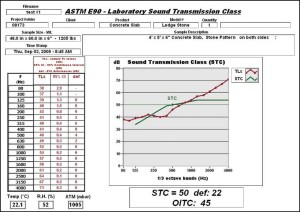
Data courtesy Element Materials Technology
Precast walls are built to withstand an assortment of weather conditions. Sun does not degrade them to the extent it does wood walls. Since hydration actually helps build concrete’s strength, water does not damage precast walls. Concrete’s inherently impermeable surface prevents chloride from road salt from migrating into the concrete. Properly air-entrained concrete is designed to withstand the freeze-thaw process and can last for decades without degrading. The air structure within concrete provides a place for frozen water to expand, preventing the confinement required to push apart and degrade concrete in the first place.
Low-maintenance aesthetics
Aesthetic value is another appealing aspect of precast sound walls. Concrete walls require minimal maintenance to preserve their ‘posture.’ While sun fades the stains and paint of wooden walls, there is no need to add a layer of paint or stain to most precast walls. Instead, concrete can be tinted with a permanent hue that does not wash away or fade as highway walls bake in the sun. Many U.S. Departments of Transportation (DOTs) are selecting buff-colored tints that resemble indigenous rock, limestone, or other surroundings. When entire highway walls are stained with earth-toned shades, they easily camouflage into their natural environment.
Neighboring communities also often appreciate the aesthetic value offered by precast sound walls. Historically, the walls were only finished on one side, so either highway passengers had to view the less attractive side, or else the neighbors had to. Now, finishes can be applied to both sides of the highway walls.
Maintenance for precast walls is simple. As concrete walls get coated in dust, dirt, and other elements, a sporadic high-pressure wash-down is all that is necessary to make the wall look as good as new. Re-caulking once every 15 years eliminates fissions that can develop over time. Conversely, other building materials require much higher maintenance. With precast concrete, less than one percent of its surface area is caulked, compared to 20 to 30 percent of brick surface area that is mortar.
Masonry is also susceptible to cracking because of the sheer number of components bound by mortar. When cracks appear, tuck-pointing is necessary. This involves reapplying mortar to all of the joints and is expensive because it takes time to remove old, failed mortar. Since masonry is porous, it requires a sealer (e.g. paint) applied at installation and at regular intervals to control moisture migration from the outside atmosphere.
Rapid construction
Another benefit precast sound walls bring to citizens and specifiers alike is their ability to be expeditiously erected, compared to the installation method of their wooden counterparts. When building wooden sound walls, the construction crew must first plant a long row of columns, and then retrace their footsteps to begin bolting on wood piece by piece. With precast, builders can erect the concrete slabs sequentially, eliminating inefficiencies and expediting the process. Concrete columns are set with a light crane or a rough terrain forklift, and then are grouted in place. Once two columns are set, the walls are slipped into the columns’ slots without requiring any additional connection work. This provides the potential to reduce 15 to 20 percent in a typical sound barrier construction schedule.
The shortened installation time is appealing for construction teams in climates subject to ground-freezing temperatures. For crews that can only install walls nine months of the year while the ground is thawed, rapid installation is a significant benefit. Minimizing road construction time is also important for traffic circulation.

Photos © Alan Krane. Photos courtesy Fabcon
The bottom line
The durability and weather-resistant nature of precast walls can create an affordable long-term solution for many city and state specifiers. Traditionally, wood has been considered the most cost-efficient option for highway walls. As the price of concrete and precast sound walls has lowered, and lifecycles have been evaluated, it has become clear precast highway walls are nearly equitable to wooden walls in short-term costs. Moreover, precast walls offer significant savings in the long term.
State DOTs paid an average of $172/m2 ($16/sf) for wooden highway walls in 2010. Precast highway walls cost between $172 and $175/m2 ($16 and $16.25/sf), and have a significantly longer lifecycle. Considering that wood panels last an average of a decade and precast panels typically last between 20 and 40 years, one can calculate a minimum savings of $169.50/m2 ($15.75/sf) after 10 years with precast walls.
In addition to their long lifecycle value, precast highway walls have a sustainable component that appeals to forward-thinking communities and specifiers as well––they can be disassembled and re-constructed, since the panels themselves are not connected to columns. Instead, they are attached to columns through a tongue-in-groove system. When a major road project is underway and crews need to take down the sound walls, all they must do is slide the panels out of the columns. Rather than discard the panels, they can reassemble them to construct another highway wall, saving time and money without sacrificing the durability or aesthetic nature that characterizes precast highway walls.
Tom Kuckhahn, PE, is the vice president of manufacturing and engineering for Fabcon. He has been at the company since 1994. Kuckhahn graduated from the University of Minnesota with a bachelor’s degree in civil engineering and has been a professional engineer since 1999. He can be reached via e-mail at tom.kuckhahn@fabcon-usa.com.