By Chuck Knickerbocker
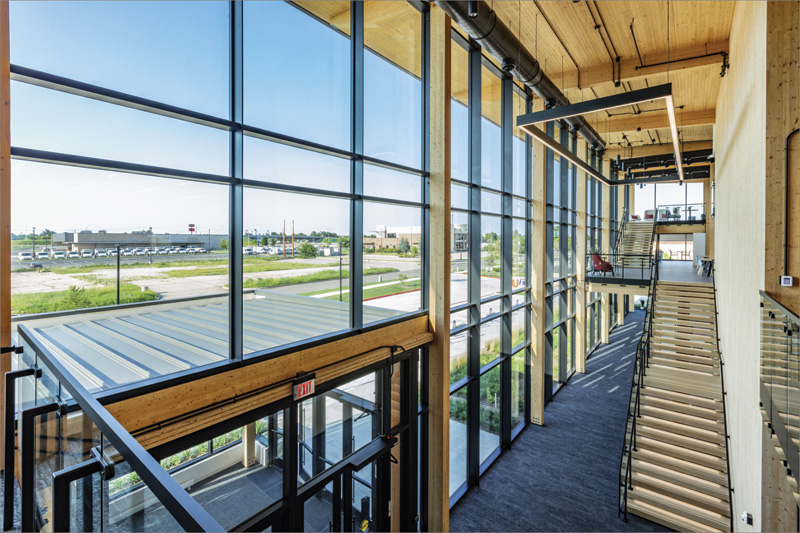
Glazing systems are significant in connecting interior spaces to the outdoors, making them a popular option for today’s sleek and modern building facades. Their ability to transfer daylight also makes them beneficial for interior applications. While naturally heralded for these attributes, glazing systems are increasingly required to do more as sustainable construction and energy efficiency take center stage.
As a result, building and design professionals are turning to high-performance building envelopes to reduce operational carbon. Glass and framing manufacturers have developed products that improve U-values, reduce solar heat gain, and enhance thermal performance to meet this demand.
With an ever-growing array of options available, building and design professionals might be challenged with selecting materials and systems that balance visual appeal with performance. To ease their process, this two-part series will delve into the performance of two beneficial glazing systems—steel curtain wall and channel glass, starting with the former.
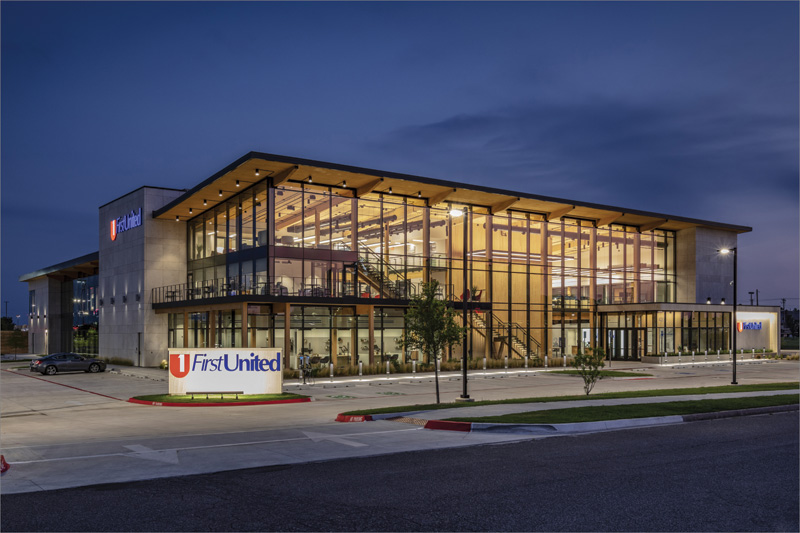
Steel the show by solving design challenges
Building and design professionals frequently use curtain walls to create monumental building entrances, providing beautiful views of the outdoors and natural lighting for spaces inside. Given the prominent role glass plays in achieving these goals, it is easy to see why much of the conversation centers on the glass itself. However, despite glass having a significantly larger area in a curtain wall, the framing is key in helping establish numerous design and performance outcomes. After all, the material and size of the framing significantly impact a curtain wall’s structural strength.
