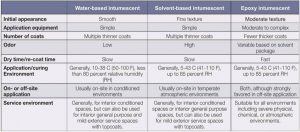
In addition, the description of a “decorative finish” in the second paragraph of the ASFP guidance document is largely subjective and may lead to dispute on cost impact and remedial work to achieve a “good standard of cosmetic finish.” The standard would also rely on the bespoke finish for all critical items in close view (AESS categories 3 and 4). Commercially, this is an issue for hard bid work, as the concept of a bespoke finish agreed in the field lends itself more to design build arrangements due to its inherent ambiguity. A contractor may have an issue providing an effective bid for an item for which its level of effort would likely be determined post-award.
In the absence of an objective, industry-accepted standard, coatings manufacturers, applicators, architects, and building owners continue to struggle with all the basic characteristics—material selection, application and finishing procedures, appearance standards, and more. Further, with no allegiance to a single standard, there remains considerable room for subjectivity, bias, and costly disagreement over the finish quality of coated AESS members. Ideally, an appearance standard for IFRM coatings would be built to align with the AISC’s AESS categories and their specific surface quality requirements.
IFRM materials, formulation, application, and finishing criteria
Any workable global IFRM finish standard for AESS must address the three generic types of IFRM coating materials: water-based acrylic, solvent-based acrylic, and plural-component intumescent materials. The comparisons found in Table 1 and 2 highlight key features of these material types and suggest how material capability, formulation, application, dry time, and service environment influence material selection and finish. In general:
- Both water- and solvent-based acrylic intumescent systems are applied in thinner coats than epoxies—typically 30- to 60-mil dry film thickness (DFT)—making them likely to self-level into smoother finishes. In addition, their lower viscosity enables the use of finer spray tips, resulting in better atomization and a more aesthetic finish. Acrylic intumescent materials are typically well suited for interior, general-purpose, and conditioned spaces. These materials may also be used on some exteriors with the help of a topcoat to protect the fire protection coating from atmospheric degradation.
- Epoxy intumescent materials are applied in thicker films, typically around 100-mil DFT or more, but their thixotropic nature makes for a more textured or “orange-peeled” finish. Epoxies provide the best overall long-term performance, especially in corrosive, physically demanding, or severe exterior environments, giving them a substantial life-cycle cost advantage over acrylics in these applications. They also lend themselves to off-site application, making them ideal for new construction projects, particularly for AESS-2 designs.
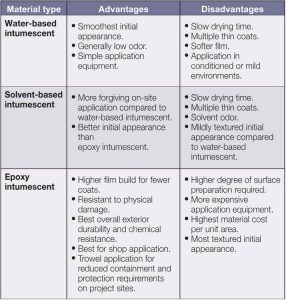
While performance requirements and material composition are strong influencers on IFRM coating finishes, three other issues can also play a vital role in the finish quality of IFRMs, including: product formulation, application techniques, and secondary shaping, such as sanding and using rasps. The level of finishing, such as troweling and finish rolling, affect the finish quality as well, along with DFT requirements, as coatings with higher DFTs tend to be rougher and or wavy in appearance.