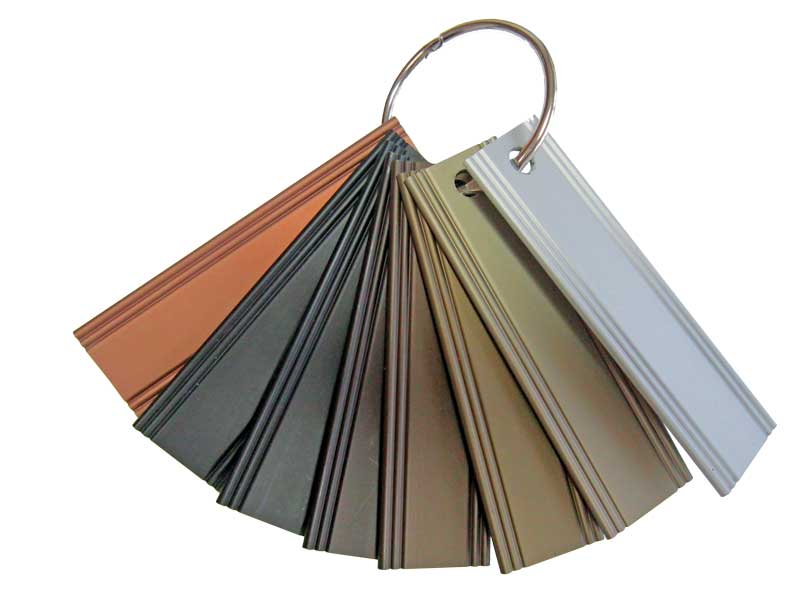
Chemistry of the anodize process
To produce a clear anodize finish, aluminum parts must go through a minimum of 12 process tanks. If colored anodize is needed, two additional tanks are required. Temperature, bath time, and chemical concentration of each tank must be tightly controlled in order to maintain a consistent process and finish. Automation of the anodizing process (and of each tank’s chemistry) is the best way to perform this.
The pre-anodizing steps of cleaning, etching, and deoxidation (or desmut) are intended to yield as much oxide-free aluminum as possible, as well as result in a uniformly conductive distribution at the surface for anodizing. Rinsing is imperative between process steps to keep contaminants out of subsequent process tanks.
Focus on the etch
The etching temperature, time, chemical concentration, and dissolved aluminum concentration are the most important etching process parameters influencing surface uniformity. The etching process’ goal is to produce an appearance that is homogeneously matte and consistent.
During anodizing, an electrochemical reaction converts aluminum into a porous aluminum oxide film. This transparent-to-translucent layer is several times thicker than the naturally occurring oxide. Light is scattered, refracted, and reflected differently from this film depending on the compositional variations, incorporated particles, and microscopic roughness of the aluminum’s substrate surface. However, during the alkaline etching process prior to anodizing, further surface roughness is also generated due to uneven chemical attack on the microstructure. The additional surface roughness created on the extrusion surfaces is due to different reaction rates between the alloy’s impurities or constituents and the aluminum substrate.
It is critical to control the etch bath parameters to decrease the intensity of, or even prevent, the occurrence of surface streaks. The final appearance usually depends on a good etch. An acid etch bath with fluorides produces a more matte finish—hence a more uniform finish—than a caustic etch.
Anodizers have varying control over their tank chemistry, tank temperatures, solution concentrations, and the time material spends in each tank. However, they have no control over the alloy, temper, or shape of the aluminum parts. These variables can make it extremely difficult to achieve an exact color from run to run and load to load. Working with a company whose processes are automated, with tight process controls, can greatly reduce these variables’ impacts.
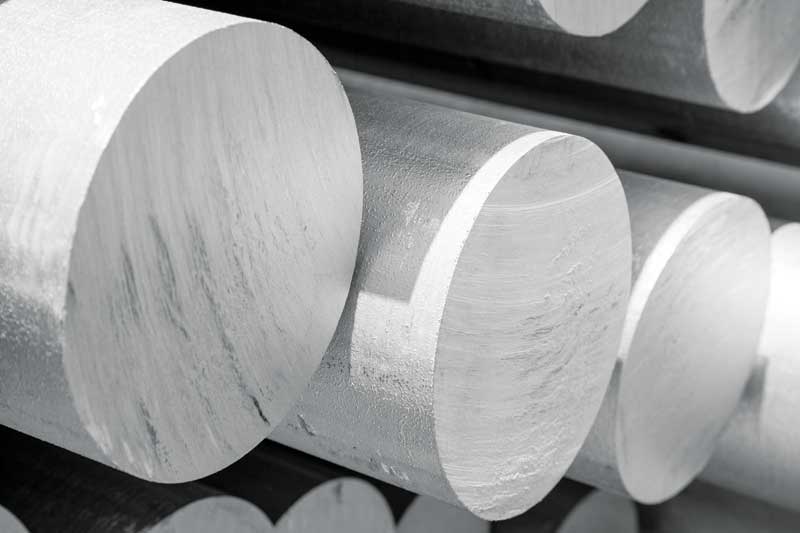
Surface preparations
Defects to the surface of an anodized substrate can be introduced by various unrelated processes such as machining, sanding, or welding, or by residues from previous processes. Shot-peening, grit-blasting, or mechanical finishing techniques may leave residue on the substrate that can also introduce interfacial contamination and obstruct anodic oxide formation during the anodizing process. Laps, seams, and burrs created on the surface by these processes have distinct charge distribution effects on the substrate.
Anodizing can have an unpleasant effect on welds. When two or more parts are welded together, acid can be entrapped in the weld and in the area around the weld. Further, the heat developed from the welding process changes the metallurgy of nearby metal or heat-affected zones (HAZs), causing localized discoloration after anodizing—this is often referred to as a ‘halo’ or ‘ghost’ effect. The area around the weldment can be slightly lighter or darker in color, causing the welded area to appear larger than it is.
The most extreme finish variations exist when a welding rod alloy vastly differs from the alloy used to make the part. The proper 5356 alloy welding wire and the lowest heat possible should be employed when welding 6xxx series alloys. The worst choice is 4043 because it turns smutty black when anodized.
Some extrusion surface defects, such as pick-up and die lines, may not be completely removed from the etched surface, and their remnants become a part of the surface imperfections. For best anodizing results, there are a few other considerations to keep in mind.