Consider aluminum—the historical framing material for curtain walls. The material is lightweight, versatile, and more corrosion-resistant than traditional steel framing, which is beneficial, considering parts of the U.S. are subject to freezing winters and heavy snowfall.
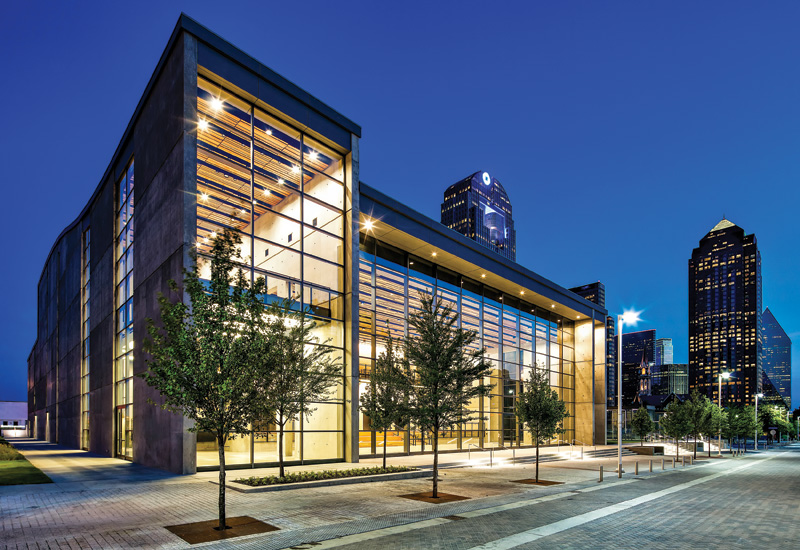
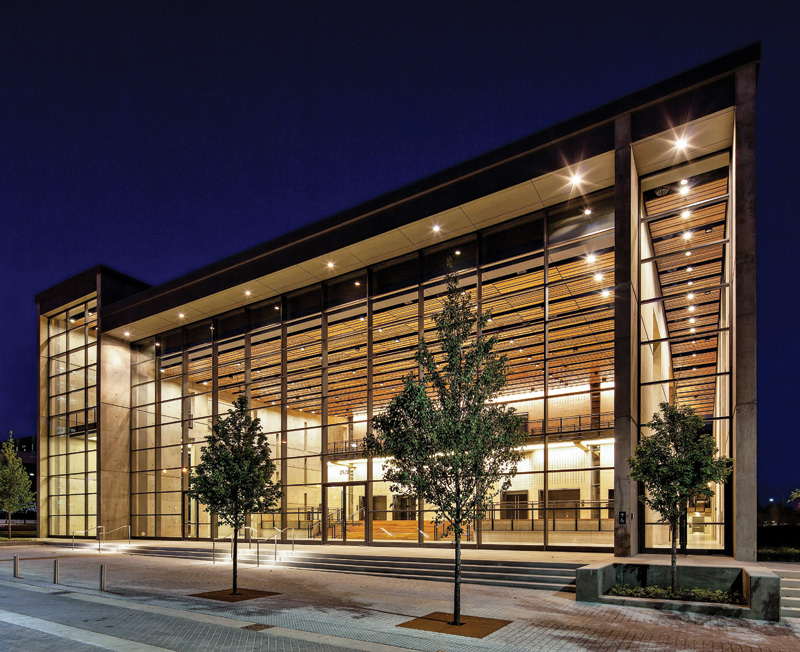
However, with Young’s modulus € of approximately 69 million kPa (10 million psi), aluminum may not be able to support the required loads associated with high-performance glazing simply due to their size, thickness, and/or weight. Likewise, increasing the free span size may lead to thicker and bulkier frame profiles than is desirable to ensure structural integrity. Unfortunately, larger frame profiles limit the total area of glazing possible.
