Fire performance
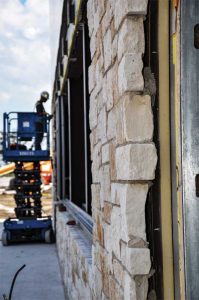
Several wall assemblies, including masonry cavity walls, must meet criteria under the National Fire Protection Association (NFPA) 285, Standard Fire Test Method for Evaluation of Fire Propagation Characteristics of Exterior Non-Load-Bearing Wall Assemblies Containing Combustible Components. NFPA 285 test results are either “pass” or “fail” based on an evaluation of vertical and horizontal flame spread and conformance with temperature limits within the assembly. With limited exceptions, International Building Code (IBC) section 2603.5.5, “Vertical and lateral fire propagation,” requires wall assemblies in Type I, II, III, and IV construction using foam plastic insulation to pass NFPA 285 testing requirements. Although the title says “nonloadbearing,” NFPA 285 also applies to loadbearing walls, so masonry cavity walls are not exempt.
Masonry cavity walls are inherently fire resistant due to the noncombustible properties of brick, clay, stone, and other components of the wall. However, since a cavity wall system may include flammable materials, it is critical to consider code-required fire performance when selecting insulation.
NFPA 285 is particularly rigorous in that it evaluates entire wall assemblies, not individual products. Thus, even if a given insulation product—or other component—passes NFPA 285 in a specific assembly it does not mean the material is automatically compliant in alternate assemblies. To be included in masonry cavity walls, an insulation type must pass NFPA 285 within a particular assembly.
While critical, code compliance is just one component of the specification equation. In the event of a fire, each insulation type will perform differently. Of the polystyrene foams (EPS and XPS), both of the insulation materials are classified as “thermoplastic.” Gregory Havel, a 35-year fire service veteran explains thermoplastics will “melt, liquefy, and run down into the bottom of the cavity, and burn as a flammable liquid,” when they are exposed to fire.
In contrast, a “thermoset” plastic, such as ISO, is manufactured with chemical bonds that irreversibly harden during a fire, providing a high level of fire resistance. In other words, during a fire, ISO does not melt as thermoplastic styrene foam. Instead, thermosets develop a protective char layer. As a result of this fire performance, ISO manufacturers have developed a wide selection of products that pass NFPA 285 testing in multiple wall assemblies. Further, if a building has combustible claddings in some sections and brick in others, thermoplastics like XPS and EPS might not always have approved NFPA 285 assemblies. However, ISO does. As such, it does not require building teams to change materials in different parts of the building.
Resistance to solvents
As with most construction methods, masonry cavity wall designs often incorporate materials with petroleum-based solvents. These solvents come in the form of adhesives, preservative coatings, and waterproofing to aid in building performance and increase construction speed. Unfortunately, petroleum-based solvents can damage styrene rigid foam insulations. While this is not a primary deciding factor for choosing among insulations, as there are specially formulated solvents that can accommodate styrene rigid foam insulations, resistance to solvents helps simplify construction. When the insulation does not need to be protected from common building materials, the need to buy alternative materials or exercise additional caution around the insulation is eliminated. ISO is unaffected by common petroleum-based solvents and eliminates the worry of chemically based deterioration of the insulation.
Putting it all together – Manor High School case study
To serve a fast-growing student body in suburban Austin, the Manor Independent School District (MISD) added a new high school on an adjacent campus.
Manor High School demonstrates the advantages of ISO insulation in masonry cavity walls. Designed by Perkins + Will, the new school building has walls with rock masonry exterior cladding in some areas and metal cladding in others. It is common these days to have buildings incorporating more than one cladding, and masonry exteriors are often combined with other materials. One challenge the architects faced was providing ci within the cavity, while also meeting fire requirements under NFPA 285.
“The project was originally specified with XPS insulation, but swapping that out for ISO improved the thermal performance, and met NFPA 285,” said Darren Butler, president of a product manufacturer representative firm. “The price did not change when switching to coated-glass facer ISO for the contractor and everyone was happy and code compliant.”
Conclusion
Masonry cavity walls continue to adapt to current building practices, thanks to modern advances in building products. An important aspect of this evolution is the use of insulation within the cavity. To maximize the wall’s overall performance, it is critical the insulation is chosen carefully. Although it is commonly employed in roofing applications, ISO is gaining popularity among specifiers for use in masonry cavity walls. ISO enhances the masonry cavity wall’s inherent performance traits because of its complementary thermal conduct, moisture, and fire and solvent resistance.
Nicole Richard is a technical service specialist with Hunter Panels, focused on the company’s roof and wall insulation divisions. Richard has more than 22 years of experience in the building insulation industry, including technical services, customer service, and sales. She can be reached at nicole.richard@hpanels.com.