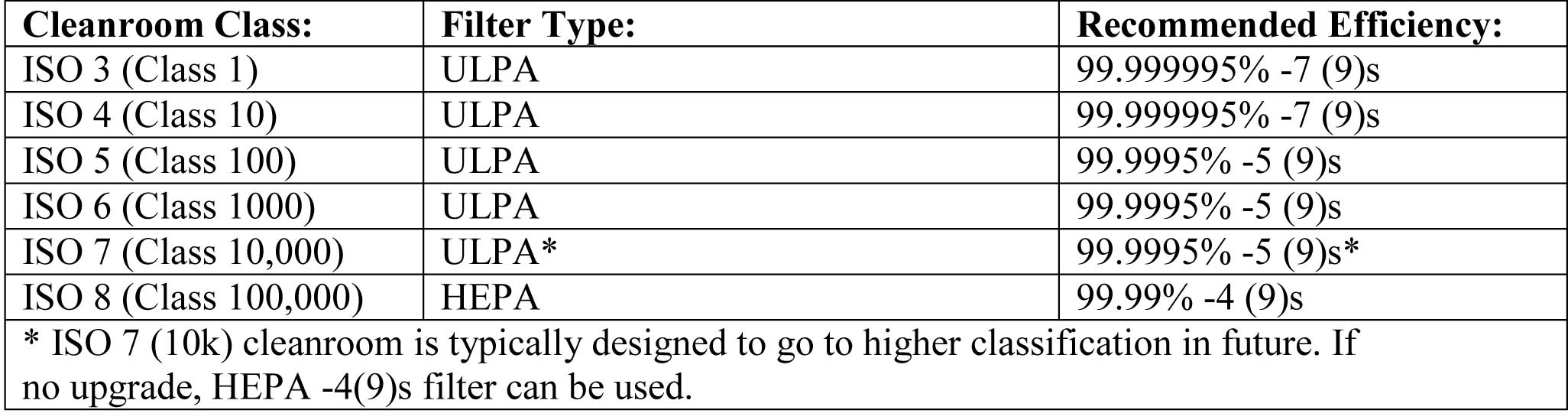
Since the gel grid system installation is tricky, more owners prefer to use the easy-to-install gasketed ceiling with filter fan units sitting directly atop the gasket. Since filter fan units are located on the cleanroom ceiling grid in the plenum space, these systems do not take up facility floor space and offer maintenance access from below or above. With noise levels as low as 55 dB(A), these units offer quiet operation as well.
Units using the latest DC motor models have proven to be highly reliable, and they also have very low energy usage. Filter fan units have a negative-pressure plenum that forces any leaks up into the plenum instead of the cleanroom; they typically use a gasketed ceiling grid consisting of a closed-cell foam gasket located around the perimeter and atop the filter opening. The units are very cost-competitive when coverage is less than 50 percent, but typically a high quantity of units is required for greater coverage or for large cleanrooms.
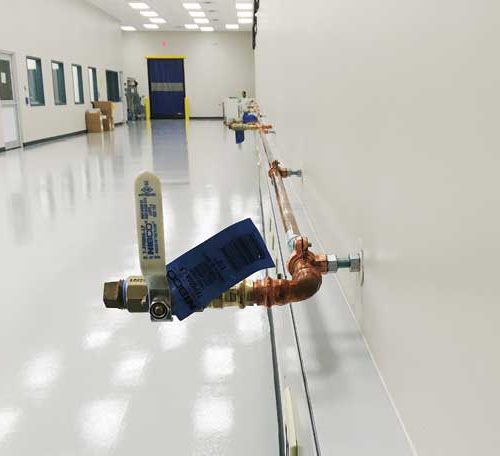
Airflow within the clean space is another consideration for specifiying the recirculation system. Based on the needs and use of the room, the flow must be enough to allow for the prescribed recirculation, but not so fast it stirs up particles. Additionally, designers should consider the impact of air flowing over people in the room and depositing particles on the work product when determining the locations of the supply and returns within the space. Overall, the goal is to provide a gentle blanket of air in the cleanroom that provides comfort and cleanliness without causing disruption that adds particulate to the air.
The cleanliness of the supply air delivered to the cleanroom is primarily determined by the ceiling filter coverage, as well as the efficiency of the filters. For the initial intake of outside air, a pre-filter is used to remove larger particles. Within the cleanroom, ULPA and high-efficiency particulate air (HEPA) filters remove the smaller particles. HEPA filters are 99.97 to 99.995 percent efficient at 0.3 µm MPPS, while ULPA filters are rated 99.9995 to 99.9999995 percent efficient at 0.12 µm MPPS. The pre-filter, which should be changed according to contaminant loading, also serves to extend the life of the more expensive HEPA/ULPA filters. For each cleanroom classification, there is a related filter efficiency recommendation that should be followed (Figure 3).
Building automation provides control
The building automation system (BAS) is critical to the proper functioning of the cleanroom HVAC systems, so specifiers should possess a strong grasp of control systems in order to write the detailed sequences required for the cleanroom BAS. Today’s advanced direct digital control (DDC) systems greatly simplify the monitoring and control of cleanroom conditions—no longer does an employee have to walk around, manually checking gauges and documenting the room pressures. Rather, the MUA air-handlers are equipped with variable frequency drives controlled by the BAS, making precise regulation of air pressure automatic. The BAS monitors and stores data related to pressure, temperature, and humidity; it also activates alarms when conditions are beyond accepted tolerances.
The BAS not only controls conditions within the cleanroom, but reports on them as well—a critical step for the continued success of the cleanroom. Certification of the room and the products produced within it depend on meeting design and cleanroom classification criteria. The BAS provides detailed records documenting the conditions in the cleanroom consistently meet these standards—this way, the room or products do not lose certification.
Conclusion
Before designing and specifying systems for a cleanroom HVAC system, the engineer must first understand the classification of the room and what activities will be performed there, as these will influence the type of HVAC systems required. As these rooms have precise tolerances for everything from temperature and humidity to air pressure, precision is required in the design of the HVAC systems. Fortunately, the requirements laid out in the utility matrix, as well as the ISO classification, provide a road map for what the HVAC system must accomplish. This will guide the engineer toward successful design and specification.
Matt Strong, PE, LEED AP, is president of C1S Group, which is a full-service professional engineering and construction firm based in Dallas. Strong has more than 26 years of experience in the design and installation of mechanical and electrical systems. He can be reached via e–mail at matt.strong@c1sinc.com.