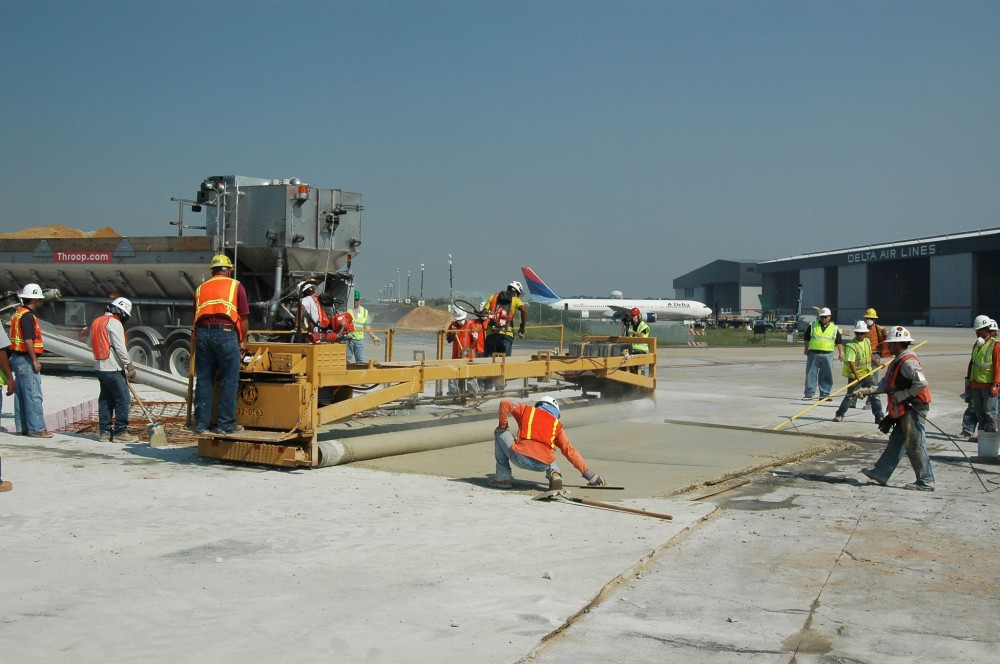
by Eric Pascal Bescher, PhD, and Nick de Ocampo, LEED AP
Although ‘sustainability’ is a popular term, it remains an ill-defined and nebulous concept in the construction industry. This is especially the case with concrete, where it can be difficult to understand cost and environmental benefits.
There is no straightforward, simple definition of what sustainability means to the construction industry. Further, there are few tools or even metrics available to help decision-makers specify one construction material over another in relation to sustainability.
The sustainability of concrete, the most widely used material in the world, is still a difficult concept to quantify. However, the recently developed Product Category Rules (PCRs) for concrete are a step in the right direction.
This article focuses on the sustainability of materials used in civil infrastructure such as highways and bridges, but the concepts explored are also frequently applicable to materials used for building repair.
Defining sustainability
According to the U.S. Environmental Protection Agency (EPA), sustainability is based on the simple principle that everything needed for survival and well-being depends, either directly or indirectly, on the natural environment. Sustainability efforts ensure resources needed to protect human health and the environment remain available.
