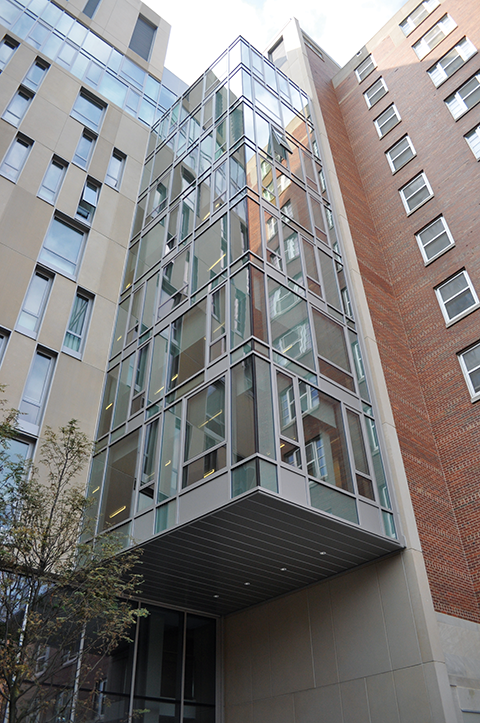
by Stephen Metz, PE, LEED AP
Many factors come into play when designers specify structural framing. There are so many criteria, sometimes there is no absolute answer as to which framing system would perform best. At the same time, the interests of various parties must be served, meaning the final selection does not always rest with the structural engineer.
Despite the number of variables influencing the design team’s choice of a structural system, there are a few major consistent considerations from project to project. These variables can include:
- building code requirements;
- aesthetics;
- owner preference;
- functional requirements;
- spans and/or structural depth limitations;
- cost; and
- schedule.
Building code requirements
A building’s fire resistance rating—the number of hours for which treated structural members can withstand a standard fire resistance test—is a measure influencing structural design. International Building Code (IBC) Table 601 provides the fire-resistance ratings of a building’s primary structural elements and establishes five classifications for construction types—Type I requires the highest fire-resistance ratings for its structural elements, and Type V requires the lowest. (See Figure 1.)
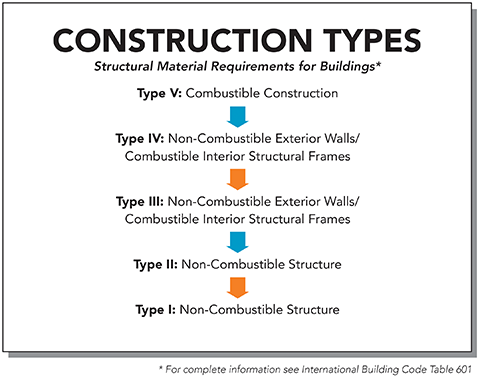
Steel, concrete, masonry, and fire-retardant-treated wood are the only structural materials allowed in Type I and II construction, which both require materials to be non-combustible. If a fire rating is required, structural steel cannot remain unprotected. Fireproofing—typically by spray-applying a cementious fireproofing material, coating with intumescent paint, or encasing in concrete—is needed to achieve the required rating. Masonry and concrete achieve the ratings with little to no additional considerations, though with the latter, the cover for the reinforcing steel needs to be increased beyond its typical depth to achieve higher ratings.
When designing to meet the building code, engineers have to pay attention to many tangential items. For example, IBC may require testing of an actual wall assembly to National Fire Protection Agency (NFPA) 285, Standard Test Method for Evaluation of Fire Propagation Characteristics of Exterior Non-load-bearing Wall Assemblies Containing Combustible Components, if it is designed to have combustible materials (e.g. certain kinds of insulation or vapor barriers) within its otherwise non-combustible walls.
Aesthetics and owner preference
Aesthetic considerations are a top priority for many building types and a structure’s material palette signals its overall quality and design sensibility. While one basic material may not be objectively ‘better’ than others, a designer often has an aesthetic goal in mind dictating the choice of materials right down to the structural system. Similarly, owners often have a preference for one structural system over another—however, they may not be basing their opinion on complete information. For example, a building owner may want to use a wood structure for a six-story building; but IBC will not allow a wood structure taller than five stories. Either way, a collaborative approach should be taken between structural engineers, the owner, designers, and other stakeholders to ensure everyone’s priorities are addressed.
