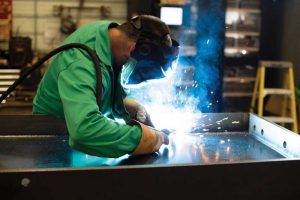
Having their own controlled environment for fabrication is another advantage toward ensuring quality. Common procedure is for fabric to be tested at the beginning of each day, at each new roll, and during any significant temperature changes observed throughout the day. Humidity and temperature are kept as consistent as possible in the plant as fabric panels are produced, and the final fabric panels can then be examined by the original building manufacturer before shipment.
Putting it together
Much like the design and manufacturing phases, the final piece of fabric building quality control comes down to a combination of “how” and “who” questions:
How is the fabric attached to the building frame?
Who is erecting the building?
Many fabric buildings use a panel attachment system, commonly featuring 6-m (20-ft) wide fabric panels, which are connected to each frame by sliding through an aluminum keder channel.
A traditional method for attaching the extrusion channel to the frame was using self-driving screws, which were problematic for a variety of reasons, including the fact water could settle in the hole created in the aluminum around a screw, eventually causing corrosion. An even bigger flaw emerged when some buildings had to have trusses twisted out of plane to install the panels and apply horizontal tension to the fabric.
Beyond the attachment method, the actual people handling the installation—and their experience or lack thereof—can come into play. Many suppliers hire local subcontractors to have their buildings erected on-site. Some manufacturers leave it to the customer to hire their own assembly team.
Some manufacturers have in-house fabrication crews, which is an ideal method of construction for this building type. Their internal knowledge and expertise make it easier to get every detail right, helping to ensure a complete chain of quality control from start to finish.