
Photos courtesy TGP
Structural silicone glazed steel curtain wall systems
Where a frame-free, glass-clad aesthetic when viewed from the exterior is desired, a popular option is to install structural silicone glazed (SSG) steel curtain wall systems. In such systems, structural silicone attaches silicone glazing-compatible glass lites to modular steel-back mullions. This setup utilizes steel’s strength while eliminating the need for exterior pressure plates and caps, which typically retain the glass to the frame. For design professionals, this opens the door to curtain walls with soaring free spans (up to 12 m [40 ft] nominal free spans in single members) and an uninterrupted exterior glass surface.
As is the case with most curtain wall systems, the size of the back member depends on glass size, design loads, and connection or anchor points. One additional factor specific to SSG systems is the amount of sealant required to hold the glass to the frame. The size of a glass lite and its anticipated design wind load determine the amount of silicone that must be in contact with the glass and framing. This dimension is called the bond line width. In addition to the amount of gasket or glazing tape and the exterior weather joint between lites of glass, the bond line width generally sets the width of the framing member.
Depending on the type of SSG system, the waterproofing methodology may also be different than conventional captured curtain walls. For example, if water is not allowed within the glazing pocket past the exterior face of the glass, it is possible to employ a barrier system where the sealant joint between the lites of glass is responsible for keeping water out (Figure 5).
Where it is necessary to have SSG curtain walls with ‘two lines of defense’ for air and water resistance, it is possible to use a cassette or toggle system. In such systems, a small aluminum extrusion is structurally silicone glazed to the glass. Toggles are then inserted into the channel and fastened to a fully gasketed steel curtain wall framing system to retain the glass. The gasketing provides additional air- and water-resistance within the system. From an aesthetic perspective, these weather joints look the same as a conventional barrier system.
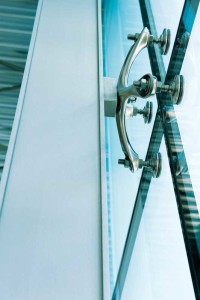
Point supported steel curtain wall systems
Design professionals desiring glass façades and walls with narrow sightlines can also use steel mullions as the structural component in point-supported glazing systems. In such systems, custom structural fittings (i.e. ‘spiders’) connect the glass to the steel supporting members (Figure 6). This design mechanism concentrates loads at the connector locations, rather than applying a uniform, consistent load to the frame members. As a result, it is important to work with the curtain wall supplier’s structural engineer to ensure the frame member size is sufficient.
Additionally, it is crucial to verify the glass in point supported systems is able to accommodate any loads transferred between it and the structural connector without fracturing. Many connectors, including popular spider brackets, require the manufacturer to drill holes in the glass. These holes concentrate the wind load and dead load (i.e. weight of the glass) transfer from the glass at the connector before transferring their loads to the curtain wall framing member. This makes it paramount for the glass to be constructed in such a way as to resist these concentrated point loads. This challenge becomes even more complex when point-supported curtain walls incorporate IGUs or laminated glass constructions. The glass fabricator must seal and align the holes between the IGU lites at the spider penetrations, driving up the tolerance constraints of fabrication. Given these challenges, manufacturers are developing alternative methods of connecting glass panels to the structural supports, including a spider bracket connected to the glass via structural silicone, thereby eliminating the need for holes through the IGU.
When the challenges with glass in point support curtain walls are properly addressed, systems with steel back members can serve as a cost-efficient curtain wall option. Due to steel’s strength, framing members are typically only required in one direction to reduce material costs. This is often the verticals because they handle gravity better. While horizontal framing members may be required to resist buckling loads in I- or T-beam vertical members, it is possible to reduce the size and frequency of horizontal framing members. Fewer framing members can help put the glass and the resulting, less-obstructed views to the exterior on center stage, while also furthering cost savings.
Fire-rated curtain wall systems
Modern steel frames are advantageous for non-rated curtain wall systems, and also for fire-rated systems. One pronounced benefit is their ability to help design teams match the aesthetic of fire-rated systems to neighboring non-rated curtain wall, window, and door systems.
For years, fire-rated ‘hollow-metal’ steel frames have been viewed as bulky wrap around affairs that, although functional, are at odds with today’s slender, monolithic glass façades and walls. Design professionals can now achieve a uniform look by using steel fire-rated frames formed from tubes and shaped in a rolled process similar to new generation steel frames. The frames have narrow profiles, well-defined corners, and crisp edges. They can also be custom painted or powder-coated to match or complement non-fire-rated frames, and can incorporate custom cover caps to provide a wide range of design schemes. Together, these benefits make it possible for design teams to install fire-rated frames that integrate well with surrounding curtain wall, window, and door applications.
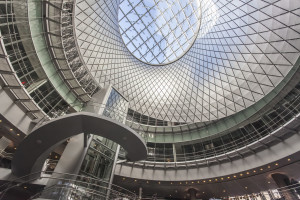
New York’s Fulton Center achieved this. The building’s retail and transit interior spaces are flooded with light from a 16.2-m (53-ft) diameter glass oculus, and thus a crucial part of the design aesthetic was ensuring the grand atrium’s interior curtain walls had clean sightlines—even in areas required to provide fire protection. To successfully achieve this design, the project team used non-rated and rated custom captured horizontal steel mullions that fit the atrium’s distinct shape and created a matching look across the upper (the fire-rated portion) and lower (non-rated) curtain wall assemblies (Figure 7).
While new generation steel frames make it possible to match the aesthetic of non-rated systems, it is important to note fire-rated glass requires stiffer frame deflection criteria (under wind load) than non-rated glass and can weigh between 100 to 350 percent more than non-rated glass. To limit deflection, design teams may need to increase the framing member size, or reinforce smaller profiles. While reinforcing the profiles is a viable option in instances where a larger profile may hinder the design intent, it can significantly increase the cost of the framing.
An alternative to captured fire-rated curtain walls is glazed assemblies that emulate the smooth appearance of silicone glazed (SG) non-rated systems. They are one of the most recent fire-rated glass systems on the market, and can help design professionals achieve a sleek, frame-free exterior aesthetic through a toggle retention system that becomes hidden once installed, eliminating the exterior pressure plate and cover cap of a conventionally captured system.
Conclusion
Today, architects continue to seek curtain wall assemblies that soar higher, hold larger glass lites, and minimize the visual impact of frames. Once an obstacle to these goals, steel frames are now a catalyst for innovation.
Chuck Knickerbocker is the curtain wall manager for Technical Glass Products (TGP), a supplier of fire-rated glass and framing systems, along with specialty architectural glazing products. With more than 35 years of curtain wall experience, he has successfully worked with numerous architects, building owners, and subcontractors from development of schematic design through installation. Knickerbocker chairs the Glass Association of North America (GANA) Building Envelope Contractors (BEC) Division Technical Committee. He can be contacted via e-mail at chuckk@tgpamerica.com.