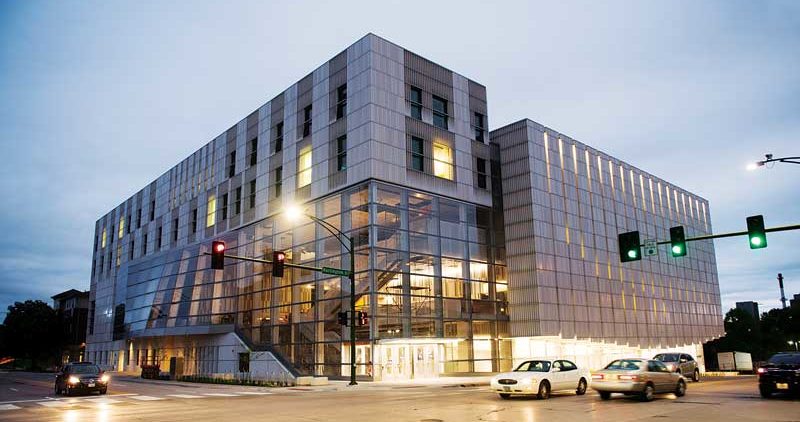
by Tammy Schroeder
Aluminum offers a wide range of properties and characteristics engineered to the demands of specific applications through choices of alloy, temper, and fabrication processes. When aluminum is anodized, it results in an extremely hard and durable surface finish. In fact, the anodized layer is second only to diamond in hardness. Along with its metallic appearance, 100 percent recyclability, excellent corrosion resistance, and minimal maintenance requirements, this makes it an excellent option for architectural building products PLACED in high-traffic areas such as storefronts, doors and entranceways, curtain walls abutting offices, and handrails.
Anodize coatings are created through an electrochemical process where the aluminum on the surface of a part is converted to aluminum oxide. The coating becomes integral to the part on which it forms. Therefore, the aluminum to be anodized has a significant impact on the finish. The aluminum alloy and temper, as well as the anodizing process, have profound effects on the success of achieving a superior, sustainable, visually appealing anodize finish.
Aluminum alloys and their alloying elements
Pure aluminum is soft, light, corrosion-resistant, and highly conductive for electricity. Other constituents—such as silicon, copper, magnesium, manganese, chromium, and zinc—are added to aluminum to further enrich its properties (Figure 1). Predominantly, these additives can increase the material’s strength, workability, and response to finishing. Iron is also typically present as a contaminant, but it is desirable in very small quantities (as discussed later in this article).
Aluminum alloys, with their alloy constituents, can have a large effect on anodizing. The only component of an aluminum alloy that anodizes is the aluminum—all other components, elements, and impurities do not.
The 6xxx series are the alloys most commonly recommended and used in architectural and structural applications. They contain small amounts of magnesium and silicon as the principal alloying elements. The most frequently specified alloys, 6061 and 6063, contain no less than 95.8 percent aluminum. The total amount of other elements is less than five percent of the alloy composition. Impurities, such as iron, are also present, but their total percentage is usually less than 0.35 percent.
Anodizing is very dependent on the alloying elements. A slight variance in the aluminum’s composition can have profound impact on the finished appearance. Various combinations of constituent elements cause each aluminum alloy to react differently to the process of anodizing, through either surface chemistry or electrical conductivity. As a result, each alloy or series yields a different appearance, even if treated with an identical anodizing process.
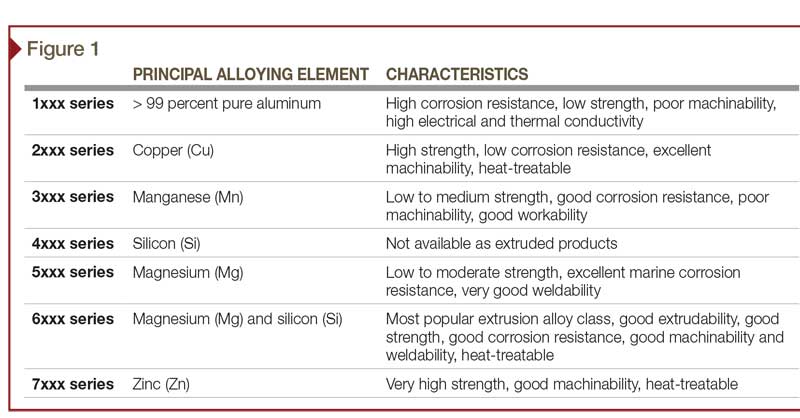