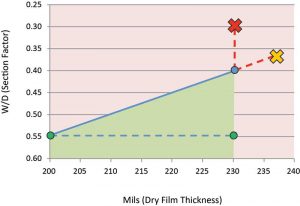
UL considers the following two scenarios acceptable in its revised fire-resistance rating guidance documents.
- Using the minimum listed coating DFT for a particular beam size (specific W/D) on a larger steel section (greater W/D) that has a greater heat sink than the listed steel section. (The heat sink would provide some fire resistance, allowing the minimum DFT to provide a similar fire-resistance rating.)
- Substituting a steel member for a heavier weight (greater W/D) section using the same specified coating thickness. (The heavier steel section could actually require less coating thickness for the same fire-resistance rating but using the same DFT will certainly provide the same or better protection.)
Conversely, UL lists the following scenarios as unacceptable because the applied coating may be too thick, creating the potential for delamination from the steel during a fire:
- using a coating DFT specified for a larger steel section to cover a smaller steel section with a lower W/D than is listed; and
- substituting a steel member for a lighter weight (lower W/D) section using the same specified coating thickness.
Figures 6 and 7 demonstrate these points for engineers and architects specifying the intumescent coating DFT for a given steel section W/D ratio. In both diagrams, one simply needs to stay within the green areas and stay out of the red sections. In this author’s experience, any point on or below the blue lines is fine.
In both figures, the blue lines represent the maximum allowed data points in ANSI/UL 263 and ASTM E119. The blue line in Figure 6 terminates at a W/D ratio of 0.40, the lightest steel listed in ANSI/UL 263. The required coating DFT is plotted on the X-axis in relation to the steel section’s W/D ratio on the Y-axis. For example, the blue dot shows a steel section with a W/D ratio of 0.40 requires a 6-mm (230-mils) DFT for a two-hour fire-resistance rating. The left-hand green dot shows a steel section with a 0.55 W/D ratio would require a minimum DFT of 5 mm (200 mils). However, the right-hand green dot reveals the 0.55 W/D ratio section could be coated up to a 6-mm DFT without worry. The DFT cannot exceed 5 mm for either of these steel sections because the data is not included in UL’s listing. Therefore, per UL guidelines, specifiers cannot extrapolate the data to a lower W/D ratio (red X) or to a higher DFT (orange X).
Enhancing Aesthetics and Protecting Against Corrosion |
Per building fire-resistance codes defined in the American National Standards Institute/Underwriters Laboratories (ANSI/UL) 263, Standard for Fire Tests of Building Construction and Materials, and ASTM E119, Standard Test Methods for Fire Tests of Building Construction and Materials, and enforced by local municipalities, state governments, building owners, and insurance companies, all structural steel members of a building must be coated with the appropriate intumescent coating thickness based on final specifications. Coatings can be applied either in the field or offsite in a controlled facility. After the coatings have cured, applicators will use an electronic gauge to determine the resulting DFT. If insufficient, they will apply additional coating material to reach the specified thickness.
Following the application of intumescent coatings on exposed structural steel, architects often choose to apply a topcoat for a more aesthetically pleasing or colored finish. Nonexposed steel sections may also need to be covered with a protective coating in areas where durability is a concern (e.g. areas prone to corrosion due to exposure to weathering or wet/dry cycling). It is important to note the addition of a thick topcoat or too many layers can prevent the intumescent coating underneath from activating in a fire. This is not a concern for new construction, but it must be considered when recoating steel. Engineers, architects, and coating suppliers need to carefully plan to mitigate this potential situation. |
When working in the other direction and looking at stronger/heavier steel sections, the same principle holds true, as shown in Figure 7. Here, the blue dot represents the lowest W/D listed in ANSI/UL 263 and ASTM E119. The two-hour DFT requirement at this W/D ratio of 1.74 is 2.5 mm (98 mils). Per UL guidelines, it is acceptable to coat sections with a greater W/D ratio. For example, 1.8 (green dot) with the same minimum 2.5-mm DFT. However, UL does not permit specifiers to extrapolate a reduced DFT for stronger steel sections (orange X) because it has not tested sections beyond the 1.74 W/D ratio. Additionally, UL does not allow specifiers to extrapolate data for lighter steel sections (red X). Specifiers must instead follow the blue line up to match a lower W/D ratio with the correct minimum DFT.
Conclusion
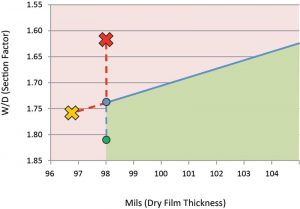
When a steel-framed building catches fire, the fate of the structure—and the safety of occupants in, on, or around the structure—may come down to a layer of passive fire-protection coatings. To ensure the steel has the appropriate fire-resistance rating, engineers and architects must specify the intumescent coating DFT for each steel section. This specification should only rely on UL’s published data, and not extrapolated data, to avoid the risk of applying too little or too much coating material. As such, UL is reminding coating suppliers, subcontractors, structural engineers, architects, and fire engineers to avoid extrapolating its data. UL first published an updated position on the issue in 2014 and added language to the ANSI/UL 263 and ASTM E119 specification in 2017. Last October, UL said extrapolated thicknesses beyond published UL designs are not considered acceptable without additional supporting test data and are therefore outside the scope of the UL certification.
Intumescent coatings are universally accepted for passive fire protection applications. However, when UL data is unavailable for a particular structural steel section, one must be aware of the recommendations to employ an intumescent coating thickness based on extrapolated data. It is advisable to follow UL guidelines and find a safe, workable alternative to arrive at the proper DFT specifications. In many cases, advanced fire engineering design principles can help to resolve issues associated with unlisted steel sections. However, the applicator and the manufacturer must make the ultimate decision on the applied DFT for a given steel section.
Intumescent coatings are not the only option for passive fire protection. Alternative building systems include cementitious fire-resistive materials and fire-rated boards, either of which may be used in combination with intumescent coatings. These passive materials work differently than coatings by providing a physical barrier of cement or gypsum, respectively, to slow down the transfer of heat to the steel substrate underneath the materials. These materials present their own specification challenges.
Bob Glendenning is a structural engineer and the global fire engineering manager for the fire engineering and estimation team at Sherwin-Williams Protective & Marine Coatings that supports the specification of engineered fire-protection solutions based on simple and complex calculations, as well as inputs from building information modeling (BIM) software. Glendenning spent more than 20 years in the steelwork industry before joining Sherwin-Williams to lead its fire protection team 17 years ago. He can be reached at bob.glendenning@sherwin.com.