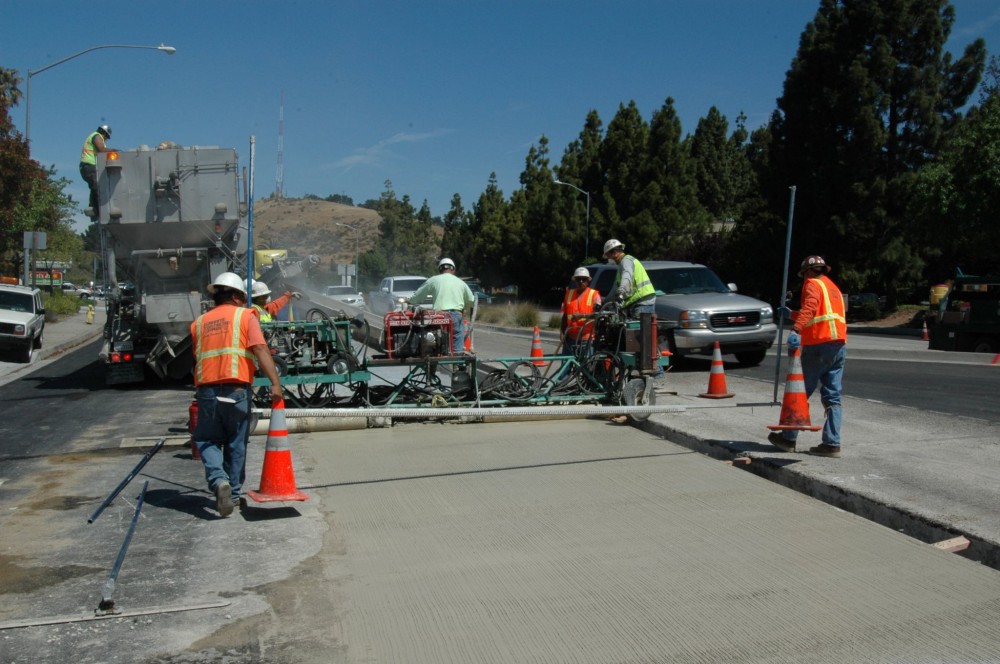
The sustainability of construction material is affected by the amount of non-renewable materials entering into its manufacturing and its lifespan before it has to be replaced and manufactured again. These non-renewable materials include sand, rock, and limestone for cement manufacturing.
Most sustainability or green voluntary certification programs—including Leadership in Energy and Environmental Design (LEED) and other multi-attribute certification programs developed by industry groups—have focused on energy, material and water conservation, indoor environmental quality, and site selection and development.
While these are all important aspects of sustainable building design and construction, lifecycle does not appear to be an integral part of this definition.
The Cement Sustainability Initiative—a project of the World Business Council for a Sustainable Development (WBCSD)—is a complex effort by 24 major cement-producers to look at the factors affecting concrete sustainability. It is still in its infancy and is attempting to deal with the many facts of concrete manufacturing. However, it cannot yet circumvent the fact portland cement technology and its carbon footprint has changed little since Joseph Aspdin obtained the patent in 1824.
A century-old technology
The portland cement industry in the 21st century is facing one fundamental fact of materials science: the technology is significantly dated. Although the industry has made great strides in the efficiency of limestone burning, the material’s carbon footprint has not changed significantly, and is not likely to any time soon. The industry is locked into a technology forcing it to emit large amounts of carbon dioxide (CO2). In order to make one ton of cement, approximately one ton of CO2 must be released into the atmosphere.
Given the global industry produced nearly 4 billion tons in 2012, portland cement production accounts for about five percent of total greenhouse gas (GHG) emissions worldwide.
Sustainability efforts have been generally limited to reducing the cement content in concrete or increasing the amount of filler, such as limestone, slag, or fly ash. While fly ash, blast furnace slag, and other pozzolans provide cementitious properties, such fixes are superficial and can only reduce the carbon footprint by a fraction; they do not address the basic, core issue of a 200-year-old chemistry As a result, it can be difficult to consider traditional portland cement concrete as a sustainable building material.
A greener solution
It is possible to produce ‘green’ cement that would tap less into natural resources?
Such ‘greener’ concrete is available with calcium sulfoaluminate (CSA) cement. This rapid-setting cement requires burning mixtures of limestone, bauxite, and gypsum at lower temperatures than portland cement—approximately 1482 C (2700 F) for portland cement versus 1232 C (2250 F) for CSA cement.
This lower burning temperature reduces the amount of energy and carbon dioxide emissions associated with portland cement production. CSA cement also requires less limestone, which is the primary source of carbon dioxide released during the chemical sintering process. CSA clinker is also easier to grind, reducing the energy needed during the milling process. A particularly interesting type of CSA cement is the CSA-belite (C2S) cement that provides some of the advantages of portland cement while lowering its carbon footprint.
CSA cement can play a significant role in improving the sustainability of construction materials by simply reducing the quantity of non-renewable resources used during manufacturing. The use of resources is just one part of the equation—durability, or lifecycle, is the second.