As often happens in building construction, materials used in the past have metamorphosed into other variations of themselves, regaining popularity, as they did with wood and stone. This is now happening with steel, making it a viable alternative to aluminum for curtain wall framing systems.
Advanced technology offers weather sealing and moisture protection
Steel is an inherently stronger material than aluminum, with Young’s modulus € of approximately 207 million kPa (29 million psi). As a stronger material, it can support larger free spans at various locations throughout (not just at the podium level) of a building’s design.
Despite its strength advantage, the design-build sector preferred corrosion-resistant materials such as aluminum over steel since it could not withstand corrosion catalysts such as moisture and air.
However, today’s steel framing can be combined with innovative technology to eliminate any concern regarding corrosion. The material can be powder- or wet-coated to match the desired color scheme, using any coating suitable for architecturally exposed structural steel (AESS). The author recommends designers and specifiers approach coating manufacturers or suppliers about using specific coatings on steel if there are any questions. Building professionals can also use exterior caps or interior back mullions from stainless steel to match other building elements and suit local climate requirements. Manufacturers also provide high anti-corrosion protections, such as double-sided pre-galvanization, coated with a durable primer and finished with color to enhance weather protection.
While these protective mechanisms are beneficial, some manufacturers now offer gaskets that isolate the water and prevent it from coming into contact with the steel components. In such systems, a continuous gasket, typically made from extruded silicone, fills the gap between curtain wall components and keeps water off the tops of insulated glass units (IGUs). The water is directed to the verticals, which it is then weeped out of the glazing systems. The glazing pocket is also free of metal, supporting condensation resistance.
To further ensure protection, installers seal the lapped gasket joints at horizontal-to-vertical connections to any prevent water intrusion to the steel back members and interior occupied spaces. Another benefit of using steel systems is that do not require zone damming at each glazed lite to manage water flow, unlike aluminum pressure plate systems. However, the full gasketing fabrication method without zone damming still provides a water penetration resistance of 718 Pa (15 psf) or more, meeting ASTM E331, Standard Test Method for Water Penetration of Exterior Windows, Skylights, Doors, and Curtain Walls by Uniform Static Air Pressure Difference.
Modern techniques and installation systems have improved steel curtain wall assemblies, ensuring they effectively protect against dynamic and static water penetration, which helps reduce the risk of corrosion. These overlaps and specific joint treatments also provide a layered barrier to help maintain air tightness within the envelope.
Manufacturing advantages help use steel’s strength
Beyond corrosion concerns, traditional steel framing members were not as adaptable to different designs, preventing their widespread use as a primary material. Modern steel fabrication techniques today overcome these challenges, resulting in previously unimagined aesthetic possibilities for curtain walls. For instance, in the cold-roll forming process, flat steel sheets or continuous coils undergo a series of rolling operations to achieve project-specific profiles. This process enables the creation of complex shapes and larger sections from thin-gauge carbon or even stainless steel, with thickness ranging from 24-gauge 0.60 mm (0.02 in.) to 6 mm (0.23 in.).
Further, laser cutting and welding processes provide even greater flexibility. These processes involve taking long, flat carbon or stainless plates with lengths ranging from 11.8 to 15 m (38 to 49 ft) and thicknesses up to 38 mm (1.5 in.), and cutting them into bars or strips of the necessary width for shaping. Once cut, these bars are assembled into the desired shapes (rectangles, channels, T’s, angles, square tubes, and I-beams), and the joints are welded using lasers. This method allows steel profiles to meet custom width and depth requirements and, in turn, enables curtain wall system depths to be tailored per specific project specifications. Unlike traditional steel forming methods, the laser cutting/welding process allows these profiles to have sharp corners 0.5 mm (0.02 in.) rather than rounded ones, allowing teams to create corner joints with no visible weld beads or fasteners.
