Continuous insulation for masonry cavity walls
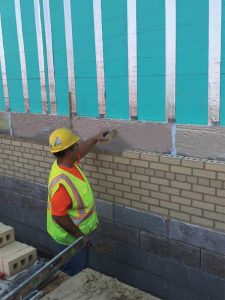
The American Society of Heating, Refrigeration and Air-conditioning Engineers (ASHRAE) 90.1, Energy Standard for Buildings Except Low-Rise Residential Buildings, defines ci as:
Insulation that is continuous across all structural members without thermal bridges other than fasteners and service openings. It is installed on the interior, exterior, or is integral to any opaque surface of the building envelope.
To get the best performance from the cavity wall, ci is installed on the inner wythe’s outside face. In this configuration, insulation serves as the first line of defense against heat loss from the building to the outdoors. The air space and the insulation work together to improve the assembly’s overall thermal performance, without disrupting the channeling of moisture from the outer wythe to the wall’s exterior.
ASHRAE 90.1 was established in 2007. It requires ci in most new construction (choosing to establish energy compliance using the ‘prescriptive’ approach in lieu of the ‘performance’ method), as well as new portions of existing structures and their systems, except low-rise residential buildings, for almost every climate zone. According to the U.S. Department of Energy (DOE), as of December 2018, 39 states have adopted commercial energy codes that meet or exceed ASHRAE’s standard (U.S Department of Energy Status of State Energy Code Adoption: Commercial Buildings.). California’s Title 24 has taken energy efficiency regulation even further by calling for all new commercial facilities in the state to be zero net energy (ZNE) by 2030.
Specifying continuous insulation in masonry cavity walls
Of the ci options available, extruded polystyrene (XPS) is widely used for masonry cavity walls in the United States. However, building teams have successfully employed a range of insulations to meet ci standards, including mineral wool, sprayed polyurethane foam (SPF), as well as other rigid foams, including expanded polystyrene (EPS) and polyisocyanurate (ISO). In regard to the range of cavity wall insulation options, the MAC Design Guide for Taller Masonry Cavity Walls says, “a foil faced, polyisocyanurate insulation is the most beneficial.” ISO is known for its use as roofing insulation, but it is also recommended in masonry cavity walls for its thermal, moisture, and fire performance as well as its resistance to solvents.
Additionally, ISO offers increased R-value per inch versus mineral wool, XPS, and EPS insulations. The high R-value per inch of ISO provides high-performance ci, while enabling the insulation layer to take up less air space within masonry cavity wall assemblies. Benefits of a thinner insulation layer include added room for the mason to work when installing the exterior brick veneer and reduced risk of mortar clogging the airspace within the cavity. Masonry magazine reports some building professionals are moving to wider masonry cavity walls. However, narrower walls reduce product and labor costs since fewer materials are needed in the building process.
To determine which insulation is well-suited for masonry cavity installation, design professionals must closely examine commonly used masonry cavity wall insulation. The following will evaluate the thermal, moisture, and fire performance, along with solvent-resistance properties, of multiple ci options.
Thermal performance
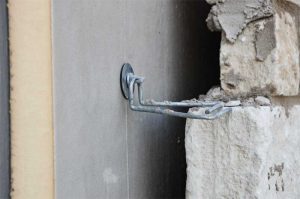
As defined earlier by TMS 402-11, a minimum air space must be maintained within a cavity wall to allow for critical moisture management. Keeping this in mind, specifying insulation to maximize thermal performance without hindering the air gap in a cavity wall is crucial to creating a code-compliant, energy-efficient masonry building.
Since ISO offers increased R-value per inch, it provides effective ci while allowing for a thinner overall wall assembly. For example, the R-value of foil-faced ISO products is R-6.5 per inch and R-6 for other ISO wall products. Comparatively, other rigid foams are in the 3.6 to 5 R-values per inch range with mineral wool falling in the 3 to 4.2 R-value per inch range. By reaching higher, code-mandated R-values without increasing insulation thickness, ISO is able to provide flexibility in the wythe air space gap without increasing the wall’s thickness.
Moisture
If a masonry cavity wall is performing as intended, moisture or excess moisture vapor breaching the outer wythe will rarely reach the insulation attached to the inner wythe. In the event the insulation is compromised, either from damage to the outer wythe, seepage from the top of the wall, or other factors, it is important the insulation does not readily absorb water. When insulation is damp, its R-value is dramatically impacted because the water compresses the insulating air space between material layers. When insulation is compressed, the R-value is negatively impacted because there is less insulating air space. Additionally, if insulation is subject to continuous moisture retention, it is at risk of deteriorating.
Due to their closed-cell physical makeup, foam insulation boards—this includes EPS, XPS, and ISO—naturally resist moisture intrusion, to varying degrees. Their physical properties can provide a great baseline for moisture performance. However, there are other features to consider. For instance, foam insulation boards with facers have the added advantage of enhanced water resistance. Consider ISO products with coated-glass (CG) mat or foil facing. The Polyiso Insulation Manufacturers Association (PIMA) explains in its Technical Bulletin 401, “The foil face on the polyiso insulation is an impermeable material, which enhances long-term thermal performance.” This, in turn, protects the building’s energy efficiency in the event of outer wythe failure or other moisture intrusion.