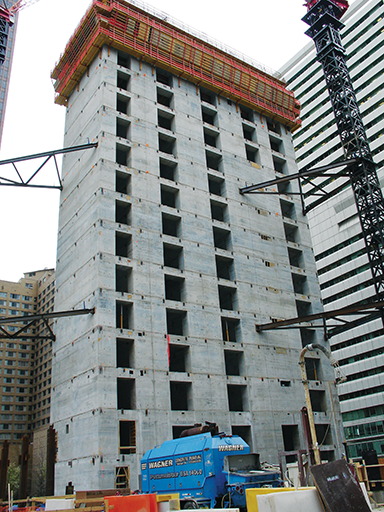
by Andrew Pinneke, PE, LEED AP
Resisting natural disasters and reducing environmental impacts are major challenges in the United States. During an average year, there are 10 tropical storms (six of which become hurricanes) and more than 1200 tornadoes touching down.
In South Florida, Hurricane Andrew left a wake of destruction in 1992 that totaled more than $25 billion in property damage and resulted in 44 fatalities. Along the Gulf Coast, Hurricane Katrina caused widespread devastation in 2005, resulting in at least 1833 fatalities and $108 billion in property damage. In 2012, Hurricane Sandy affected the entire eastern seaboard and caused $65 billion in damage. In densely populated New York City alone, this superstorm took the lives of 53 residents, destroyed thousands of buildings, and caused $19 billion in damages and lost economic activity.
Almost every state has been affected by extreme windstorms (Figure 1). Each year, tornadoes with gusts as high as 320 km/h (200 mph) in the Midwest and lower Great Plains result in more than 100 fatalities and 1500 injuries. In 2013, a tornado cut a swath 3.2 km (2 mi) wide and 19 km (12 mi) long through Oklahoma City, causing 26 fatalities, 400 injuries, and $2 billion in property damage.
Few regions of the country escape the wrath of Mother Nature. Flooding, which accounts for more than 75 percent of federally declared disaster areas, is the most prevalent disaster event in the United States, and earthquakes pose serious risks not just in California, but also many Midwestern and Eastern areas. About 5000 seismic events occur each year, with approximately 400 capable of causing damage to building interiors and 20 able to cause structural damage. For example, the 1994 Northridge earthquake in California caused 57 deaths, over $20 billion of damage, and destroyed or damaged 90,000 homes, offices, and public buildings.
Figure 1
Over the past decade, the frequency and overall economic damage inflicted by destructive wildfires also has increased in more than three-fourths of the United States. In 2012, some 38 catastrophic wildfires produced $1.1 billion in economic losses according to estimates in a January 2013 report by Munich Re. The wildfire problems are not limited to California and the Southwest, as there has been a recent trend toward larger and more destructive wildfires in the Southeast and Midwest.
Championing resilience
Standards for construction and code-related enforcement vary widely across the country. Some states have adopted building codes applicable to virtually every type of structure, while others employ lesser degrees of regulation.
The International Code Council (ICC) has developed the most widely adopted set of codes to unify the nation’s building regulatory systems. Based on thoroughly tested scientific and engineering principles, these model codes provide standards used in the design, build, and compliance process to construct safe, sustainable, secure, and resilient structures.
The Federal Emergency Management Agency (FEMA) and National Oceanic and Atmospheric Administration (NOAA) provide additional guidance on how to design buildings to lessen the impact of natural disasters. This guidance to designers includes their support of the ICC standards, which are equivalent to the National Earthquake Hazard Reduction Program (NEHRP) for New Buildings and reflect the current state-of-the-art engineering requirements for wind, such as those found in American Society of Civil Engineers (ASCE) 7, Minimum Design Loads for Buildings and Other Structures.
The Fortified for Safer Business program of the Insurance Institute for Business and Home Safety (IBHS) is another valuable resource. This ‘code-plus’ program offers design criteria and construction techniques that greatly increase a new commercial building’s durability and resilience to natural and manmade hazards.
In recognition of the increasingly important need for enhanced resiliency of buildings, the National Building Museum in Washington, D.C., is hosting a Designing for Disaster exhibition, which runs through August 2. This major exhibition showcases innovative research, cutting-edge materials and technologies, and disaster-resistant designs for creating safer, more durable and disaster-resilient communities. When the exhibition opened in May 2014, a group of 20 prominent industry organizations, led by the National Institute of Building Sciences (NIBS) and the American Institute of Architects (AIA), issued a joint statement pledging to research design and construction best practices, educate their memberships, and advocate for governmental policy changes.