These steel formation processes also allow for the development of larger sections of thin-gauge carbon or stainless material with longer member lengths. Steel is much more versatile when shaped or formed in this advanced manner. Combining design flexibility with strength makes enduring and expansive glazing facades possible.
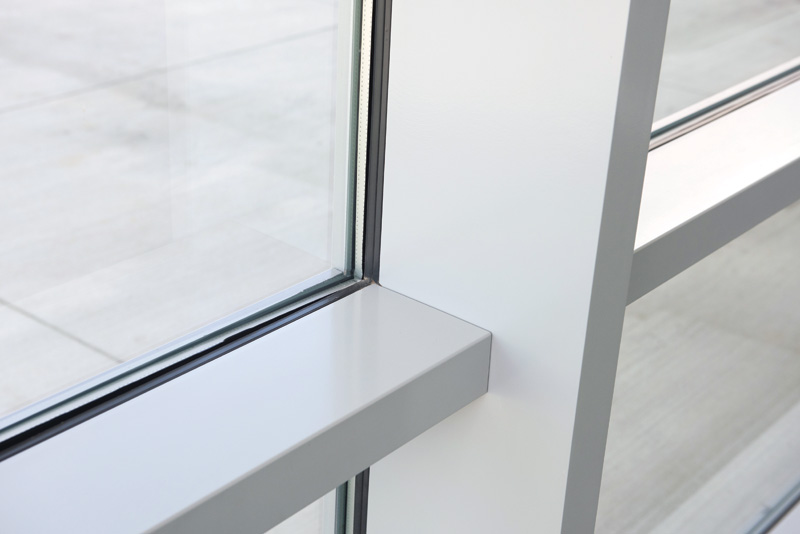
Narrow yet stronger framing system
In addition to production techniques, steel’s material properties offer specifiers significant advantages over conventional materials in large curtain wall designs. Using Young’s modulus € numbers earlier, steel is approximately three times stiffer than aluminum. Steel framing systems can better resist deformation and deflection under wind and other loads. Consequently, the stiffness of steel allows framing profiles to be much narrower in width and depth than aluminum’s for the same load specifications.
For example, if building and design professionals aim to meet design criteria for a typical two-story curtain wall, steel frames can accommodate a
45 x 146 mm (1.75 x 5.75 in.) profile. In contrast, aluminum would require a 64 x 200 mm (2.5 x 8 in.) profile. The profile size of an aluminum frame in such a case would be 25 to 50 percent larger than a steel framing system. The leaner steel profile does not compromise material strength and allows design teams to build more expansive curtain walls with larger glazing areas.
Greater glazing spans with fewer supports
Due to their strength, steel profiles can also support much larger glass panes than what is possible with aluminum. Moreover, the cold roll-formed and laser-welded steel processes help capitalize on steel’s strength and bolster its ability to handle a greater wind load. This enables building and design teams to achieve larger free spans and daylight openings between framing members without additional supporting members. For example, consider a 6 m (20 ft) long steel or extruded aluminum mullion with the same cross-sectional properties, using 1.4 Pa (30 psf) in a 1.5 m (5 ft) module as the design load (discounting allowable deflection limits momentarily). In this scenario, an aluminum mullion deflects 111.6 mm (4.4 in.), whereas a steel mullion deflects about 38.51 mm (1.5 in.).
These properties allow building and design professionals to use smaller system shapes to realize larger free spans and glass lites, facilitating uninterrupted outside views and greater illumination for interior spaces.
Thinner frame profiles have a smaller surface area for the sun to move across during the day, resulting in smaller shadow projections. Understanding steel’s performance capabilities, designers for the First United Bank’s regional headquarters in Moore, Okla., specified floor-to-ceiling glazing systems. The curtain walls helped them create uninhibited sightlines and fill the corporate office with daylight.
