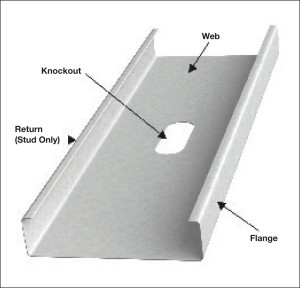
As EQ studs are formed from steel with higher yield strength, they have greater pullout and shear values. Higher pullout values are advantageous when attaching handrails and fixtures. Due to various factors, EQ studs meet the same requirements as traditional studs, despite being thinner. To begin with, EQ stud manufacturers have taken advantage of new, higher-strength steels, such as those listed in ASTM A1003, with yield strengths ranging from 227.5 to 551.6 MPa (33 to 80 ksi), as well as new processing methods. They may have also added more steel into the strip width used to make the studs. Reinforcing ribs and other devices have been added to flanges and/or webs.
Additionally, new technology is being used by manufacturers to develop high-performance coatings to protect the base steel and meet the protective coating requirements of ASTM C645. These coatings use corrosion-inhibiting and adhesion-enhancing formulas to chemically react and bond with the substrate’s zinc, producing a synergistic effect that greatly enhances the corrosion resistance.
The coatings can be applied to any zinc or zinc-alloy coated substrate. As an added advantage, they fill any imperfections—fractures or porosity—in the existing substrate.
EQ studs differ from traditional flat studs. For example, they generally have a minimum thickness of 0.381 mm (15 mil) instead of 0.455 mm (18 mil). Additionally, because they are thinner than traditional studs, the majority of their physical structural properties are lessened. However, with regard to performance, they perform as well or better than traditional studs because of the stronger yield strength steel and enhanced section configuration.
ASTM C754: Steel stud installation
The industry standard for non-structural steel framing members’ installation is ASTM C754, Standard Specification for Installation of Steel Framing Members to Receive Screw-attached Gypsum Panel Products, which covers all members made in conformance with ASTM C645. Steel tracks for non-load-bearing interior partitions are secured to the supporting structure. If the floor is a concrete slab, installers should fasten the tracks with concrete stub nails, expansion anchors, shielded screws, or power-driven fasteners. If floors are wooden, tracks should be fastened with screws (25 mm [1 in.] minimum penetration) or nails (38 mm [1 1/2 in.] minimum penetration). Tracks can be secured to suspended ceilings with ‘molly’-type expandable fasteners commonly used in drywall installation, toggle bolts or screws fastened into channels, splines, T-runners, or other framing members.
All fasteners should be located 50 mm (2 in.) from each end and spaced a maximum of 609 mm (24 in.) oc. When attaching track-to-stud—which is only required at door jambs—partition intersection and borrowed light frames, a sharp point pan head or low-profile, Number 6 diameter screw with a flat surface on the underside of the head should be used.
To engage floor and ceiling tracks, full-length steel studs should be inserted between tracks, positioned vertically, and with their open side facing in the same direction. They must be spaced 406 or 609 mm (16 or 24 in.) maximum oc based on the gypsum board’s thickness, the board’s ability to span the distance between studs, the board’s number of layers, and, for rated partitions, requirements of the fire rating. Stud spacing is not permitted to exceed spacing requirements by more than ± 3.2 mm (1/8 in.). Aligning the studs properly permits correct bracing and utility runs, and prevent stepped or uneven joint surfaces.
ASTM C754 interior framing composite limiting heights tables are not up to date with the requirements of ICC-ES AC86 for composite walls. The version currently published allows for a 0.25 load reduction, which is no longer allowed by IBC. (To get current limiting height information, the manufacturer should be consulted for tables.) New testing is scheduled to be completed this year to update these tables. Composite limiting height data can only be applied to walls where gypsum board is installed on both flanges of the stud for the wall’s full height. This allows higher limiting heights without needing a heavier stud or lesser spacing.
Non-composite conditions, however, are common in all structures. They occur:
- where the gypsum board stops at the ceiling level, but the stud continues to the deck;
- where the gypsum board is only partial height on one or both sides of the stud; or
- when the stud only has gypsum board on one side.
When these conditions occur, composite limiting height tables cannot be used.
Studs should be located no more than 50 mm (2 in.) away from the intersection of through and abutting partitions. At partition corners, a stud should be installed so it forms the outside corner. Following the application of a single layer of board to this stud, a second stud should be installed in the abutting track. This second stud’s web should be screwed through the board into the first stud’s flange.
Headers should be installed over doorways and other openings, securely attached to the adjacent vertical studs. ASTM C754 sets no limit on the height or width of openings. An engineered solution may be needed, which may require more than a single-track header.
Fire-rated wall assembly requirements
Ensuring fire safety in building designs is critical. Laboratories perform fire testing for various building materials, including wall assemblies. This testing is designed to determine how quickly fire can raise the temperature to unacceptable levels and how building materials react. The results are fire-resistance ratings (which gauge a construction assembly’s ability to confine and isolate flames within a zone composed of fire-resistance-rated walls), ceiling, and floor assemblies. Fire-rated assemblies are tested and certified in their entirety.
There are several important things to remember about fire-resistance-rated wall assemblies and the role of steel studs in the assemblies. A fire-rated partition must adhere to the way the actual tested assembly was constructed—no variation is permitted. Many commonly used fire-rated assemblies were tested decades ago, and there is no requirement for retesting once an assembly passes the fire test. Fire-rated assemblies using EQ studs, however, are more likely to have current fire-testing reports, as they are newer products.
EQ studs have either been fire-tested or have gone through an extensive engineering evaluation in order to be listed in an Underwriters Laboratories (UL) fire-rated assembly. It is important to examine current wall assembly schedules and research the components to determine whether EQ studs meet the project’s framing requirements.