
Photo courtesy Bruce Damonte
Steel curtain walls with large glazed lites
Due to steel’s strength, it can support larger glazed lites than aluminum frames of the same shape. For design professionals working to increase the free span or glass module size, this means it is possible to specify double- or triple-glazed insulated glass units (IGUs) up to 76 mm (3 in.) thick without revising the system to support the intended glazing. This advantage makes advanced steel curtain walls a powerful alternative to fully utilize the massive glass units being introduced by today’s glass manufacturers. It is also an effective way to help increase the natural admission of light, and balance it with the energy costs associated with artificial light.
Additionally, because steel has a thermal conductivity of approximately 32,700 joule (31 Btu) per hour, compared to aluminum at approximately 124,500 joule (118 Btu) per hour, it can help reduce potential for heat gain and loss through the glass and frames. This is a critical performance benefit as a system’s overall thermal efficiency is often substantially less effective where the captured or retained glass edge meets the supporting frame. Where frames with low thermal conductivity are critical to project goals, specifiers can select from advanced steel frames without a traditional thermal break. Such frames use less metal to support the glazing than traditional aluminum frames—further reducing the pathway for heat transfer.
When incorporating large glass lites, specifiers can also work with the manufacturer or supplier to determine the minimum required frame width. Steel can meet curtain wall load and deflection criteria requirements with less material than aluminum, enabling design teams to preserve thin frame dimensions and narrow sightlines, even as the glass size or unit thickness is increased.
Multi-story steel curtain walls
Steel’s strength and versatility also enables multi-story curtain walls (Figure 3). As is the case with any curtain wall, the maximum allowable height depends on factors such as applied loads, and thermal expansion and contraction. However, the primary factor influencing the allowed height is where the curtain wall’s dead load will bear on the structure. This determines the length of individual pieces of vertical framing, the number of splices (if required), and how the glass accommodates the movement within the curtain wall system at splice locations.
For example, rather than have a six-story curtain wall’s full weight (about 1.1 kPa [25 psf] due to thick glass) forced on the lowest level of the structure, the project engineer required each floor carry the imposed curtain wall dead load. To accommodate the load, the steel mullion was sized at 60 x 180 x 2.5 mm (2.3 x 7.1 x 0.1 in.) thick, and required a 12.7-mm (1/2-in.) dynamic splice joint at every floor. Additionally, to ensure the live load deflection did not exceed 0.95 mm (0.375 in.) at these conditions, it was necessary to change the sizing of the structural steel frame to limit it. Exact conditions often vary between projects; this allows larger splice joints and/or greater structure flexibility. It is important to communicate these requirements in the construction documents for review by the steel system detailers.
Another important consideration during the specification process is the impact of the structure’s long-term potential movement at the points where the curtain wall anchors to the structure. column or structure foreshortening (shrinkage) will generally not be included in the curtain wall specifications. However, this information is critical for the curtain wall designer to know in order to properly design and specify anchorages, splice connections, and sealant perimeter joints.
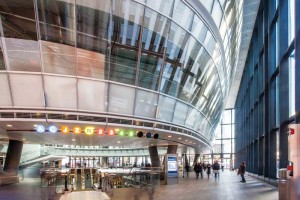
Photo courtesy TGP
Segmented steel curtain wall systems
In buildings where it is desirable to install a curtain wall with a curved aesthetic, design professionals can use steel mullions to create a segmented steel curtain wall system (Figure 4). For off-the-shelf standard steel systems, the degree of turn is typically limited to a maximum of 10 to 12 degrees at any single mullion. Custom steel systems can have a greater degree of turn to help design teams achieve a tighter radius. However, manufacturing order minimums can prove cost-prohibitive in small- and mid-sized curtain wall projects.
When working with segmented curtain walls with a tighter radius, the mullions are typically spaced more closely for standard steel systems. For a curtain wall with a 4.5-m (15-ft) radius that goes around a 90-degree corner, the turn is typically limited to 10 degrees for standard steel systems. In this instance, the curtain wall would require approximately nine mullions spaced 0.76 m (30 in.) apart on center (oc). If the radius was opened up to 9.4 m (30 ft), the nine mullions would be spaced 1.5 m (62 in.) apart.
The degree of turn at individual mullions, as well as glass thickness (specifically, the ability to maintain the minimum glass bite dimensions at glass edges), will also determine whether it is possible to use standard pressure plates and covers. For example, if the glass thickness or degree of turn exceeds the capacity of the standard pressure plates and covers, manufacturers can furnish custom shapes to meet project demands.
While steel and glass can be easily bent or curved (albeit at a high cost), the following issues commonly preclude their use and result in segmented steel curtain wall systems. Firstly, the way cold-roll formed steel is processed does not curve in a similar fashion to hot-rolled or standard steel shapes. Secondly, other curtain wall components—such as the glazing veneer—will not hold their shape when rolled, compromising the system’s functionality. Lastly, each component has its own set of bending or forming tolerances and many are not compatible with each other. For example, one component may go to the ‘positive’ side of its allowable tolerance when curved, while an adjoining component may be manufactured at the ‘negative’ side of its tolerance.
To date, coordination of tolerances to eliminate differences between the various material suppliers has not been possible. However, when a curved curtain wall or window is assembled, the system generally relies on a sealant to account for any such differences and to ensure air and watertightness when in service.