the FRP pressure plates provide structural strength for the entire curtain wall system, outperforming polyamide alternatives in both compressive and flexural strength and exhibiting no creep under sustained loads. The final result delivered a comfortable interior climate for staff and customers. The new curtain wall with FRP technology also reduces the facility’s energy usage for a cleaner, greener footprint.
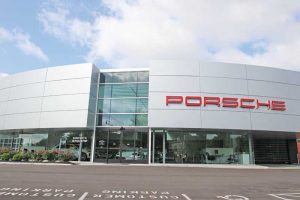
FRP thermal pressure plates were also used for Vaisala’s North American Headquarters. The custom designed pressure plates were again added to a thermally broken curtain wall system and proved to be a keystone in the development of one of Colorado’s most sustainable buildings. The headquarters was built in Scandinavian style with an exceptional energy-efficient profile. FRP thermal pressure plates were combined with warm edge spacers to achieve a system U-factor of 0.32 with excellent condensation resistance (up to 80 CRF), as well as exceptional air, water, structural, and acoustic performance all confirmed by independent laboratory testing.
Conclusion
Curtain wall usage is accelerating in commercial construction; therefore, it is critical for all construction stakeholders in charge of the design, fabrication, and specification of curtain walls and their components to seek the industry’s highest-performing solutions.
Identifying manufacturers that can create an array of applicable curtain wall components that address thermal bridging, condensation, structural integrity, and long-term durability will be critical for the many developments seeking LEED certification or those striving to achieve near- and long-term greenhouse gas (GHG) emission targets.
Notes
1 Refer to “Curtain Walls.” FGIA, fgiaonline.org/pages/curtain-walls.
2 Visit the National Fenestration Rating Council (NFRC) 101-2020.
I have been suggesting the use of FRP materials in curtain wall construction as a method to reduce the heat loss, and improve thermal performance. This article hopefully will make other manufacturers aware and implementation of FRP use.