
by Steve Taylor
Specifiers typically select grout for tile projects based on general performance characteristics, color, warranty, and cost. However, less-than-optimal products are often used. Some design professionals are unaware of the changes in technology, not realizing all grout is not the same. Color and aesthetics are only one small factor in the product’s overall performance.
Specifiers and designers should evaluate each ceramic and natural stone tile project and base the grout decision on the function as well as appearance of the space to be tiled. Some grout perform well in certain situations, while others will fail when not specified correctly.
Before selecting a grout, some questions to consider about the area and installation are:
- Is it a lightly trafficked office foyer or a mall food court installation, with heavy traffic and exposure to a tough cleaning regimen?
- Is the tile project likely to be soiled with foods (i.e. from commercial kitchens or food-processing) that can stain the grout? What about caustic materials (i.e. acids or alkalis) from factories that will deteriorate standard grouts, or harsh cleaning chemicals that may damage the grout?
- How soon will the tiled area be opened to service and traffic?
- Is this a remodel that must be returned to service the next day?
Further, there are many colors from which to choose and, therefore, many choices of grout based on different chemical technologies to address these concerns and help achieve a durable and aesthetically pleasing tile installation.
Grout background
An understanding of grout is necessary to make educated choices. Traditionally, grout was based on the same technology as bonding mortar—portland cement and sand. Installers were accustomed to using sand and portland cement blends for installing tile and filling joints between tiles. Today, these cement-based tile grouts are divided into two categories: standard cement grout and high-performance.
Standard cement grout for tile installation
This type of grout meets the requirements of American National Standards Institute (ANSI) A118.6, Specifications for Standard Cement Grouts for Tile Installation, which establishes the performance of basic polymer-modified and non-modified portland cement grouts. These grouts can contain sand for filling joints greater than 3.17 mm (1/8 in.) or be non-sanded for joints that are less than 3.17 mm wide. ANSI A118.6 establishes minimum performance levels for compressive strength, flexural strength, shrinkage, and water absorption. These have been commonly used in the industry for 50 years.
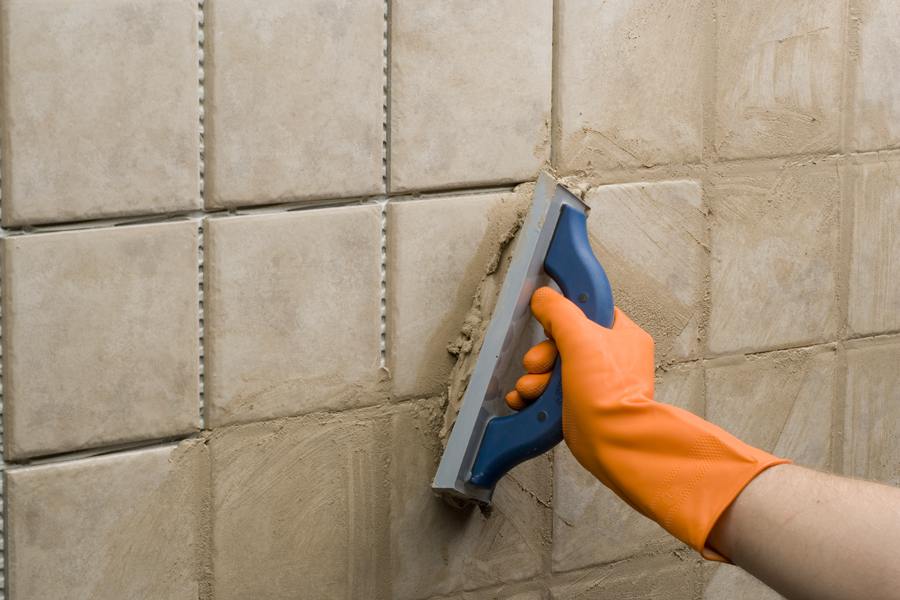
High-performance cement grout for tile installation
Meeting the performance requirements of ANSI A118.7, Specifications for High-performance Cement Grouts for Tile Installation, a grout is generally polymer-modified to reduce water absorption from 10 percent (i.e. standard grout) to less than five percent. This is important, since staining of the grout is more likely with more absorbent material. Tensile and flexural strength are both increased in these grouts. This results in higher durability. As these high-performance grouts are highly modified, it allows the manufacturer to add other benefits such as quicker curing, reduced shading, and efflorescence control.
The advent of high-performance cement grout with modern technology has eliminated many of the concerns installers have with the standard cement grout. In many cases, these high-performance grouts are necessary to complement advances in ceramic tile technology.