CSA-belite cements have been available for a few decades. They generally fall under ASTM C1600, Standard Specification for Rapid-hardening Hydraulic Cement. They are extensively used in runway or highway repair, (For example, the Seattle-Tacoma Airport repair discussed later in this article.) To date, more than 330 lane-miles of highway have been replaced in California using this material.
Quantifying sustainability
When selecting a building material—asphalt, portland concrete, or CSA concrete—sustainability should be easily quantifiable. One method for assessing the sustainability of a construction material could be to divide its lifecycle by the amount of non-renewable resources required in its manufacturing process.
Using this method, the Sustainability Index— developed by this article’s author Eric Pascal Bescher, PhD—would be defined as:
Sustainability Index (S) = Lifecycle
Resources
In this equation, “lifecycle” refers to the durability of concrete in years. It is linked to fatigue life and other material properties such as shrinkage, cracking, and porosity.
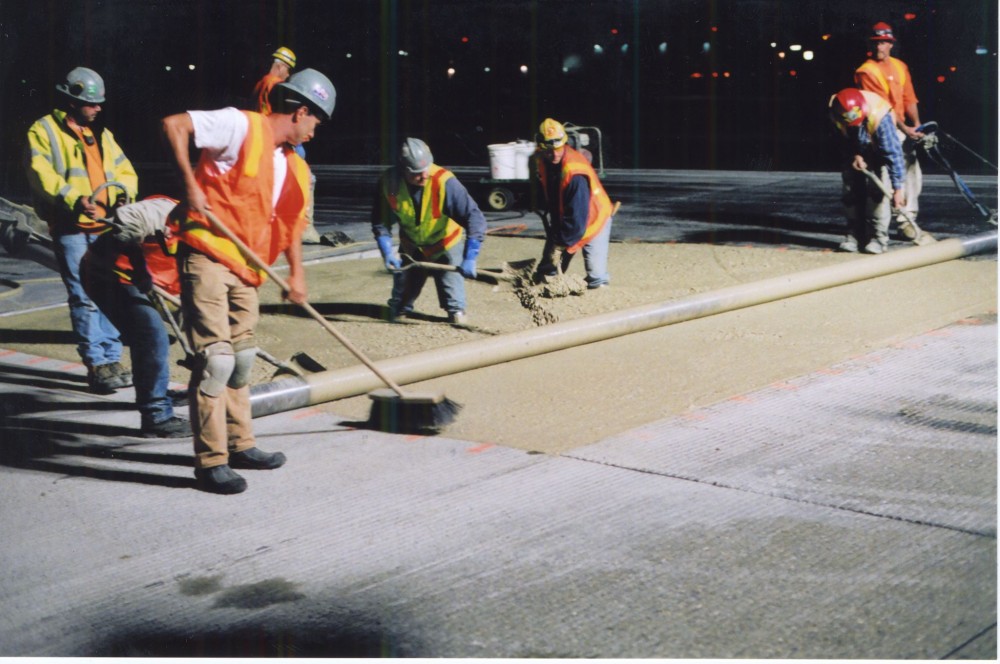
“Resources” refers to the quantity of non-renewable resources used in concrete manufacturing (such as, but not limited to, carbon footprint). Finally, the Sustainability Index, as defined above, can have the unit of [m3*years/ton-CO2].
In this equation, sustainability is tied not just to resources used, but also to lifecycle. If the lifecycle of one cubic meter of concrete were infinite, it would be sustainable. However, if the entirety of our planet’s resources were required to manufacture the same amount of concrete, it would not be sustainable. The Sustainability Index helps to quantify the sustainability of producing and using one cubic meter of concrete in simple, measureable terms.
Further, LCA and EPD calculations, as defined by concrete PCRs, can be used as the numerator and the denominator, respectively, in the Sustainability Index equation.
The lifecycle of concrete
This straightforward index can help rate the sustainability of various materials and mix designs and helps decision-makers choose materials consistent with stated sustainability goals. It brings lifecycle into the equation, and a greater lifecycle decreases the burden on resources.
A 100-year-old pavement would have five times the Sustainability Index of a 20-year pavement, all other parameters being equal. At equal lifecycle, a mix design with half the carbon footprint would have twice the sustainability. This simple concept ties economic decisions to materials properties.