Prioritizing designs with energy efficiency
Steel’s ability to increase glazing spans and areas is one of the simplest ways for building and design professionals to maximize daylight area in building design. However, this can make a building more vulnerable to heat transfer, posing a challenge to attaining energy efficiency. While pairing framing systems with glazing solutions such as low-emissivity (low-e) coatings improve center-of-glass (COG) thermal values, they may still be susceptible to summer heat gain and winter heat loss.
Many building and design professionals have preferred thermally broken aluminum frames in predominantly subarctic climates. Incorporating thermal breaks (i.e. separations between the inner and outer frames) can help reduce the heat flow associated with the material’s high thermal conductivity (approximately 118 Btus per hour). However, thermally broken aluminum frames are not the only high-performance alternative available to North American professionals.
Thermally efficient glazing systems
Steel’s thermal conductivity is approximately 74 percent less than aluminum (i.e. approximately 32,7000 joule [31 BTUs/hr]). This is equivalent to that of thermally broken aluminum frames. Moreover, some advanced steel frames do not require a traditional thermal break due to profile designs. Steel frames without a thermal break require less metal to support the glazing than traditional aluminum frames. Therefore, they reduce and resist heat transfer. The computer simulations were conducted on steel curtain wall systems according to the National Fenestration Rating Council’s (NFRC’s) 100 Procedure for Determining Fenestration Product U-factors. These simulations used 25.4 mm (1 in.) insulating glass units (IGUs) with clear low-e coatings. The results showed the combined system achieved U-values of 1.65–2.21 watts per square meter and Kelvin
(W/m2.K) 0.29-0.39 Btu per hour per square foot per degree Fahrenheit (Btu/h·sf·F) (depending on the glass), significantly surpassing the thermal performance of many aluminum curtain walls.
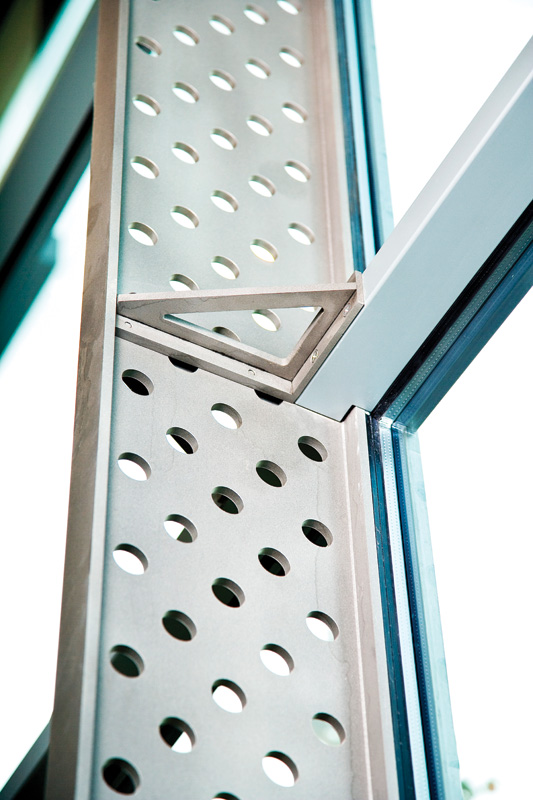
Steel supports high-performance glazing
To further mitigate heat transfer in curtain walls, building and design teams often turn to double- and triple-glazed systems and/or a variety of glass thicknesses to help balance natural light admission with energy costs. In similar scenarios, traditional framing systems might struggle to support these configurations due to their size and loads, requiring either a reduction in glass lite dimensions or free spans (which would increase the metal area).
Steel’s inherent strength allows it to support heavy triple- and quadruple-glazed units, with glazing infills up to 76 mm (3 in.) thick and weights up to 112.3 kg/m2 (23 lb/sf). This easily surpasses a triple-glazed unit’s thickness of 45 mm (1.7 in.) and weight of 48.8 kg/m (10 lb/sf), helping bolster a building’s thermal efficiency with ease. Underscoring this point, in NFRC 100 computer simulations of steel frame materials with IGUs comprised of clear glass and non-gassed airspace plus triple glazing, recorded U-values as low as 1.078 W/m2.K (0.19 Btu/h·sf·F). However, it is important to note these are approximate values only. Actual values will vary depending on specific glass and framing combinations per project requirements.