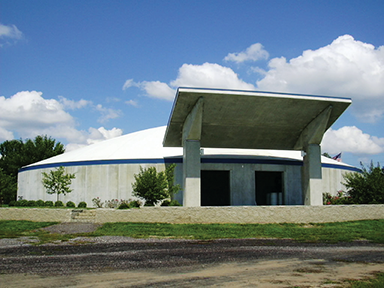
Concrete’s role in resilient construction
In areas susceptible to natural disasters, architects must design durable, high-performance buildings with materials that not only offer resistance, but also continue to function after a catastrophic event. High-performance concrete (HPC) structures are especially suited to provide protection against natural hazards and help ensure critical services—like hospitals, evacuation shelters, and emergency operations centers—can remain in operation even under the harshest of environments.
Concrete’s inherent strength and stiffness provide a primary advantage, which can be enhanced through building design, mix formulation, and reinforcement to withstand the forces of extreme winds and flying debris. Concrete not only provides the resilience needed to protect against tornadoes and hurricanes, but its structures are also resistant to flood damage, earthquakes, wind-driven rain, corrosion, decay, insect infestation, and mold and mildew formation. The slow rate of heat transfer and inherent fire resistance enable it to tolerate flames, and slow their spread. Concrete buildings also have excellent aesthetic versatility, providing an almost endless array of colors and textures to help minimize the cost of building repairs following a disaster.
All these attributes are built into a concrete structure, so if disaster strikes, restoration is usually a matter of replacing contents and some finish materials. This is a much less daunting and expensive process than complete rebuild or build out of interiors.
In Iowa, where the annual State Fair draws thousands of visitors during the heart of tornado season, the State Fair Board called for the construction of a 483-m2 (5200-sf) shelter to help protect campers in the event of a major storm. The Iowa State Fairgrounds tornado shelter features a unique curved design to provide superior wind resistance. The roof and the curved walls of the structure are constructed of 305-mm (12-in.) thick precast concrete panels that use a special framework to retain their shape, and the interior partition walls are constructed of fully reinforced concrete masonry units (CMUs). The building’s exterior concrete canopy is mounted atop concrete piers to provide additional weather protection. The canopy is designed to withstand 400-km/h (250-mph) winds and to prevent them from becoming a debris hazard themselves during a high wind event.
Concrete is also taking center stage in construction projects in the Gulf Coast region, which is still recovering from the devastation caused by Hurricane Katrina in 2005. At the time of the storm, Alabama, Louisiana, and Mississippi did not have statewide building codes for non-state-owned buildings. As a result, Hurricane Katrina’s storm surge, high winds, floodborne debris and long-duration flooding exceeded flood depths and loads used in building design, causing massive and widespread structural failure.
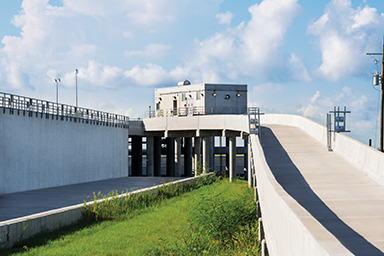
In the wake of Katrina, levees for Greater New Orleans were brought up to modern building code standards, and the U.S. Army Corps of Engineers (USACE) constructed the Inner Harbor Navigation Canal (IHNC) Surge Barrier to improve the resiliency of Gulf Coast communities. The largest of its kind in the world, the barrier incorporates more than 53,520 m3 (70,000 cy) of a self-consolidating concrete mix that achieved strengths greater than 27,580 kPa (4000 psi) within 48 hours. The backbone of the main barrier consists of 1271 concrete vertical piles, each measuring 1676 mm (66 in.) in diameter and 44 m (144 ft) in length and weighing 96 tons.
Another focus of reconstruction efforts is the need for critical and essential facilities to remain functional during a catastrophic event. When completed, the new University Medical Center (UMC) in downtown New Orleans will be the only Level One trauma center in southeast Louisiana, so keeping it functional during future disasters will be essential. The UMC project, scheduled to be competed this year, is using fly ash and slag cement in specialized concrete mix designs for added performance, and to help it meet flood-resistant construction standards.
This 213,700-m2 (2.3 million-sf) project is one of the largest healthcare campuses under construction in the country. It includes 120,775 m2 (1.3 million sf) of concrete decking delivered at a weekly rate of 5575 m2 (60,000 sf). The high-performance concrete building envelope for the seven-story, 52,025-m2 (560,000-sf) Inpatient Tower, just one component of the 15-ha (38-acre) campus, has been designed ?to endure hurricane-force winds up to 240 km/h (150 mph), yielding a facility that will enhance public safety in the event of natural disasters.
