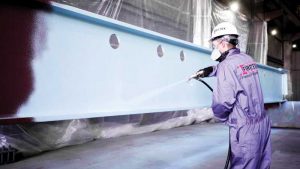
Formulation
Finish-related factors in formulation include variables such as fiber content and length, pigment selection and concentration, and the use of thixotropic thickeners or other additives essential for fire-retardance, film build, or other properties. Often, IFRM formulations will need to strike a balance between aesthetics and performance.
More viscous materials will apply in thicker film layers and therefore require fewer application steps, but those films may be more textured in appearance. These high-solids epoxy formulations feature diluents that react and are retained within the final cured coating, allowing for thicker builds. Conversely, acrylics must be applied in multiple thinner coats to allow for diluent evaporation.
Fiber selection and content can also have a significant impact on final appearance. For example, long-strand fibers can improve the strength of the char in a fire test and extend the coating’s insulating time at lower film thicknesses. However, the added fiber content creates texture in the finish, forcing building specifiers to trade the improved performance for some reduced aesthetic appeal.
The key takeaway here is, formulation that may be necessary for performance, may be detrimental for appearance. Oftentimes, it is critical to understand this, as functionally higher performing materials may prove more difficult when achieving the desired performance.
Application
Methods for applying IFRMs include spraying, brushing, rolling (typically for touching up small areas only), or troweling, with the final appearance
of the coating dependent on both, the material’s characteristics, and the skill of the applicator.
Spray applications generally provide the best initial appearance, though the quality of the finish can vary based on the type of equipment used, the film thickness applied, the amount of solvent reduction, spray pressure, and the spray distance to the substrate (Figure 3). Key equipment considerations include using the proper hose diameter, spray gun, and tip size, all of which can affect material flow, atomization, and final appearance.