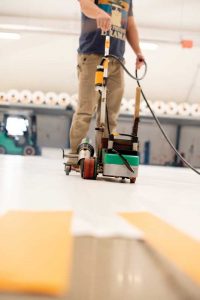
With the goal of ensuring better quality control, leading manufacturers have invested in their own on-site facilities and employ their own full-time Certified Welding Inspectors (CWI) to thoroughly inspect the varying I-beams for every project. Having inspectors on site has provided manufacturers with the flexibility to accommodate requested modifications that impact the final design required for the steel frame.
Critical corrosion prevention
Such an investment becomes even more important when one considers the common applications for fabric structures. While some markets, like event centers and sports and recreational facilities, often require the steel framing to be enclosed within the building’s fabric-cladded walls, it is commonplace in other industries for the I-beams to be left visible and exposed.
For applications such as commodity, fertilizer, or salt storage—or locations in humid, high-moisture environments, like wastewater treatment plants—corrosion concerns are a significant challenge for the steel frame.
The older style hollow-tube truss frames were notorious for hidden corrosion originating inside the tube. I-beams are made of solid steel to eliminate this, but their surfaces still must be treated to protect against corrosive elements. Hot-dip galvanizing was the go-to method for this protection for decades. In recent years, the industry has shifted toward coating I-beams with epoxy paint.
Galvanizing adds a thin layer of zinc around the steel. That layer is sacrificed over the course of several years, with corrosion gradually eating it away. In effect, galvanizing is a long-term stopgap, slowing down the corrosion process as much as it can. Epoxy paint is consistently preferred as a corrosion-fighting solution because it creates a true barrier between corrosive elements and the steel framing members, thereby providing a much higher level of protection.
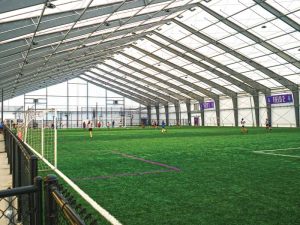
Epoxy coating is not new but is frequently considered cost-prohibitive for many fabric building customers when the only way to get it involves outsourcing. When manufacturers apply the epoxy coating in-house, the overall cost may be lower.
Equally important to a project’s ultimate longevity is the ability to control the quality of the paint job. Companies with this capability no longer must rely on a third party to do the work, but rather can bank on their professional expertise to hone in on the correct blast profiles and epoxy coating methods when preparing the I-beams for eventual shipping and installation.
Fabric self-fabrication
The story of how epoxy coating became more cost-effective is not unique in recent fabric building history. Certain polyvinyl chloride (PVC) fabric materials have followed a similar path to affordability, after previously having been reserved mostly for higher-end building projects due to higher costs.
Polyethylene (PE) fabric has traditionally been the most used material for cladding the roofs and sidewalls of tension fabric structures. Compared to the heavier yarn of PVC, standard PE material is relatively thin, with three layers comprising a fabric weave and top and bottom coatings. Its life expectancy is about 15 years.
A newer PVC on the market has seven material layers to provide increased tensile strength and longer service life. Further, as more in-house fabrication has emerged in the industry, fabric structure manufacturers can handle all the necessary panel cutting and prep of this fabric themselves, helping them to now offer PVC cladding to clients at lower prices than in the past.
Going hand in hand with lower costs is a better level of quality control. Manufacturers can cut PVC fabric panels to their specifications, rather than relying on a third party to handle the task. In-house personnel can review drawings and paperwork prior to fabrication, and in cases where they work under the same roof as the design engineers, can immediately discuss any issues without causing major project delays.