It is generally accepted by the ceramic tile industry the lifecycle of a ceramic tile installation is 60 years. High-performance cement grout has high strength and a hard finish like the surrounding tile. When these installations are properly sealed and maintained, they will hold up for the life of the tile installation. However, if they are not properly maintained and cleaned, acids from contaminants and cleaning agents will break down the grout’s portland cement component and weaken its internal structure. After a few years, the affected grout in the joints will sufficiently degrade and have to be replaced. This problem with cement-based grouts led to the development of chemical-resistant grouts.
Chemical-resistant grouts
The first chemical-resistant grouts were based on epoxy resin because it could be easily mixed at the jobsite and cure at the same rate as the traditional cement-based grout. Epoxy resists many chemicals, such as solvents and strong acids, and can be easily pigmented in factories to produce an array of colors. Factory-controlled coloring of the epoxy allowed manufacturers to produce a more consistent batch-to-batch appearance.
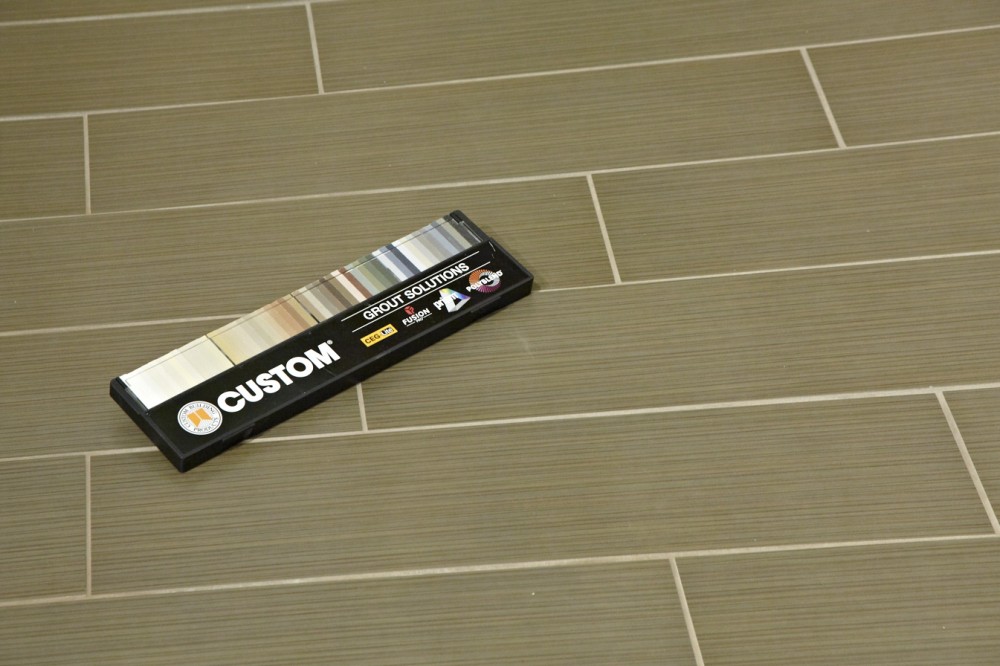
The curing of portland cement based grout relies on the hydration of the portland cement to build strength. The amount of hydration also affects the color/shade of the grout. Fully hydrated portland cement grouts tend to be lighter in color than the partially hydrated cement. If the grout is not uniformly hydrated, it will show shading (i.e. light and dark areas) across the tile installation. Higher performance grouts have been developed to address shading. The curing of the epoxy does not affect the color, so the appearance throughout the installation remains uniform throughout the curing process.
Standards were developed to classify the epoxy resin-based grouts into two categories: chemical-resistant, water-cleanable tile-setting and grouting epoxy, and modified epoxy emulsion mortar/grout.
Chemical resistant, water cleanable tile-setting and grouting epoxy meeting the requirements of ANSI A118.3, Specifications for Chemical-resistant, Water-cleanable Tile-setting and Grouting Epoxy and Water-cleanable Tile-setting Epoxy Adhesive, was established as a minimum performance requirement for water-washable 100 percent solids epoxy grout.
Modified epoxy emulsion mortar/grout with performance meeting ANSI A118.8, Specifications for Modified Epoxy Emulsion Mortar/Grout, is available for addition to standard cement grout. The modified epoxy emulsion grout was developed to be mixed with traditional cement-based grout in place of water. While this improved the strength and stain resistance of the standard cement grout, it did not completely eliminate its chemical sensitivity. Today, this grout type is not commonly found for sale.