HPC for stronger, more durable buildings
The specification of high-performance concrete (HPC) continues to grow as superior structural resiliency and durability performance become increasingly important. HPC mixtures incorporate supplementary cementitious materials (SCMs)—such as slag cement, fly ash, and silica fume—as separate components or combined in blended cement. The greatest physical benefits imparted by SCMs and blended cements (ASTM C595, Standard Specification for Blended Hydraulic Cements, and/or ASTM C1157, Standard Performance Specification for Hydraulic Cement) can be seen in the properties concrete exhibits after hardening.
Strength
Concrete gains strength at a decreasing rate over time, so varying the concrete mixture can significantly alter the rate and/or ultimate strength gain as defined by ASTM C39, Standard Test Method for Compressive Strength of Cylindrical Concrete Specimens. Slag cement and fly ash typically lower early strengths (one to 14 days) but can significantly improve long-term strength development (28 days and beyond), depending on the proportions and materials used (Figure 2). For example, Class F fly ashes tend to have a slow strength gain curve contributing mainly to the strength beyond 28 days, whereas silica fume contributes primarily to the three to 28 day strengths. Both compressive and flexural strengths can increase markedly at 28 days and beyond with the addition of most SCMs.
Figure 2
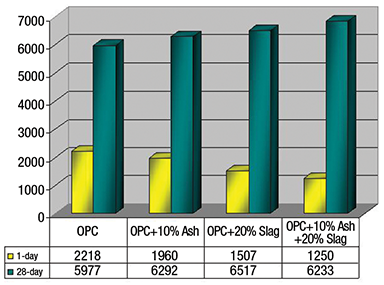
Permeability
Slag cement, fly ash, and silica fume all can significantly reduce the permeability of concrete to the ingress of chlorides, sulfates, and other aggressive agents present in rain, groundwater, and seawater. Silica fume has a profound effect on permeability, exhibiting as much as a five-fold reduction in permeability when using only eight percent silica fume.
Alkali-silica reaction
Most SCMs can effectively prevent excessive expansion and cracking of concrete due to alkali-silica reaction (ASR). The amount of slag cement required depends on the nature of the slag cement, the reactivity of the aggregate, and the alkali loading of the concrete. In most cases, 50 percent slag cement is sufficient with highly reactive aggregates. The amount of fly ash required typically is in the range of 15 to 55 percent, depending on the chemical composition of the ash, reactivity of the aggregate, and the alkali loading of the concrete.
Generally, Class F ashes are much more effective in controlling expansion due to ASR than Class C ashes. Silica fume can control ASR, but the amount required generally results in poor constructability. Consequently, blends of slag cement and silica fume, as well as blends of fly ash and silica fume, are often used as an alternative to straight silica fume replacement because they can be used to achieve a synergistic effect in mitigating expansion due to ASR, while producing a workable concrete.
Sulfate attack
Concrete containing SCMs generally offer superior resistance to sulfate attack as they lower the permeability, restricting the ingress of sulfate-bearing ions. In numerous cases, they additionally reduce the compounds that can react with sulfates to form deleterious compounds. Typically, slag cement, silica fume, and Class F fly ashes are effective in improving sulfate resistance. The effectiveness of Class C fly ashes depends on the ash chemistry and the replacement level.
Thermal stress
If the temperature differential between the concrete’s surface and interior is too high, the result can be cracking and loss of structural integrity. Employing high replacement levels of slag cement and/or fly ash in properly proportioned mixes can reduce the peak temperatures, as well as the rate of heat generation. Reducing the heat of hydration of the mix can moderate the development of thermal stresses within the concrete and prevent cracking.
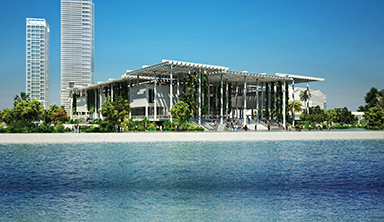
Soaring to new heights in resiliency
A major advantage of concrete construction for high-rise buildings is the material’s inherent properties ?of heaviness and mass, which create lateral stiffness, or resistance to horizontal movement. Occupants of concrete towers are less able to perceive building motion than occupants of comparable tall buildings with non-concrete structural systems. High-strength concrete also provides the most economical way to carry a vertical load to the building foundation.
By employing high-strength concrete, the column size is reduced. At the same time, the amount of vertical reinforcement can be reduced. The net result is the least expensive column is achieved with the smallest size column, the lowest amount of reinforcement and the highest readily available concrete strength. As a result, concrete has become the material of choice for many tall, slim towers.
