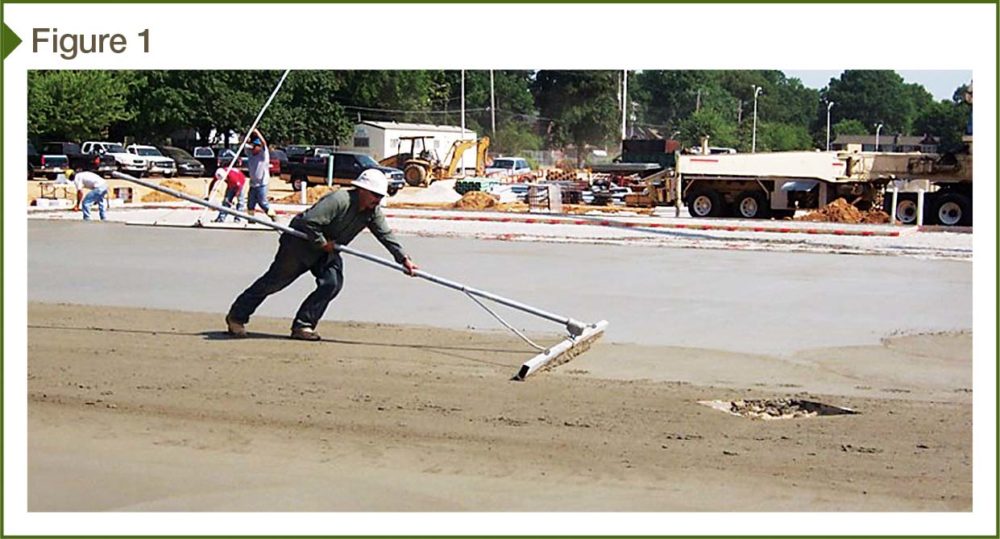
Screed slab surfaces with a vibratory straightedge and strike off to correct elevations.
Rationale: A sufficient amount of paste is needed at the surface for polishing, and this is best accomplished by the use of a vibratory straightedge such as a hand-held vibratory bullfloat, a vibrating screed, a truss screed, or a laser screed. Hand-screeding will not provide enough surface paste.
Do not leave the vibratory screed at any one location while the vibrator is running; move it continuously across the slab.
Rationale: Too much vibration at one location drives the coarse aggregate deeper into the slab. This results in variations in coarse aggregate exposure after polishing. This effect of non-uniform vibration can be due to leaving a vibratory screed running when it is not advancing or, for self-propelled laser-guided screeds, lowering the vibrating head onto the surface before the machine is moving.
Do not use a highway straightedge or bump cutter on the concrete surface during finishing operations.
Rationale: This removes too much paste from high spots, leaving variations in the polished surface (Figure 1). Flatness for polished concrete is best achieved by the use of pan floats.
Finishing
Do not trowel over adjacent hardened concrete surfaces. Inspect trowel machines prior to each pass and remove any accumulated mortar.
Rationale: Troweling over adjacent hardened concrete from previous placements scratches the concrete surface. Some of the worst scratches come from debris falling off an uncleaned trowel machine. These scratches will often be visible on the polished surface.
Machine-trowel the slab edges and as close as possible to walls and columns. Minimize hand-finishing.
Rationale: Machine-troweling and hand-troweling result in differing surface densities, with the former’s surface being denser and harder. Results of the differing densities will be obvious in a polished surface. (Figure 2).

The troweled surface shall be free of trowel marks, burn marks, and mottling.
Rationale: These features affect the uniformity of the final polished appearance. Specifiers sometimes require three trowel passes, believing this will control these effects. However, the number of trowel passes depends on the concrete mix design, weather conditions, and the use of different finishing equipment such as a walk-behind or riding power trowel and the type of blade—steel or plastic. Thus, specifying the number of passes may not achieve the desired result.
The floor flatness (FF) measured in accordance with ASTM E 1155, Standard Test Method for Determining FF Floor Flatness and FL Floor Levelness Numbers, within 72 hours shall be that as shown in Table 1 for the Class of Grind specified for the polished surface.
Rationale: The appearance of the polished surface is dependent on the floor flatness. In addition to measuring floor flatness within 72 hours, the specifier should also require the testing agency measure the flatness when the polishing contractor starts work. If the FF decreases more than 10 percent, the polishing contractor may request a change order because of increased costs needed for extra work. Alternatively, one should consider specifying a FF one step above that specified for a class of grind. For instance, specifying a floor flatness of 50 for the concrete slab, but then choosing a class B grind (FF 40) allows for the decrease in FF with time.
One should specify a FF 50 or above when a laser screed, check rod, highway straightedge/bump cutter, and other floor flatness tools and techniques are available (for 1858-m2 [20,000-sf] placements and above). A FF of 35 or lower should be specified for retail or light commercial, grocery stores with drains and penetrations, or school slabs broken into small placements.
WOW! You guys really put some quality thought into this! I really appreciate the fact that is was designed to be viewed on a monitor with slides and the fact that you included the very rare WHYS!!!
Great article. Out here in Seattle we are using 22%-30% slag cement. How did you arrive at the recommendation for 20% maximum? -David Landrey, CSI, ACI, LEED AP
Please do this for slabs to receive resilient flooring & the inherent issue of ASTM F710 & spray on curing compounds / moisture sealer spray on products. So many spec writers seem to write a ‘belt & suspenders’ approach when doing both just creates a situation where the belt doesn’t warrant the suspenders’ performance and vice-versa.
Great Read, I love concrete Polishing, we just started doing more and more of those these days.
We keep getting scratches in slag mixes.
There are many light colored scratches that require additional cutting to remove
Many of our mixes are 40% slag.
Has anyone had this experience with slag mixes.