Replacing the portland cement binder with epoxy resin made the original ANSI A118.3 epoxy grouts hard to install and spread across the face of the tile. Installers found it difficult to clean during the installation. This resulted in additional labor cost and a less-than-acceptable looking tile installation.
Over the years, there have been many advances in the chemistry of epoxy resins. Manufacturers of epoxy grouts have taken advantage of these chemical breakthroughs and develop 100 percent solid epoxy grouts meeting the requirements of ANSI A118.3.
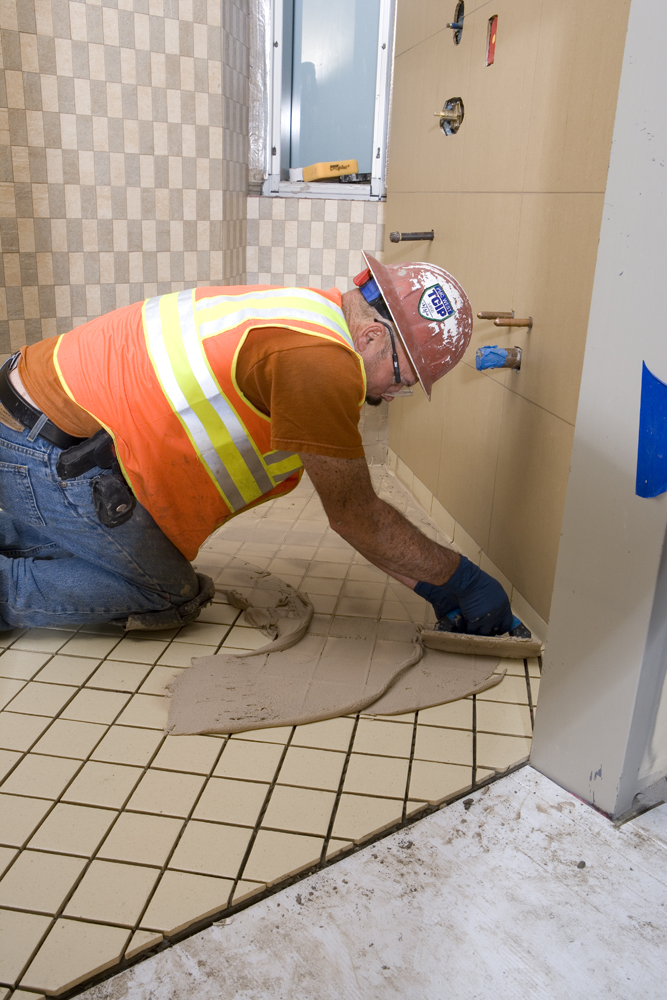
These grouts were formulated for easy spreading and filling of the joints in tile assemblies. They contain non-sag and non-slump properties, allowing installers to fully fill joints on both horizontal and vertical surfaces. Further, they are designed to clean off the tile’s surface during installation. They are also chemical-resistant and suitable for commercial installation. While epoxy grout fills the need for chemical resistance in most installations, some industrial applications need even greater resistance to harsh chemicals.
The need for even more chemical- and heat-resistant materials in industrial applications resulted in the development of less-common furan resin-based grout. Chemical-resistant furan mortars and grouts meet the performance characteristics of ANSI A118.5, Specifications for Chemical Resistant Furan Mortars and Grouts for Tile Installation, unfortunately, when these grouts are installed they cannot be removed from the face of the tile with ordinary water. The installer must use solvents, like alcohol, to remove excessive grout form the face of the tile and his tools.
Installation of furan resin grout requires special techniques, including the coating of the tile with wax. Besides having extremely good chemical resistance, furan resin is known to produce a high bond to ceramic surfaces. To prevent permanently bonding to the face of tile, the tile face must be coated with wax that has to be removed once the grout is fully cured. Due to the difficulty in installation, furan-based grouts are used in areas demanding the highest resistance to chemicals (i.e. battery manufacturer that use strong acids).
Manufacturers of maintenance cleaners continue to improve products, making them more effective and easier to use. The latest developments in cleaners include agents to help break down the common greases that end up on floors of commercial kitchens caused by deep fryers. When these greases break down by the action of the cleaner, they convert an organic acid (i.e. fatty acid) detrimental to the grout and should be removed from the surface. These acids are aggressive on cement grouts and normal epoxy grouts; if left in contact with the grout for extended periods, they will begin to break down the epoxy resin in the grout.