The concept also highlights the sustainability of concrete is, above all, a materials property. For example, lower shrinkage and lower porosity increase lifecycle. Doubling the lifecycle while halving the carbon footprint, quadruples the Sustainability Index. Using this approach, the sustainability of concrete is not such a nebulous concept—its basic definition becomes “the lifecycle of the material per unit of non-renewable resources.”
With this definition of sustainability for the concrete industry, decision-makers now have a tool allowing them to select between materials of different lifecycles made with different resources. Choosing a sustainable building material should be a matter of figures and numbers. The table in Figure 1 provides examples of the Sustainability Index for various mixes and materials in 0.7 m3 (1 cy) of concrete. Different mixes and materials have different sustainability indices. For example, the type of cement, cement content, or the addition of fly ash to a mix can affect its sustainability.
Concrete, water, porosity, and structure
Concrete is a highly porous material, with the amount of water used in the mix controlling its porosity. A highly porous concrete will have lower strength and shorter lifecycle. Also, as concrete shrinks as it ages, it causes cracks to develop. Any factor reducing concrete shrinkage decreases its tendency to crack. This, in turn, increases its lifecycle and therefore sustainability.
Generally, portland-based concrete shrinks because more water is needed to make a workable mixture than required for chemical hydration. Most of the shrinkage of portland cement concrete, and its lifecycle, are directly connected to the amount of water needed to make the mixture. Adding more water than needed to hydrate is one reason why the goal of 100-year pavement is still elusive.
CSA concrete permanently retains the mixing water in its crystalline structure, which makes it less prone to shrinkage or cracking. CSA concrete is less porous, stronger, and has lower shrinkage than portland cement concrete, which increases its lifecycle. CSA concrete’s lifecycle has been tested to be as long as 80-years versus 40-years for portland cement. Using the Sustainability Index, civil engineers can include lifecycle as part of the evaluation of the sustainability of a mix design.
Lifecycle implications
A long lifecycle is a significant advantage in many applications, such as highway rehabilitation. The United States is facing serious problems related to its deteriorating infrastructure as engineers and state Departments of Transportation (DOTs) are confronted with aging and decaying highways causing safety and transportation issues. When concrete ages and cracks, it must be replaced at a significant cost. Therefore, increasing the lifecycle of concrete is important to sustainability efforts.
As an example, many California freeways built in the 1950s and 1960s are now at the end of their lifecycle or past the point when they should have been rebuilt. Shutting down even a portion of a freeway for repairs has a tremendous impact on human activity and the economy. Many DOTs would be interested in a concrete that could last 80-to- 100-years, rather than the typical 20-to-30-year lifecycle of portland cement.
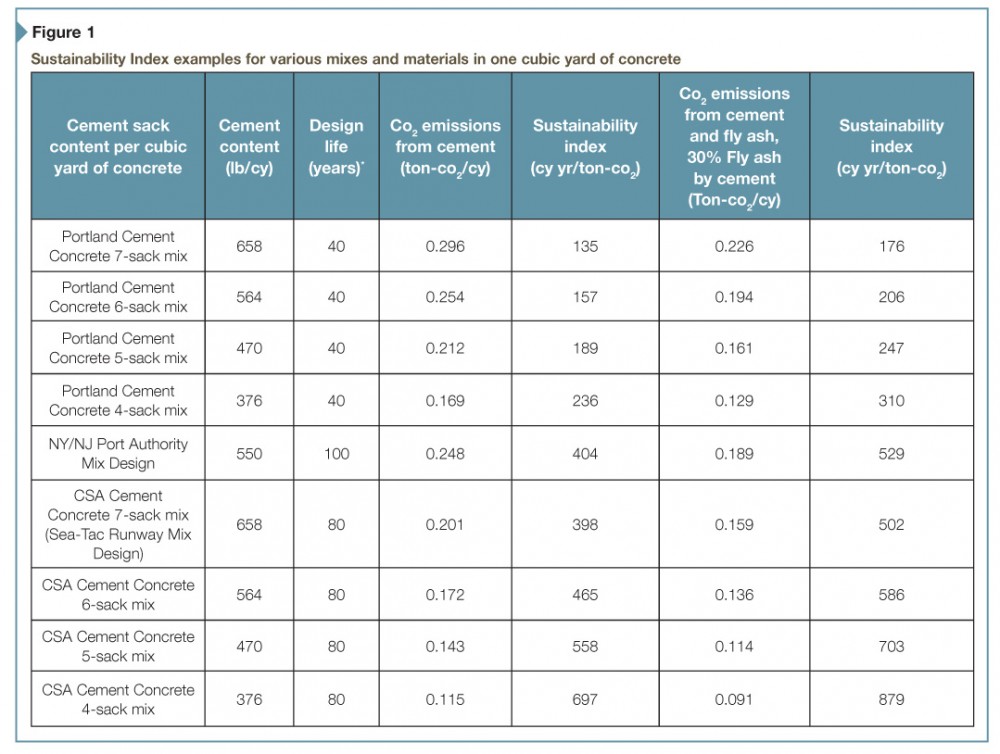
CSA concrete and LEED
CSA cement can play an important role in improving the sustainability of construction materials, mostly because its chemistry and materials science differ from the well-established standards of portland cement. It can play a significant role in the sustainability of concrete technology from the perspective of raw materials use, energy demand, carbon footprint, and pavement longevity.