Functional requirements
A building’s use or geographic location may dictate a given structural system. Most notably, buildings located in tornado- or earthquake-prone locations require special engineering and must meet particularly stringent codes. Care should also be taken to identify whether a structure is likely to experience vibration. For example, buildings located near railroad tracks may need to be designed with special considerations if the occupants or equipment within the building are susceptible to vibration.
In extreme cases where a building will experience large amounts of vibration, studies of the structure’s natural vibration characteristics can be done to ensure there is no damage to the building. In rare circumstances, the induced vibration can have the same frequency as the structure’s natural resonant frequency, which can cause harm to the building.
Building structures must be designed as not to excessively deflect, damaging the materials and being noticeable to the occupants. IBC provides limits on floor and roof deflections and allowable lateral drift of a building. Typically, floor deflection is limited to the span in feet divided by 360 (l/360), with a maximum of 25 mm (1 in.) allowed. Roof deflection is the same limit. Lateral drift is typically limited to the building’s height in feet divided by 400 (h/400). In some circumstances, equipment or specialized occupancies will limit the deflection to less than what is typical.
Individual building types frequently have special needs when it comes to structural systems. For example, warehouses often require super-flat floors, to allow the facility’s equipment to properly function. Elevated super-flat floors require the supporting framing to be designed with strict deflection limitations so the floor stays within flatness tolerances when it is loaded. Building structures supporting heavy loads, such as equipment, require careful consideration of the actual equipment loads. Special attention has to be paid to any deflection limitations. It is also important to consider how the equipment will be put into its final location in the building.
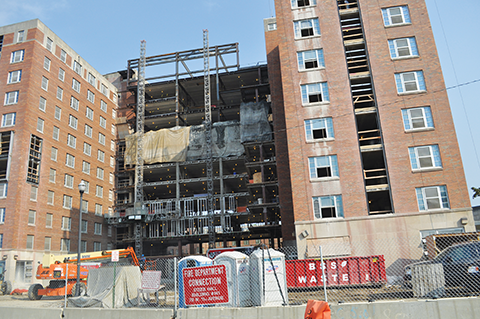
Span and structural depth limitations
A building’s size or space requirements may entail the use of a given structural system. If a building needs large, column-free floor areas, the longer spans between columns results in deeper floor structures. Floor-to-floor height is always a driving force behind structural decisions. Increased heights cost more for materials and result in higher climate control costs over the life of the building, due to the increased volume.
Local zoning codes also place height restrictions on many building types, and a structure classified as a high-rise will have to comply with additional code requirements, involving an increase in cost. Buildings typically requiring low floor-to-floor heights are best framed with concrete two-way slab systems. This system is usually the thinnest structural system available. A conventional concrete beam and slab system will have similar depth to a conventional structural steel system.
Cost
Every building project has a budget, the question is, how generous is it? Some high-end buildings are designed around novel structural systems that showcase the creative possibilities of modern engineering. Some architects may rely on a uniquely sculpted building mass to convey creativity. These designs may require curved structural members, expansive horizontal and vertical interiors, or other complex structural systems integral to the building’s aesthetic. When this is the case, there will most likely be a bigger budget for the structural framing system.
Even for utilitarian buildings, however, the structure may not always be the place to save money. Sometimes investing more in the structural system will save money somewhere else in the project. For example, for one major high-rise, adapting the building’s column layouts in a way that would accommodate less expensive office furnishings was a worthwhile trade-off. Furnishings may seem like a minor expense or an afterthought to structural design, but on the scale of an office building housing hundreds of employees across multiple floors, this type of detail becomes particularly significant.
Typically, the structure costs between 15 and 30 percent of the total construction project. Therefore, if structural system costs increase by 10 percent, this only translates to a 1.5 to three percent rise in the building’s total construction cost.
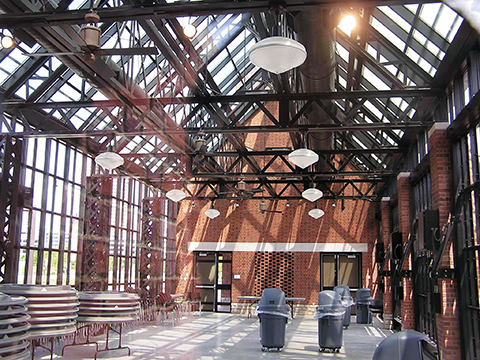
Schedule
As with cost, a project’s schedule can influence what kind of building structure is selected. One factor is the lead times necessary for procuring materials. A structural steel fabrication order may require two to four months to fill, while obtaining the materials to place concrete takes only days. However, for post-tensioned concrete structures, the cables and hardware, as well as the reinforcing steel, can take weeks to obtain. Precast concrete elements require two to four weeks to fabricate, as do wood trusses for wood-frame construction. These schedule constraints should be considered when selecting a system.