Furan grout has a higher chemical resistance to the organic acids and would be a good choice for commercial kitchens. However, the expense and difficulty in installation make them less attractive to the installer. Recently grout manufacturers have developed improved 100 percent solids epoxy grouts meeting the performance of an ANSI A118.5. These grouts are easier to install, with the same characteristics of an ANSI A118.3 epoxy grout, but have higher chemical and temperature resistance. They will hold up to the latest commercial cleaners for 15 to 20 years in commercial kitchens. While these epoxy grouts do have an industry standard, they are labeled by their manufacturer as industrial-grade epoxy grout meeting the performance of ANSI A118.3 and A118.5.
The latest development in grout for the installation of ceramic and natural stone tile is single-component, ready-to-use, and premixed. These grouts are water-based and use polyurethane, acrylic polymer, and/or silicone resin for the binder, in place of portland cement or epoxy. Industry standards have not yet been developed for these grouts, so there are many performance differences between them. It is important to confirm with the manufacturer this type of grout is suitable for the particular installation; some are suitable for wet areas and others are not.
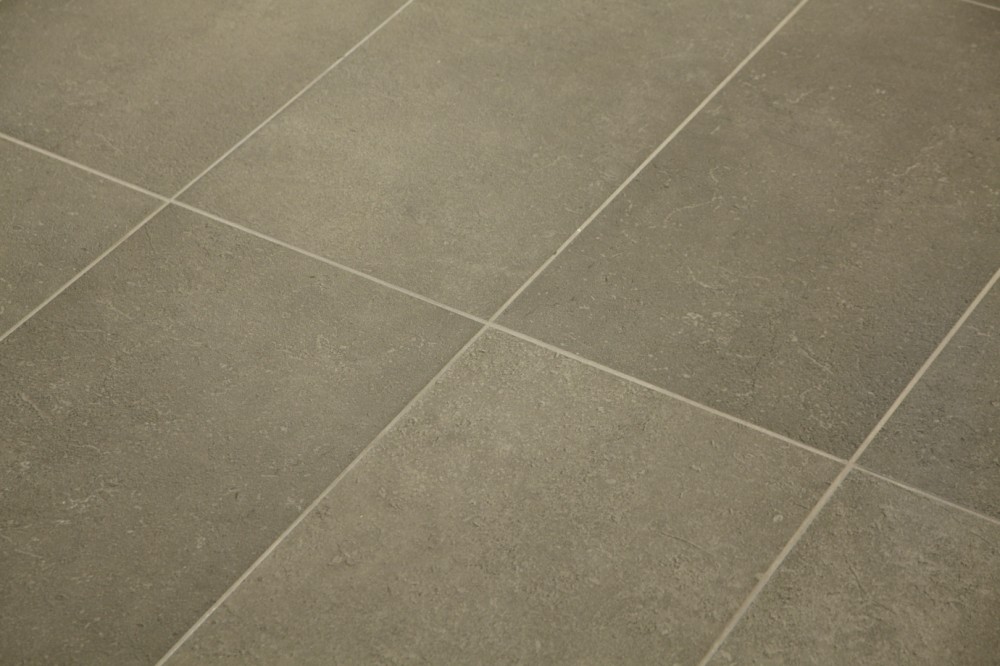
The most recent developments produced grouts with many of the desirable properties of portland cement grout and 100 percent epoxy grout. They are easy to install, cure rapidly, and have chemical resistance of an epoxy grout. Some are the most stain-resistant grouts on the market and never have to be sealed to prevent being stained.
Conclusion
There are many choices in finishes for the architect, specifier, and designer to choose from. When it comes to selection of ceramic tile one should not overlook the grout. It is important to select a color of grout that complements and works with the project; it is equally important to select the right type of grout to meet the function of the tiled area. The majority of the projects will only require a standard or high-performance cement grout.
Today, there are a growing number of areas, like commercial kitchens, where ceramic tile is used and would greatly benefit from an industrial grade of epoxy. One should not overlook the up-and-coming single-component grout in many installations. The various types of grout available have been discussed, and it should be easy to specify the right type with the correct ANSI standard identification. Many suppliers have grouts performing above the standards—in these cases, it is important to specify a performance level in addition to the minimum ANSI standard. Following these guidelines helps ensure a long-lasting, attractive ceramic tile installation.
Steve Taylor is director of architecture and technical marketing for Custom Building Products. He has more than 30 years of experience developing products for the construction industry. A member of Tile Council of North America (TCNA) and Materials & Methods Standards Association (MMSA), he helps determine proper tile installation methods and standards. Taylor can be reached by e-mail at stevet@cbpmail.net.
Steve Taylor, what kind of grout would you recommend for a hearth pad? Is grout heat resistant or do I need something special?
Thanks, Rob