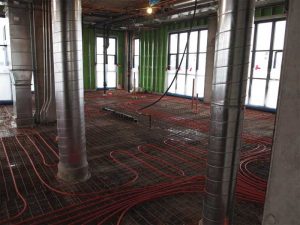
Lower w/cm ratios result in more stable color between batches, increased durability, and reduced shrinkage. Lower w/cm ratios and non-air-entrained concrete typically result in higher compressive strengths. The mix design should contain the largest possible portion of aggregates to minimize the cement paste content and reduce shrinkage. Supplementary cementitious materials can improve hardened concrete properties but may affect color and plastic properties. Most supplementary cementitious materials also slow the strength development of concrete compared to cement alone. Slower strength development can result in increased cracking if they result in shrinkage stresses developing faster than concrete tensile strength.
The clear distance between the substrate and the embedded hydronic tubing or reinforcement restricts the maximum aggregate size permitted in the concrete. The maximum aggregate should be limited to 3/4 of this dimension.
For a given concrete mixture, the total ultimate concrete shrinkage strain is the same for all types of topping slab thicknesses, but the duration to achieve that ultimate shrinkage is longer for thicker slabs. The use of a shrinkage-reducing admixture in the concrete mix can reduce the shrinkage strains that could develop in the topping slab. Instrumented tests of mixes with shrinkage-reducing admixtures find they can significantly reduce the early age shrinkage by up to 50 percent and the long-term shrinkage by 25 to 30 percent. Reduced shrinkage significantly lowers bond stress demands on a bonded topping interface. The author recommends that a concrete mixture with less than 0.04 percent shrinkage when tested according to ASTM C157, Standard Test Method for Length Change of Hardened Hydraulic-cement Mortar and Concrete, modified by a seven-day wet-curing period.
Slab configuration
Shrinkage and other internal tensile stresses vary with the plan configuration of the topping, with irregular shapes creating several areas of stress concentrations. There is also a higher risk of cracking at re-entrant corners, long narrow areas, and localized stress concentrations developing from penetrations and embedded items (such as electrical boxes). Minimizing these items will help reduce the risk of cracking associated with stress concentrations. Additional localized reinforcement could also minimize the width of any cracks that may form.
For unbonded concrete topping slabs, successful performance depends on the slab’s ability to freely move and respond to the development of internal tensile stresses. Control joint layout and additional reinforcement are the primary methods to minimize restraint cracking for these slabs.
For bonded topping slabs, additional protection against debonding may be warranted in these irregular plan areas causing restraint. Supplemental dowels or pins into the substrate at edges and corners can be used to provide a mechanical supplement to bond strength (especially at early ages) to prevent debonding and curling.
Finishing
Depending on the desired surface finish, the required floor flatness (FF) may be a critical consideration for designers to specify and contractors to consider. FF is measured according to ASTM E1155, Standard Test Method for Determining FF Floor Flatness and FL Floor Levelness Numbers, and higher requirements demand greater care and construction controls from the contractor. ACI 310R recommends an overall minimum FF of 50 with a local minimum of 45 to minimize aggregate exposure in polished concrete. ACI 310R also notes an overall FF less than 40 will likely result in localized aggregate exposure at high points. In the authors’ project, through-topping penetrations, deflections of the supporting elevated structural slab, and obstructions from interior walls and columns prevented use of sophisticated tools such as laser screeds to provide higher flatness. The project achieved a typical FF of approximately 35, resulting in localized uneven surface finish and aggregate exposure.
Curing
Curing the freshly placed concrete is critical to minimize the cracking potential due to shrinkage of both bonded and unbonded topping slabs. Proper curing will minimize early age shrinkage, delay drying shrinkage, and promote development of bond and tensile strength of concrete. Portland Cement Association’s (PCA’s) Design and Control of Concrete Mixtures notes “concrete wet cured for seven days has less shrinkage because of drying and autogenous effects than concrete that had no water curing” and emphasizes the importance of early wet curing. The authors prefer to specify a wet cure of topping slabs for a minimum of seven days. This wet cure must be completely saturated and drying or evaporation from the exposed surface of the topping concrete should be prevented. The contractor for the authors’ project preferred to use wet blankets to avoid the leakage of excessive water through penetrations onto curing topping slabs below. A membrane forming curing compound for the topping slab was not considered to prevent any undesirable issues with future polishing or applications of densifiers or penetrating sealers.