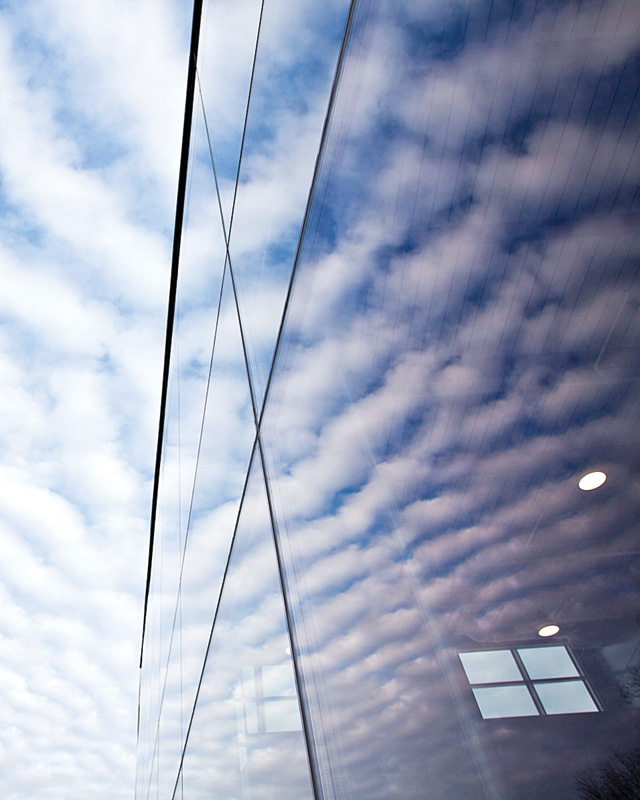
Mitigating airtight leakage
Modern steel curtain walls can mitigate air penetration infiltration, which can be especially beneficial in cold climates. There are two factors at play here. Firstly, steel’s coefficient of thermal expansion is about 12 x 10-6 meters per meter per degree Celsius (m/m C), which is much closer to that of glass (9) and concrete (10) than aluminum’s coefficient of 23.6. Similar expansion rates to neighboring materials reduce the strain on one material in case of temperature fluctuations. For example, when there is a high-temperature differential between the framing material and the supporting structure, the components will expand or contract differently, creating gaps in the envelope and causing air leakage. The compatibility of the physical properties between framing materials is also crucial to minimizing risks of sealant failure and other instances that affect thermal performance.
Secondly, when paired with the full gasketing, modern steel curtain walls promise almost no air penetration. When tested (per ASTM E283/E283M, Standard Test Method for Determining Rate of Air Leakage Through Exterior Windows, Skylights, Curtain Walls, and Doors Under Specified Pressure Differences Across the Specimen) with a pressure differential of 30.47 kg/m2 (6.24 lb/sf), a steel curtain wall’s air leakage has been consistently measured at 0.05 L/s•m2 (0.01 cfm/sf) or less of wall area. These factors enhance energy performance in steel-framed curtain walls, supporting sustainability goals.
The gasketing on the front of the steel frames plays a role in isolating steel from coming in contact with any air that may be present in the glazing channel, further mitigating infiltration. Together with perimeter detailing around the curtain walls or windows and select infill panels (glass, metal panels etc.), the steel-framed curtain wall can have an almost impenetrable air and water barrier. Naturally, tighter systems that prevent heat transfer are better at keeping conditioned air inside a building while not allowing untreated exterior air into building interiors. The process lowers loads on mechanical systems that do not need to work as hard to heat or cool interior spaces, improving energy efficiency. In doing so, steel-framed curtain walls support a project and team’s sustainability goals.
Sustainability considerations and LEED ratings
Steel curtain walls help building and design teams meet sustainability goals and various LEED requirements by optimizing energy performance and contributing to daylight and views.