A combination of low calcium content and low burning temperatures allows CSA cement to yield concrete with lower carbon footprints. When used as a shrinkage-compensating additive to portland cement, CSA can also improve sustainability through a decrease or total elimination of shrinkage, resulting in an increase in longevity.
Users of CSA cement can help a project earn points toward Leadership in Energy and Environmental Design (LEED) certification. Points can be obtained for energy and water conservation, reducing harmful greenhouse gas emissions, and reducing waste sent to landfills. For example, CSA cement can help a project earn up to 13 LEED points over a range of credits including recycled materials, heat island effect, and low-emitting materials.
CSA cement meets guidelines for LEED credits through its use of byproducts. Calcium sulfoaluminate requires aluminum oxide and calcium sulfates. These compounds can be introduced using byproducts of aluminum recycling or synthetic gypsum as raw materials. These byproducts eliminate the need for bauxite and gypsum mining.
The improved sustainability of CSA-based concrete is due to a combination of factors including:
- lower emission of greenhouse gases;
- decreased emissions of smog-producing nitrogen oxides;
- use of recycled raw feedstock materials; and
- longer lifecycle through higher strength, lower shrinkage, and lower porosity.
Rapid-setting and sustainability
There are several additional benefits that should be taken into account when considering CSA cement for a project. While portland cement can set in about three hours, it can take several days for it to reach structural strength. CSA cement achieves structural strength in three hours.
As a result, CSA concrete is used in time-sensitive pavement rehabilitation projects such as the Seattle-Tacoma (Sea-Tac) airport.
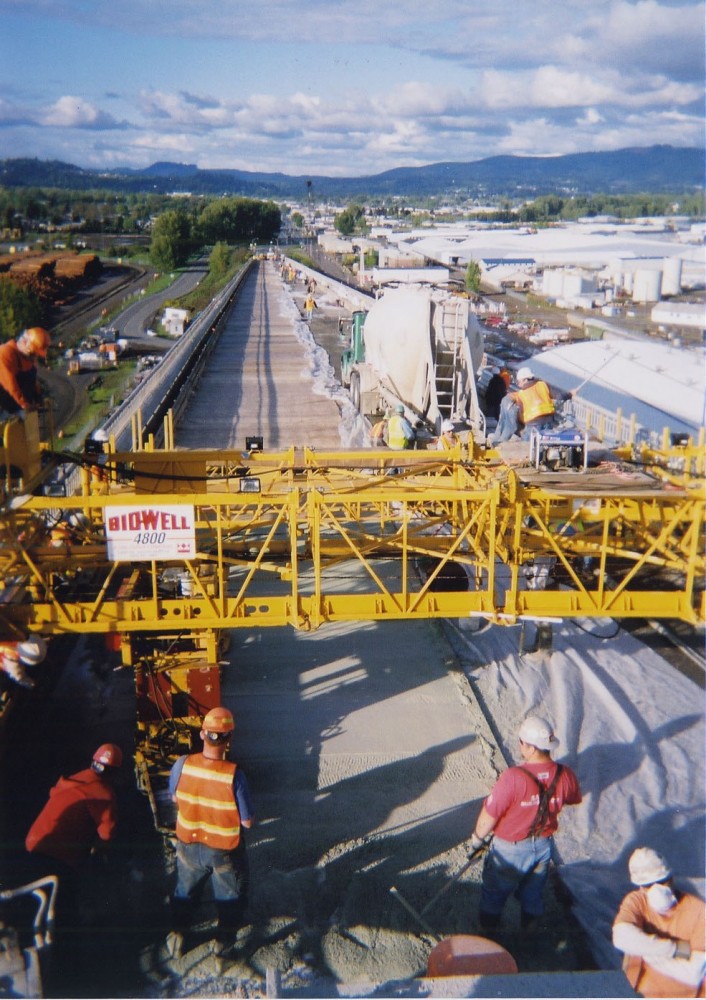
The Sea-Tac runway in Washington was shut down at midnight, old concrete removed, and fresh CSA concrete poured. By 6:00 a.m., planes were able to land. Another example is the use of CSA cement to rehabilitate aged concrete on freeways in California, where more than 300 lane-miles of pavement have thus far been replaced with an average replacement rate of 35 panels (i.e. 133.8 m3 [175 cy]) per eight-hour closure, and a maximum replacement of 203 panels (i.e. 776 m3 [1015 cy]) in 10 hours.1
There are substantial sustainability benefits to the rapid-setting characteristics of CSA concrete. For example, shorter closing times mean less fuel burned in traffic and lower economic impact on the travelling public. Additionally, it can be used in post-tensioned concrete buildings, or precast concrete work, where high, early strength means sooner post-tensioning and faster construction times.
Cost considerations
