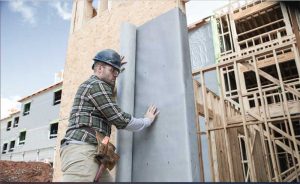
Asphalt felt paper
Asphalt felt paper is an absorbent material made from a base of natural (wood) or synthetic (fiberglass) materials and an asphalt coating that can be used as a secondary layer of protection against moisture intrusion. The two most common types of asphalt felt are 15# and 30#. Ranging from 5 perms when dry to nearly 60 perms when wet, felt will absorb water in humid conditions and dry to the exterior. However, there are several downsides to using felt paper. First and foremost, felt paper must be handled with extreme care to avoid tearing or ripping the delicate material. Tears and rips minimize the performance capabilities of WRBs by allowing water to build up in the wall system. Additionally, asphalt felt paper is prone to UV degradation from extended sunlight exposure. This exposure weakens the material, thereby compromising its durability. When combines with long-term heat aging, UV degradation can reduce the integrity of asphalt felt paper.
Impregnated sheathing
Impregnated sheathing is a relatively new weather barrier material composed of oriented strand board (OSB) wood structural sheathing panels that have an integrated WRB layer. These panels are typically fastened together with seam tape. The sealing tape is a polyolefin sheet with an acrylic adhesive backing. While speed of installation and wind resistance are benefits of these materials, there are several setbacks associated with using impregnated sheathing as a WRB. For example, swelling along edges and corners is a well-cited issue among contractors. Swelling creates complications for taping and can instigate pathways for air and water to enter the wall assembly. Careful attention during installation is also important with impregnated sheathing, since overdriven fasteners can open the system up for water penetration.
Furring strips
Before integrated drainage gaps were woven into the building wrap, contractors used furring strips as a capillary break to separate the wrap from the structural sheathing and framing. Today, wooden, metal, or plastic furring strips can be used to create a true plane on which to attach flat surface materials. The gap created by the strips allows water to flow down with gravity and drain out of the building envelope.
Rainscreens
One method for achieving bulk water drainage is attaching a rainscreen material to the building wrap. These products eliminate the cost and time-consuming labor of installing furring strips by creating a gap between the sheathing and the cladding, which facilitates both drainage and continuous airflow. Where wood strapping only vents approximately 85 percent of the wall, building wraps with an integrated rainscreen provide a continuous vented airspace over the entire surface area of the wall, providing greater drainage and more effective drying. Since many rainscreen products use a matrix of plastic material to achieve the gap, they are not subject to saturation and decomposition that could compromise wood furring.
Rainscreen products are recommended in areas with wind-driven rain, heavy rainfall (1016 to 1524 mm [40 to 60 in.] annually), or high temperature and humidity. Coastal areas and hilltops are suitable for this technology. In these situations, the importance of creating a drainage plane is heightened when using an absorptive cladding material like wood or fiber cement.
Other considerations
As a general rule, the Building Enclosure Moisture Management Institute (BEMMI) recommends any area receiving more than 508 mm (20 in.) of annual rainfall should incorporate enhanced drainage techniques in the wall system, especially if using an absorptive cladding material. Areas receiving more than 1016 mm of rain should utilize rainscreen design regardless of cladding material. The geographic orientation of the wall, amount of overhang, altitude, and even nearby trees can have an impact on the expected amount of water intrusion and how likely drying is.
Some states have added prescriptive measures to their codes that include the use of drainage planes, and others are expected to follow. Oregon, for example, requires the building envelope to consist of an exterior veneer, a WRB, a minimum 3-mm (1/8-in.) space between the WRB and the exterior veneer, and integrated flashings. The envelope must offer proper integration of flashings with the water-resistive barrier, the provided space, and exterior veneer. In lieu of providing the 3-mm space between the exterior veneer and WRB, builders can install the exterior veneer over a WRB that is manufactured to enhance drainage and meets the 75 percent drainage efficiency requirement of ASTM E2273 or other recognized national standards.
These considerations are driving the adoption of new WRB solutions that meet both bulk water blockage and drainage needs, thus satisfying the requirements for today’s high-performing wall systems.
Impact of siding selection
While there are many exterior cladding options on the market today, none of them are impervious to the effects of water penetration. Installing a water repellant material behind the cladding might be common sense, but knowing which type of WRB pairs best with which cladding is a little less obvious. There is a right and a wrong way to combine WRBs and claddings, and builders need to know each cladding material comes with a unique set of installation best practices for managing excess moisture.
For example, when installing vinyl siding, which has built-in drainage holes and fits loosely on the wall, an ordinary smooth-faced building wrap should provide adequate drainage. However, tightly fastened cladding, such as cedar siding or fiber cement board, might allow the water trapped between the siding and a smooth building wrap to pool. This could eventually make its way through the building wrap and into the framing. These are cases where a drainable building wrap would provide significant benefit.
Reservoir claddings such as brick, stucco, and stone present another set of issues. Since these materials hold water, once they get wet, the stored water can migrate elsewhere and cause problems. In these applications, it is imperative to separate the cladding from the rest of the assembly with a capillary break, which can be an airspace or a material that sheds water or does not absorb or pass moisture.
Also, certain cladding materials such as wood and stucco often contain chemicals called surfactants (or surface-active agents) that can affect the water resistance of WRBs. These chemicals, which are also present in solutions used to power-wash siding, reduce the surface tension of water, easing its ability to pass through microscopic openings in the membrane. So, if the WRB will be exposed to surfactants, it is advisable to choose a product that has added protection against their harmful effects.
One type of cladding gaining considerable attention is fiber-cement board. Strong, easy-to-install, and less expensive than wood cladding, fiber-cement board is an attractive option because it does not require any maintenance. The material is both fire- and insect-resistive and can even increase the building’s energy efficiency as part of a tight building envelope. On the flip side, since fiber-cement board is a tightly fastened cladding, it might allow water to get trapped between the siding and a smooth WRB. The water could eventually make its way through the wrap and into the framing.
Defending the structural integrity of a building is no easy feat, but with the right moisture management strategies, it is an attainable task. When looking at factors like durability and performance on the jobsite, weather-resistant barriers are an easy answer to many of the construction and comfort concerns presented by Mother Nature.