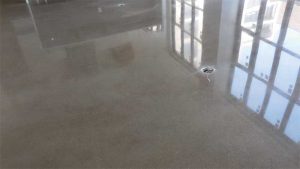
Photos courtesy Simpson Gumpertz & Heger, Inc.
A bonded topping slab only requires joints where the substrate has them because the topping slab will move and respond to volume changes in the same manner as the substrate to which it is bonded. Further, joints will be ineffective in controlling cracking because the topping slab is bonded to the substrate. In fact, joints in bonded toppings can worsen cracking, debonding, and curling since they increase the amount of edges and corners where bond stresses are highest. The author’s bonded topping slab is on an elevated structural slab without joints, thus eliminating jointing. Sometimes, bonded topping slabs on elevated structural slabs have joints at the negative moment regions to reflect any negative moment crack. Control joints can mitigate the randomness of crack propagation as a defined joint can be sealed or filled. The 75-mm thickness of the authors’ topping slab combined with architectural and contractor wishes for minimal control joints aided them in choosing a bonded topping slab over an unbonded one.
Reinforcement
Reinforcement will not prevent cracking; it will only control the width and spacing of cracks. Reinforcement needs to be coordinated with control joints, if used, to permit the latter to widen and provide shrinkage relief. Steel reinforcement in a 75-mm bonded slab will likely consist of #3 reinforcing bars or flat sheets of welded-wire-reinforcement (WWR). For jointless slabs, ACI 360R recommends a minimum reinforcing ratio of 0.5 percent—ACI 224R, Control of Cracking in Concrete Structures, recommends 0.6 percent—both ratios are greater than the minimum ratio (0.18 percent) for shrinkage and temperature that is required by ACI 318, Building Code Requirements for Structural Concrete and Commentary. Reinforcement designed to control cracking is most effective when placed in the upper third of the slab, as shrinkage cracking originates from the surface. In a 75-mm design thickness, the specified 50-mm cover over the radiant tubing would locate the reinforcement above the tubing.
For the authors’ topping slab, the contractor preferred to place the hydronic heating tubing on top and tie it to the reinforcement for ease of installation and damage protection during construction. In this method, the reinforcement must be placed close to the bottom of the topping and there should be limited cover between the tubing and the final surface. The lower placement of the reinforcement will result in greater cracking and/or wider cracks.
For a bonded topping on an elevated structural slab, supplemental reinforcement added to the base structural slab in regions of negative moment will help control the width of any cracks in the structural slab that reflect through the topping slab. Additional reinforcement in the topping may be insufficient to restrain negative moment cracking. With proper planning and coordination during design and construction, modifications to the size and spacing of the reinforcement within the base structural slab can help mitigate cracking of elevated concrete structural slabs. ACI 224R provides recommendations for the structural engineer to use to control cracking in two-way elevated slabs.
Substrate preparation
For an unbonded topping slab, surface preparation consists of a bond breaker installed between the substrate and the topping slab. Bond breakers are typically one or more layers of plastic sheet to allow free movement of the topping slab (note, although other options may exist, such as roofing felt, the authors have not seen a regular use of them). The available topping thickness of 75 mm cannot accommodate a layer of insulation between the topping and the base slab.
For a bonded topping slab, preparation of the base slab top surface is critical for successful topping slab construction. The topping requires a rough, open surface to provide strength to transfer stresses between the base and topping slabs. The rough surface can be created during base slab installation by brooming or raking the top surface, or by mechanical and abrasive methods such as sandblasting or shotblasting, just prior to topping installation. Bond was provided for the authors’ topping slab by raking the top surface of the substrate after placement. Bond tests were completed to ensure the raking method offered adequate bond.
In addition to properly roughening the substrate prior to installing a bonded topping slab, the substrate needs to be prepared to receive the topping concrete. Ideally, the substrate will be clean and saturated, surface-dry such that no water will be absorbed from the topping concrete nor any excess water added to the topping concrete. Additionally, if the placement occurs during hot or cold extremes, as happened for the authors’ project during a cold Chicago winter, pre-heating of the substrate is recommended to avoid thermal shock to the structural slab and topping concrete.
Concrete mix design
ACI 310R suggests a compressive strength of 27,579 kPa (4000 psi) or greater is suitable for polishing with a water-to-cementitious materials (w/cm) ratio between 0.38 and 0.45 for workable and durable concrete. Air entrainment is unrequired if the slab will not be exposed to freezing and thawing cycles once the building is complete. Further, air entrainment should not be used in a slab to receive a hard trowel finish due to the risk of blistering.