With steel-framed curtain walls, green building professionals can earn points in the “Energy and Atmosphere” category by optimizing energy performance beyond standard requirements. Since high efficiency glazing systems may improve building performance and reduce excess load on the HVAC systems, they can mitigate excessive energy use. Steel’s lower thermal conductivity than aluminum also decreases energy demands by reducing heat transfer between inside and outside.
Steel frames can also help earn points in the “Indoor Environmental Quality (EQ)” category, which aims to connect occupants with the outdoors, reinforce circadian rhythms, and reduce electrical lighting use by introducing daylight. There are three methods to accomplish this goal. The initial method involves conducting yearly computer simulations to determine spatial daylight autonomy and average spatial daylight autonomy, with a minimum value of 40 percent. The second option requires computer simulations for illuminance during the equinox, while the third option involves directly measuring illuminance. The second and third options have a minimum threshold of 55 percent for regularly occupied spaces.
Since steel mullions support large free spans, they assist building and design teams in meeting daylight goals. Steel mullions come in various sizes and shapes, such as box, I-beams, and T-shapes. Compared to aluminum, steel T-shapes are thinner, effectively allowing better light penetration deep into building interiors by increasing the glazing size and reducing shadows to improve the quality of space. Larger glazing areas also offer better unobstructed and quality views, which can earn more LEED points in a category that seeks at least 75 percent of all regularly occupied floor areas to have a clear view of the outdoors through vision glazing. These factors make steel a compelling choice for environmentally conscious projects to maximize energy efficiency and advance sustainability goals.
In addition to evaluating the operational carbon of the building envelope to make strides toward a more sustainable construction practice, professionals are also examining the embedded energy and recyclable content within metal frames. Among available options, primary steel manufacturing consumes 2,800 kg (6,173 lb) of CO2 equivalent per tonne (kgCO2e/tonne), while aluminum has an embodied carbon rate of around 8,300 kg (18,298 lb) CO2e/tonne. Both these materials are 100 percent recyclable. However, recycled content in steel frames typically ranges between 15 to 25 percent, whereas using about 30 percent of recycled aluminum in framing profiles is possible. One of the reasons for this low recyclable content is that the global supply of scrap steel and aluminum (low carbon feedstock) is limited, albeit to a different extent.
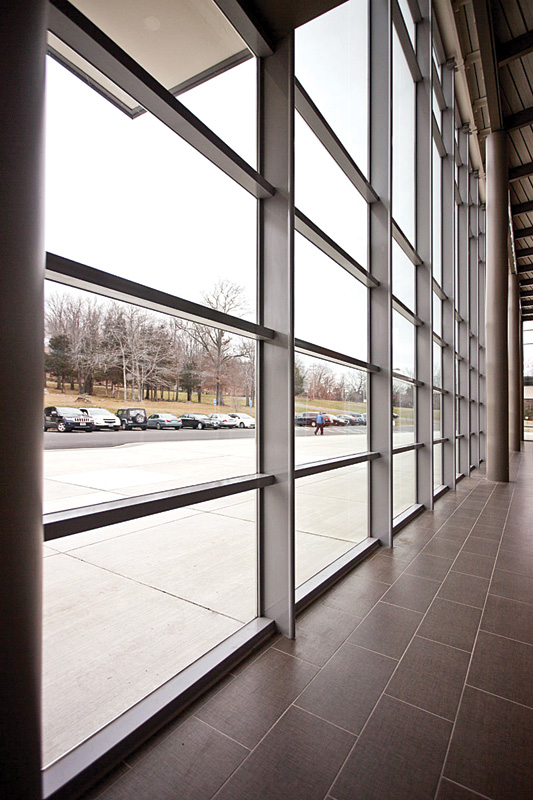
Looking beyond design and performance
When specifying curtain walls, professionals often consider the design potential and performance, the installation complexity, value for money, and long-term maintenance. Steel curtain walls are typically designed as stick wall systems, where fabricated and finished parts are shipped to the site for direct installation. Once the frame is in place, glaziers install the glazing. That said, it is also possible to unitize steel frames to a minimal extent, although it is less common when compared to aluminum extrusions. This is because the heavier weight of steel profiles requires stronger connections if assembled before installation. Plus, shipping unitized steel frames is not recommended over great distances due to the vibration the framing is subject to in transit. Adding to the complexity, pre-glazing steel-framed unitized wall assemblies before field installation can negate the functionality of the single-glazing gasket on the face of the framing member. As a result, the installation process would require a field-applied wet seal between units, fundamentally negating the desired “unitized” approach.
