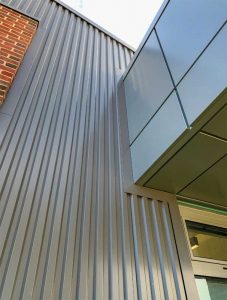
Insulated metal panels
IMPs are designed to give the architect and owner an easy ‘assembly,’ satisfying the need for ci, an A/WB, and an exterior skin with one product. These panels are made by creating a sandwich with insulation and metal panels as the finished interior and exterior of the building. Sealant is applied in the field on each tongue before being inserted into the grove of the last panel. Insulated panels are available in lengths up to 15 m (50 ft) but are typically used in 3-m (10-ft) lengths for ease of handling and installation. While manufacturers suggest panels can be modified in the field, it can be difficult to do so due to the size and thickness of the panel. The weakest point of the panel is the joint because the joint sealant is the primary vapor, air, and water barrier. Joint sealants are not designed to last more than a couple of years and will eventually fail, causing the entire vapor, air, and water barrier to be left open. Insulated panels are not designed for recycling, so their carbon footprint is high. There are NFPA 285-certified panels, but this adds to the cost. Most panels come in either an embossed or striated finish. They can be manufactured from many types of materials including aluminum, but the standard is galvanized steel. Custom colors or finishes are difficult to get, as the manufacturing process is focused on exceeding minimum volume levels of production. There is no waterproofing warranty for insulated panels without additional control layers, which would make either MCM or single-skin a more affordable option.
IMPs tend to be the least expensive and are suitable for cold storage facilities and refrigerated buildings.
It is pertinent to note IMPs are not available in custom-sized panels or angles. If the façade is not square, it is better to use either composite or single-skin panels. A secondary A/WB is recommended for long-term performance of IMPs.
Single-skin panels
Single-skin panels can be manufactured large or small, flat or bent. However, one must be careful with using panels larger than 762 x 2438 mm (30 x 96 in.) due to the possibility of oil canning. Oil canning is prevented by increasing the thickness of the material proportionate to panel size. Single-skin panels can make up the exterior portion of a rainscreen assembly, which would further include an A/WB and ci. The carbon footprint is low because all parts and pieces are easily separated, sorted, and recycled. The advantage of using single-skin metal is one can design custom shapes, sizes, and colors. The NFPA 285 requirement does not add cost to single-skin panels, as the major factor determining the rating would be the known combustibility of insulation. Color of the material is more easily customized through the use of small coil runs (around 557 m2 [6000 sf]) or post-painting. The use of exotic materials is widely used for single-skin, and is only limited to what is available on the market. Integrated wall assembly warranties covering the entire rainscreen system are available. The overall cost of this type of system is typically less than MCM, but, on occasions, greater than insulated panels.
Putting it all together
Making the assembly work together is a different challenge. The assembly detailed below works in Ft. Lauderdale, Miami, Dallas, Texas, Minnesota, and Seattle, Washington. With the detail below one can reach any R-value, keep the dewpoint on the exterior of the building, and manage the moisture indefinitely. The assembly starts with an air/water/vapor barrier with the appropriate perms for the hygrothermal region, mineral wool ci, vented hat channels to allow thermal convection, and a single-skin metal panel. The key to this assembly is the mineral wool insulation. It is permeable to allow excess moisture to escape the space. It is naturally hydrophobic, so it sheds water. When it gets saturated it will dry out quickly. By using this assembly one can avoid the many pitfalls of water being trapped on the inside of the assembly by having a nonporous component. One can also meet all requirements for R-value by using the analytical design-based method versus the prescriptive.
When specifying a metal rainscreen assembly, it is best to keep it simple. It is recommended to start with an A/WB based on the hygrothermal region, add as much mineral wool insulation as possible to the exterior to meet R-value requirements, and then include batt to achieve the required R-value. Also, use vented hat channels to allow thermal convection.