Two recently-constructed, high-profile skyscrapers feature concrete designed to offer the utmost safety and resilience. Philadelphia’s Comcast Center, the tallest building in the city at 297 m (975 ft), required 38,230 m3 (50,000 cy) of concrete containing slag cement for the high-performance project, of which 27,525 m3 (36,000 cy) was specified at 68,950 kPa (10,000 psi) for the central inner core. The building’s thick exterior core walls—1370 mm (54 in.) up to the 20th floor—further minimize deflection due to wind forces, and all its elevators, sprinklers, communications systems, and stairwells are encased within the concrete core.
However, it is Manhattan’s One World Trade Center that is setting a new standard for stronger, safer urban landscapes. Rising a symbolic 1776 ft (i.e. 541 m), this landmark skyscraper is the tallest in the Western Hemisphere. It has a massive cast-in place, reinforced concrete inner core that runs the full height of the tower—an extra-strong backbone that provides support for gravitational loads as well as resistance to wind and seismic forces. The concrete core walls are 1 m (3 ft) thick or more above ground and up to twice that below grade. Higher up, the concrete core walls slim down to 0.6 m (2 ft) thick.
The 152,910 m3 (200,000 cy) of concrete used in the tower’s superstructure—with a strength that has never been used on such a scale in building construction—was custom-designed to ensure high levels of durability, as well as control the heat of hydration during the mass concrete pours to minimize cracking. Supporting columns on the first 40 floors were made from 82,740 to 96,525 kPa (12,000 to 14,000-psi) self-consolidating concrete and the upper floors with 59,295 to 68,950-kPa (8600 to 10,000-psi) mix designs.
To meet the compressive strength requirements, the design and engineering team relied on a highly specialized concrete mix that included fly ash, silica fume, and slag cement. High-strength concrete was the ideal material for meeting the high-priority safety requirements for One World Trade Center because elevators, stair enclosures, and other supporting members relied on to resist wind, seismic, and other impact forces are designed with an extra measure of durability and resilience.
Innovative new UHPC materials
The concrete industry continues to explore new ways of making buildings stronger, safer, and, as demonstrated by one of its newest products, more aesthetically pleasing. Ultra-high-performance concrete (UHPC) is blended with high carbon metallic or polyvinyl alcohol (PVA) fibers, and has a unique combination of properties including strength, ductility, durability, and aesthetic design flexibility.
The Perez Art Museum in Miami is situated on Biscayne Bay, where frequent tropical storms and exposure to the salt and sea air can cause serious problems for buildings. UHPC was used for the building’s approximately 100 long-span, precast vertical mullions to blend with its cast-in-place concrete elements and support the large curtain wall glazing that surrounds the building. Due to its exceptional strength, the UHPC made it possible to create thin, sinuous mullions up to 5 m (16 ft) tall, allowing unobstructed views over the museum’s veranda while meeting the area’s hurricane resistance standards and offering increased resistance to corrosion from the sea air.
Conclusion
Although the frequency of natural disasters has not increased in the last 40 years, their safety risks and economic costs are rising dramatically due to increased urbanization and population concentration along the coasts and flood-prone areas. More than 50 percent of the U.S. population and $10.64 trillion ?of insured property is located in areas vulnerable to hurricane destruction, and nearly 134 million people will be living in hurricane-prone states by 2020.
It is clear stronger, safer concrete buildings will play an important role in protecting these growing communities from the humanitarian and economic costs of major natural disasters. In addition to satisfying minimum life safety provisions, enhancing the resilience of buildings through mandatory requirements should be a priority for every jurisdiction, especially communities in disaster-prone communities.
Relevant ASTM Standards |
• ?ASTM C989, Standard Specification for Ground Granulated Blast-Furnace Slag for Use in Concrete and Mortars; • ?ASTM C618, Standard Specification for Coal Fly Ash and Raw or Calcined Natural Pozzolan for Use in Concrete; • ?ASTM C1240, Standard Specification for Silica Fume Used ?in Cementitious Mixtures; • ?ASTM C150, Standard Specification for Portland Cement; • ?ASTM C595, Standard Specification for Blended Hydraulic Cements; and • ?ASTM C1157, Standard Performance Specification for Hydraulic Cement. |
Andrew Pinneke, PE, LEED AP, is a construction specialist at Lafarge, consulting on a wide range of sustainable construction and building performance issues while coordinating sustainable construction and concrete technology transfer efforts. He worked as a structural engineer for almost a decade before joining Lafarge. He sits on the National Ready Mixed Concrete Association (NRMCA) Sustainability Committee, and several American Concrete Institute (ACI) committees, along with the ACI Foundation’s Strategic Development Council (SDC). Pinneke can be contacted via e-mail at andrew.pinneke@lafarge.com.