A retrofit case study
The aforementioned considerations apply to both new construction and renovation. Some of them, however, become particularly significant during a renovation. On the Ohio State University (OSU) campus, four towers in the university’s South Residential District were combined into two buildings through the construction of 11-story connectors. Each connector addition provides 164 new sleeping accommodations along with group learning and social spaces.
The original towers were constructed in the 1950s. All are based on the same floor plan and are constructed of reinforced concrete frames with brick masonry and limestone cladding. While building code requirements allowed for any Type II A construction (i.e. steel or concrete) in the new additions, the fact each addition had to connect two existing dormitories presented some challenges.
For aesthetic reasons, it was desirable to have the first floor be column-free. The structure also had to fit within the new room module. Perhaps the project’s most challenging aspect had to do with structural depth limitations; the existing dormitories had a floor-to-floor height that was only 2.8 m (9 ft 4 in.)—low by contemporary standards. New construction had to match this height. OSU expressed a slight preference for using concrete framing, as this already existed in the original structures. However, in this case scheduling concerns outweighed the owner’s desire to stick with concrete framing and the design team elected to go with a staggered steel truss system, which uses story-deep structural steel trusses that clear span the width of the building. The floor system uses hollow-core precast concrete spanning between the trusses.
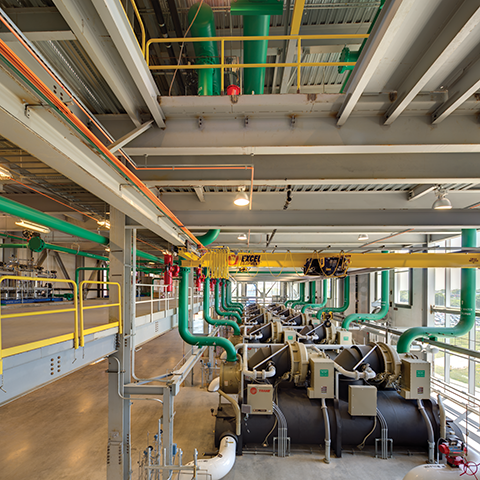
The project’s construction schedule was too aggressive to go with a concrete framing system. OSU planned for the dormitories to be out of service for one school year; even with construction commencing at the beginning of a summer break, this left only 14 months in which to perform the work, so concrete framing for the 11-story additions could not be erected quickly enough to accommodate the timeframe. The advantage of using steel framing and precast concrete was that elements could be fabricated in the spring and arrive onsite as soon as the school year had ended in early June. The actual steel erection began within days after school ended.
Trusses are also space-efficient since they are more shallow than conventional framing. Steel trusses used in the OSU dormitory additions are the same depth, from the top chord to the bottom chord, as the structural depth of the existing buildings. Positioning of the trusses had to be coordinated with the room layout so the trusses would be located between rooms. Additionally, the staggered steel truss system fulfilled the requirement for a column-free first floor space. The truss system clear spans the entire building’s width, requiring columns only at the exterior walls.
Conclusion
While there are many variables influencing the choice of a structural framing system, a systematic approach—taken early in the project’s design—should lead to the selection of a system optimal for any given project. A collaborative approach between stakeholders further ensures everyone’s primary considerations are addressed in the final building design.
Stephen J. Metz, PE, LEED AP, BD+C, is the president/principal at structural engineering firm SMBH Inc. With more than two decades of structural engineering experience, Metz’s office and field experience includes material testing, construction inspection and land surveying, which contributes to his knowledge of the design and construction process. Further, his previous experience with a full-service architectural firm provides him with the skills required to produce well-coordinated construction documents. Metz has a bachelor’s degree in civil and structural engineering from the Ohio State University (OSU). He can be contacted by e-mail at smetz@smbhinc.com.
Regardless of the type of building you are constructing, you need to take note of the type of framework that will be done. The frame is the skeleton of the building and essentially hold everything else up. You would want this to be one of the more important parts of the building. Like you said, you need to pay attention to the building codes so that you follow them exactly and don’t construct something that would be potentially dangerous.
You are right that every building has a budget. Not only do you have to stay within that, but you have to get good materials that will be able to hold the building up. Now for me, I would be sure to get quality materials and if I had to, I’d increase the budget just so I could get them.