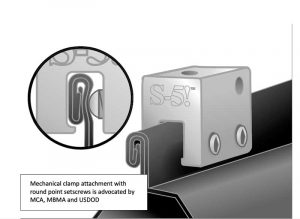
Replacement is not ‘if’ but ‘when’ the adhesive diminishes in holding strength. All adhesives weaken when exposed to heat, cold, UV, and moisture. Replacement time is often within a few years after installation, depending on orientation to the sun and other environmental factors (Figure 9).
Due to diminishing holding strength over time, testing is not feasible (e.g. at what age should testing be done?). When they fail, the adhesives can also rip away paint coatings, leading to corrosion (Figure 10). Industry groups, such as MCA, Metal Building Manufacturers Association (MBMA), and the U.S. Army Corps of Engineers (USCOE) strongly advise against their use.
What to expect with adhered attachments
At first glance, installation is simple. However, a close look at the detailed instructions reveals the process is a complex one—careful surface preparation is required as well as many days of curing time (specific temperatures for some). Expect to re-adhere stick-on parts or replace them every three to six years or so.
How to choose the best snow retention system
Since there are no industry standards or mandates for design, manufacture, use, or testing of snow guards, it is a ‘buyer-beware’ scenario, as to the appropriateness and proof of testing and engineering performed by the vendor.
How does one discern prudent product selection from sales rhetoric? In addition to understanding the art and science behind snow retention systems, one should vet the vendor and their product offerings.
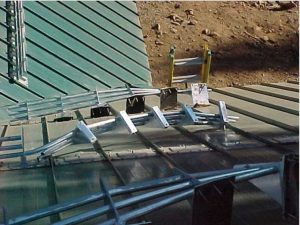
Vet and specify
Vendor transparency is requisite to adequately vet
a snow guard system. The designer should scrutinize vendor/manufacturer qualifications/certifications in order to ensure a safe, engineered application and long-term service (read MCA’s technical bulletin on “Qualifying Snow Retention Systems”).
Proof of testing
To resist the forces applied to any system, the failure point of the snow retention system must be known, and the appropriate factors of safety employed to determine allowable structural capacity. Then, the population and frequency of the system is determined, so it cannot fail. Since the system may comprise multiple components, a ‘load chain’ could result. The calculated vector forces are transmitted through this chain into the building structure. Each link (component) in the chain must be proven by testing and/or engineering analysis. The weakest link determines the strength of the chain. The requisite engineering cannot be completed without reliable, extensive testing.
Anchorage of clamps or brackets to the roof specimen should be repetitiously tested on the specific substrate of the project. A minimum of three test repetitions should be conducted. In the case of SSMR clamped systems, the testing should be specific to roof materials, gauge, manufacturer, and seam profile of the project, as holding capacities differ widely.
Testing of these system components should be conducted by a third-party lab with the International Organization for Standardization (ISO) 17025, Testing and Calibration Laboratories, accreditation. It is also not scientifically acceptable to apply a test result from one set of specimens to another similar-styled roof product or assembly.