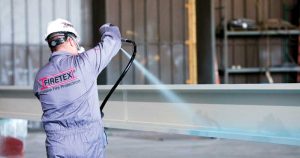
Both material and surface temperature are also critical application factors. Materials applied at higher temperatures or to warmer substrates generally build lower films and flow slightly better for a smoother finish due to the higher temperatures mildly reducing the coatings’ viscosity. However, too high temperature may result in accelerated “tacking up” of the coating, which will not allow it to level out. Conversely, at lower temperatures, applicators can increase film builds, but the film appearance may be slightly rougher. The material flow is also reduced at lower application temperatures, reducing efficiency.
Applicator spray distance from the target is a third critical factor; it requires a balance between film texture, which improves at greater spray distances, and film waste, which also increases with distance. Further, an applicator who is too close to a target can “push” material with the force of the spray stream and create wavy patterns in the final film. An applicator who is too far from the surface or applies coatings at an acute angle can leave a splattered finish, leading to excessive waste.
Secondary procedures
To improve the shape and finish of applied coatings, applicators may perform secondary procedures, such as trowel finishing, finish rolling, rasping, sanding,
or grinding. However, the success of any of these procedures depends on timing, particularly when epoxy IFRMs are involved.
Finish rolling freshly applied sprayed intumescent coatings reduce the initial texture of epoxies and can make them appear smoother from a distance. Rolling must be done at the right time after the initial application—early, but not too early—in the cure. Rolling too early can “push” the material, creating thickness variations and an uneven film build appearance. It can also result in the material sticking to the roller cover, creating a stippled finish. Rolling too late will not smooth the finish at all. Misting, not soaking, the roller cover with solvent may help in finish rolling, provided the solvent can be used in the work environment. It must be noted, using excessive solvent can extend the recoat or dry time of the material or lead to solvent entrapment should it be overcoated too soon.
Rasping can smooth out runs, sags, spits, or other textural defects. However, it must be performed during an intermediate stage of curing, when the material is firm enough to withstand a rasping treatment without deforming, but not so late that rasping is ineffective. Certain well-cured epoxy coatings rasp very well. To facilitate timely coating applications, rasping may need to be done on a follow-up shift, which requires costly additional labor.
Abrasive methods such as sanding or grinding can achieve the smoothest IFRM coating finishes. However, they are far more costly, since they require added labor, and over-application of the coating (around 20 percent), some of it can be removed to create a smoother protective coat while retaining the minimum specified thickness for the structure’s rated fire protection. Adding to the complexity, abrasive processes can be more difficult to manage. Acrylic coatings may heat up and soften, causing abrasives to gum up quickly, while epoxy formulations naturally resist abrasion and surface damage. Optimizing overall cost may require modifying application procedures and using rolling and rasping to reduce the need for abrasive methods.