Cost is a significant factor in the selection of sustainable building materials. On a pound-for-pound basis, CSA cement could be approximately three times more costly than portland cement, or 1.2 times more expensive than portland cement accelerated with organic additives. This difference is a challenge for engineers and specifiers responsible for selecting a repair material. Does it make sense to select a cheaper, less durable material when the longer-lasting alternative is more expensive?
As a matter of accountability to the public who generally pays for these repairs, the overall benefits of a longer-lasting pavement outweigh the short-term impact on a budget. A less-expensive material that will need to be replaced in 20 years simply shifts the burden to future generations. Pavement management policies should make lifecycle its first priority over purchase price.
The Sustainability Index can be an important tool. It helps engineers and specifiers make decisions on cost and lifecycle considerations and environmental impact without being overly complex. A common misconception is cement chemistries and materials are all the same. This is not true, as evidenced by the differences between portland cement and CSA cement in terms of properties, cost, and sustainability. Understanding these differences and using the Sustainability Index is crucial to making the best decision for the project.
Conclusion
The industry must educate itself on the advantages of the technology for calcium sulfoaluminate cement to become widely used. There is always inertia in specifying a material that deviates from standards, especially if those standards were established in the 19th century.
When civil engineers have a choice of materials, they need a tool to differentiate between them. The Sustainability Index is a valuable tool to help decision-makers make informed, sustainable materials choices in tight fiscal times.
The construction industry should look to CSA cement with a fresh eye because of its impact on sustainable development and the improvement of infrastructure.
Notes
1 The Sea-Tac runway mix design is a seven-sack CSA concrete tested at the University of Oklahoma to have a lifecycle of over 80 years. (back to top)
Eric Pascal Bescher, PhD, has been adjunct professor in the Department of Materials Science at University of California, Los Angeles (UCLA) since 1998. He also joined CTS Cement as director of research in 1998, and is now vice-president for cement technology. Bescher holds a bachelor’s degree in materials physical chemistry from the University of Rennes, France, as well as a master’s and PhD in materials science and engineering from UCLA. He is the author of more than 33 scientific articles in the field of materials science and the holder of several patents. Bescher can be contacted via e-mail at bescher@ucla.edu.
Nick de Ocampo, LEED AP, joined CTS Cement in 2008 as a product development engineer to help promote the sustainable properties of calcium sulfoaluminate (CSA) cements. He holds a bachelor’s degree in materials science and engineering from UCLA. de Ocampo has developed LEED product evaluations for the company’s rapid-setting product line. He can be reached at ndeocampo@ctscement.com.