Whether using a partly unitized or stick system, steel-framed curtain wall installation can be beneficial when evaluating total costs. Although steel framing generally runs 20 to 25 percent higher than aluminum frames with the same spacing, this difference can be easily offset by steel’s ability to support larger lites. When looking at the larger picture, steel frames enable less framing members to be fabricated and erected, and can mean fewer field connections to the structure that have to be installed. A study found that increasing vertical mullion spacing from 1.2 m (4 ft) on center (OC) to 1.5 m (5 ft) and 1.8 m (6 ft) OC, reduced framing costs by 15 to 20 percent at each interval. While these values do not include erection costs, there are clear advantages in that regard as well. For example, a 9.144 m (30 ft) column spacing typically requires six 1.5 m (5 ft) modules or five 1.8 m (6 ft) modules. This means at least one less vertical component to purchase, fabricate, ship, and install, along with one fewer module of horizontals to furnish and install, thus reducing the number of glass lites to install. These reductions facilitate labor savings and offset field installation costs.
Additionally, efficient field installation directly impacts long-term maintenance. Precise installation of the continuous gasket mentioned above is crucial to preventing air and water infiltration through a steel curtain wall system. Reduced exposure to elements can reduce maintenance requirements and prolong the service life of the glazing system. For projects exposed to high-speed winds, where air tightness is a concern, installers can use pressure plates as a two-line resistance strategy for air and water penetration resistance. In these systems, the pressure plates hold the lites in place and help maintain adequate pressure on the glass, gaskets and framing. This creates efficient seals that resist air and water penetration, enhancing a curtain wall’s performance and reducing the need for intensive maintenance over the long term.
The balancing act
As building and design teams increasingly seek high-performance system solutions, specifying steel-framed curtain walls can help them address performance priorities without sacrificing visual appeal. After all, the exterior defines a building’s appearance.
To achieve the best of both worlds, it is crucial to consider how steel curtain walls fit within the overall building enclosure. This involves evaluating how a specific system interacts with perimeter details and surrounding materials, examining anchorage details, and verifying deflection to ensure structural integrity. Ironing out these details early in the design and specification process, through collaboration with steel framing manufacturers, can result in precise fabrication and seamless installation.
Moreover, consulting and adhering to the manufacturer or supplier’s installation guidelines is crucial for optimal performance. Assuming standard practices may lead to improper installation, particularly regarding air and water integrity, and could void the manufacturer’s warranty. Fortunately, many manufacturers offer design and installation support, which can help ensure enhanced energy efficiency and the enduring beauty of curtain walls for years to come.
Test your knowledge and take our quiz!
Author
Chuck Knickerbocker is the curtain wall manager for Technical Glass Products (TGP), a supplier of fire-rated glass and framing systems and specialty architectural glazing products. With more than 40 years of curtain wall experience, Knickerbocker has successfully worked with numerous architects, building owners, and subcontractors from schematic design development through installation.
Key Takeaways
As sustainability and energy efficiency become priorities, a growing demand for high-performance building envelopes is growing. This series examines the use of steel curtain walls in architecture, which are favored for creating striking entrances and optimizing natural lighting. Steel’s superior strength allows for larger spans and smaller frame profiles, and recent advancements have improved its weather sealing and moisture protection.