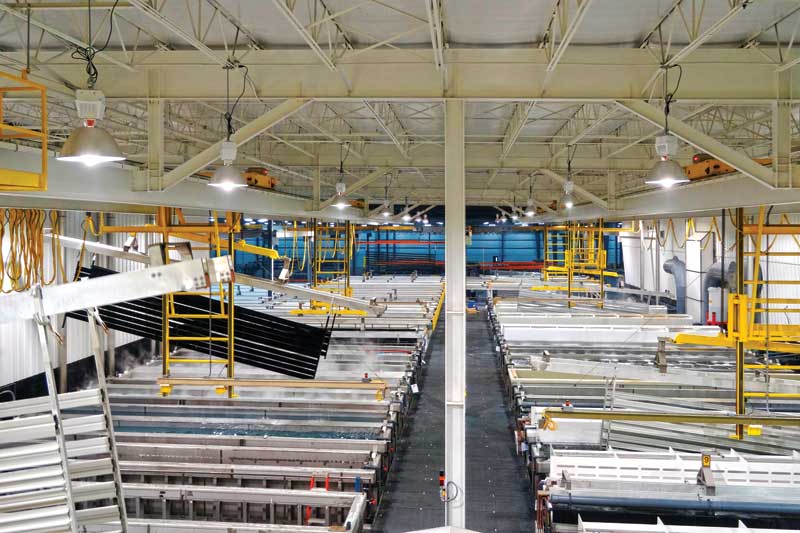
Photos courtesy Linetec
Mixing aluminum alloys means mixed results
An aluminum alloy is a chemical composition where other chemical elements are added to pure aluminum to enhance its properties and increase its strength. The finished extrusion’s characteristics are partly determined by the alloy’s composition. Each designation has a predetermined mixture of one or more elements together with the aluminum; they are typically added in amounts ranging from 0.05 to seven percent.
The alloy composition and the method of production have a substantial effect on the aluminum’s performance and its post-anodized appearance. The production method has an impact on the alloy’s final temper, which is attained through numerous forms of mechanical and thermal treatments such as the extrusion process, heat-treating, and quenching (i.e. manipulating properties through heating the metal and controlling the rate of cooling).
Whenever possible, extrusions from the same lot and temper should be used. There can be slight variances in the alloying elements and impurities between lots, which can affect the anodized finish. If it is not possible to use the same lot throughout the entire project, one should ensure the same lot of material is used per elevation. This is particularly important when working with sheet material such as 5005 alloy.
Aluminum temper
The word ‘temper’ refers to the combination of hardness and strength imparted to aluminum by mechanical or thermal treatments (Figure 2). Aluminum alloys are offered in a wide range of tempers. Those classified as ‘heat-treatable’ gain strength through the addition of heat. On the other hand, alloys classified as ‘nonheat-treatable’ develop maximum strength characteristics through cold-work hardening after extruding. This involves shaping the work piece at a temperature below its recrystallization temperature, usually at ambient temperature. In most cases, such cold-forming is done at room temperature.
Heat-treatable alloys, including the 6xxx series, attain their maximum strength through controlled heat treatment. They have the highest strength of aluminum alloys. The temper level of an aluminum extrusion has an impact on the anodizing process outcome because it affects the gloss and clarity. Typically, the higher the temper is, the higher the finish clarity will be. Temper also has an effect on the alloy’s surface chemistry, which can have an effect on the anodize color. To minimize variance in the anodize process, a project’s extrusions should be the same temper.
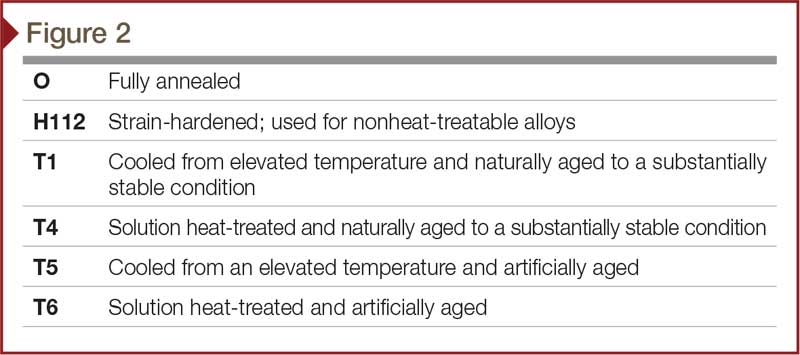
Primary versus secondary aluminum
Aluminum recovered from scrap (i.e. secondary aluminum) has been an important contribution to the metal supply since the 1950s. Economic implications and increased concern regarding the energy supply have focused even more attention on recycling of aluminum because of its energy-intensive nature. However, recycled aluminum can have higher concentrations of impurity elements, contaminants, and other metal constituents such as iron.
Iron is the most common impurity found in aluminum. Higher concentration of iron in the aluminum can cause excessive die wear and surface defects in the anodizing. However, too low of an iron concentration can cause a higher gloss on the anodized surface. Testing has shown an iron content of 0.15 to 0.2 percent provides the best response to the etch process. Secondary billet tends to have a higher concentration of iron.
An anodize finish on pure aluminum would be continuous and transparent, evenly transmitting light through the thin oxide coating. The contaminants and non-aluminum metals within the alloy of the aluminum extrusion can give clear anodize a darker finish. These areas contain particles of constituents and oxidation products detracting from the coating’s transparency. This indicates how important—or rather, detrimental—impurities are to the result.
The greatest complexity with secondary aluminum is the inconsistency in the alloy, as each lot can be significantly different. The impurities of secondary billet are higher, but still must be within the contaminant and element specification tolerance.