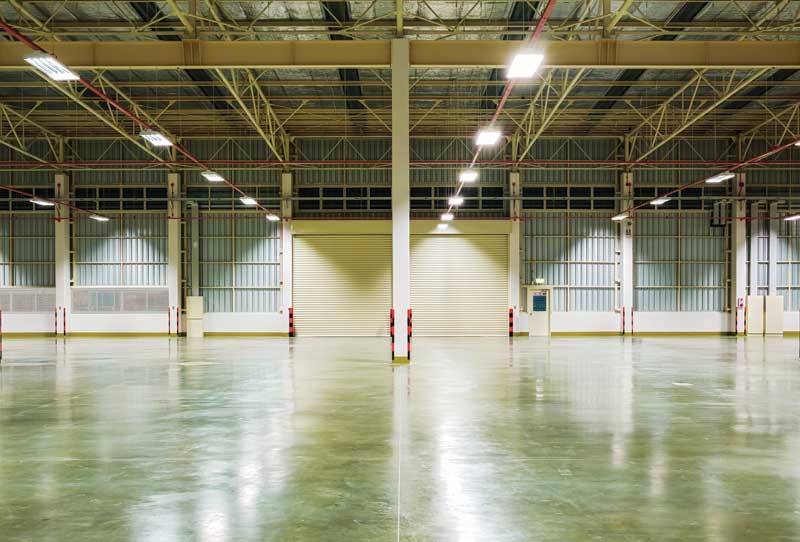
Concrete ingredients
Source limitations for cast-in-place concrete to be polished: Obtain each color, size, type, and variety of concrete material and mixture from a single manufacturer with sufficient resources to provide cast-in-place concrete of consistent quality.
Rationale: Variations in materials used in the cast-in-place concrete slab will affect the variability of the polished surface. This source limitation requirement is similar to that specified for architectural cast-in-place concrete.
Concrete mix design
1. Limit percentage, by weight, of fly ash and slag cement to not more than 20 percent of the total cementitious materials.
2. Prohibit the use of fly ash and slag cement.
Rationale option one: Fly ash particles are highly abrasive, causing increased diamond wear and tooling expense. These materials also limit the amount of available uncombined alkalis needed for chemical reactions with densifiers that aid in polishing. If the floor will be colored with reactive stains, it is also important to have a large amount of alkalis present for the reaction. (See ACI 310, Decorative Concrete). One should determine if option one is feasible during the mockup. Sometimes, the use of fly ash in slag cement is necessary as part of a sustainability effort.
Rationale option two: Both delayed-setting and strength-gain characteristics attributable to the use of fly ash and slag cement create challenges in producing a uniformly finished slab surface, particularly in cooler weather. Some concrete and polishing contractors prefer to use concrete mixes with only portland cement. Some specifications require the use of fly ash or slag cement in the summer to slow setting and eliminate their use in the winter due to the slower setting. This practice should not be allowed for polished concrete as the color variation in these two mixes will be evident.
Concrete properties
The specified compressive strength fc’ is equal to 4000 psi.
Rationale: This is strong enough to polish in a month, but not so strong as to slow polishing progress and increase polishing costs.
Do not allow air content of trowel-finished floors to exceed three percent.
Rationale: Air content greater than three percent increases the risk of blisters and delamination in a troweled finish.
Engineering the concrete slab
F-numbers are used to specify concrete flatness and levelness. These are measured within 72 hours after the completion of finishing operations in accordance with ASTM E 1155 because polishing contractors might perform their work as many as 90 days or more after the concrete was placed.
The engineer must design the concrete slab to retain its flatness and levelness needed for the polishing contractor. For slabs-on-ground, curling lowers the F-numbers as the concrete dries and shrinks. The engineer must provide a design that minimizes the change in F-numbers with time. Alternatively, the specifier could allow for a decrease in FF with time by specifying a level higher for the concrete floor that will be measured within 72 hours.
A team success
The preinstallation conference is the most important part of assembling the team and having everyone become a committed stakeholder in the process. All players, including the specifier, engineer, construction manager, concrete contactor, and polishing contractor, participate in making polished concrete a success.
Polished concrete differs from typical concrete floors and must be treated differently in the specifications and construction. Experienced polished concrete designers and contractors often exceed the specifications recommended here for a specific project. It is highly advisable to utilize such experienced contractors on the team.
Todd Scharich has been an advocate and innovator in the decorative concrete industry for more than 20 years. In 2012 he was appointed as Decorative Specialist for the American Society of Concrete Contractors (ASCC). He can be reached at tscharich@ascconline.org.
Chad Gill, PE, is a concrete polishing and staining contractor and is the president of the Concrete Polishing Association of America (CPAA). He can be contacted at chad@thisisconcrete.com.
Steve Lloyd is CEO of Lloyd Concrete and has been in the industry more than 40 years. His knowledge of finishing has earned him the Golden Trowel Award. He can be contacted at stevelloyd@lloydconcrete.com.
Pat Harrison is a vice president and principal with Structural Services Inc., with 33 years of concrete slab design, construction, and forensic experience. He can be contacted via e-mail at pharrison@ssiteam.com.
Bruce Suprenant, PE, PhD, FACI, is the technical director for the ASCC and a Fellow of American Concrete Institute (ACI). He can be reached at bsuprenant@ascconline.org.
WOW! You guys really put some quality thought into this! I really appreciate the fact that is was designed to be viewed on a monitor with slides and the fact that you included the very rare WHYS!!!
Great article. Out here in Seattle we are using 22%-30% slag cement. How did you arrive at the recommendation for 20% maximum? -David Landrey, CSI, ACI, LEED AP
Please do this for slabs to receive resilient flooring & the inherent issue of ASTM F710 & spray on curing compounds / moisture sealer spray on products. So many spec writers seem to write a ‘belt & suspenders’ approach when doing both just creates a situation where the belt doesn’t warrant the suspenders’ performance and vice-versa.
Great Read, I love concrete Polishing, we just started doing more and more of those these days.
We keep getting scratches in slag mixes.
There are many light colored scratches that require additional cutting to remove
Many of our mixes are 40% slag.
Has anyone had this experience with slag mixes.