by Nicole Richard
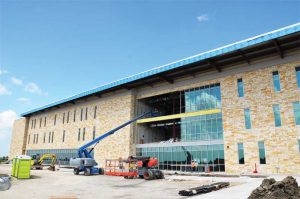
The use of masonry cavity walls dates back to ancient Greece. While this construction method is still thriving, it has evolved to meet the performance needs of 21st century buildings. One of the modern adaptations is the use of rigid foam insulation to maximize thermal efficiency. To capitalize on the material’s benefits and to ensure code compliance, proper project specification requires the consideration of a few critical insulation performance factors.
Masonry, also known as brick- or stone-laying, has been the cornerstone of some of the most significant architectural wonders of the world, from the Pyramids of Giza and the Roman Colosseum to the more ‘recent’ Taj Mahal. As one of the oldest construction methods, masonry has shown its ability to withstand the test of time by adapting to support modern building standards. Take masonry cavity walls, for example—when they were first constructed by the ancient Greeks, the remnants were observed by archeologists as two stone walls set roughly 50 mm (2 in.) apart. Masonry cavity walls have now evolved to incorporate new technology and safety measures, provide better moisture control, and, of course, improve energy management.
As the Masonry Advisory Council (MAC) explains, “Today, masonry cavity walls are used extensively throughout the United States in all types of buildings. The primary reasons for their popularity are superior resistance to rain penetration, excellent thermal properties, excellent resistance to sound transmission and high resistance to fire.”
Building masonry cavity walls in the 21st century requires a contemporary approach that maximizes the inherent benefits of these wall types. One such progressive technique is the addition of continuous rigid foam insulation. By incorporating continuous rigid foam insulation in the masonry cavity wall, building teams can effectively improve a structure’s total thermal efficiency. However, to make sure the masonry cavity wall’s moisture and fire performance characteristics remain unimpeded, the specified insulation material must adequately resist moisture penetration and combustion.
Overview of masonry cavity walls
Masonry cavity walls consist of two separate masonry layers (wythes) with an air space between them. The two wythes are connected by corrosion-resistant wall ties. Wythes can be built of brick, structural clay tile, concrete blocks, and stone or other type of masonry materials. The double-wythe configuration results in superior moisture protection of the building. The outer wythe provides a critical first line of defense, helping prevent rain water from reaching the inner wythe. Moisture making it past the outer wythe drains down its inside face to flashings channeling it back out of the wall via weep holes. Since the air space between wythes is crucial for managing the moisture, the Masonry Society’s (TMS’s) 402-11, Building Code Requirements for Masonry Structures, (section 6.2.2.8.2) (Consult the Masonry Society (TMS) 402/602-16, Building Code Requirements and Specification for Masonry Structures, 2016.) calls for:
A 4-½ in. (114-mm) maximum distance between the inside face of the veneer and the outside face of the masonry or concrete backing shall be specified. A 1-in (25.4-mm) minimum air space shall be specified.
In addition to exceptional moisture management, the multilayer wall configuration aids in thermal performance. “Both wythes act as a heat reservoir, positively affecting heating and cooling modes,” notes MAC. As an added benefit, the double-wythe air space configuration dampens sound, for a quieter indoor environment.
To maximize a masonry building’s insulating power without hindering its inherent moisture repelling and thermal properties, special care must be taken when implementing continuous insulation (ci).