Preservation and adaptive reuse: Strict adherence to standards reaps rewards
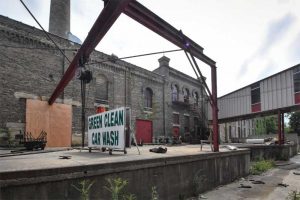
Historic preservation
Masonry
Mortar unifies the units of masonry, such as bricks and stone, and also repels the elements from the interior. Mortars used in antiquity were relatively simple—most consisted of sand and lime. Over time, mortars began to include cements, natural pozzolans, and water repellent chemicals. Using repair mortars with incompatible compositions and proportions on a historic building can change the response of the building façade to temperature and moisture, resulting in unwanted distress. For this reason, it is important to fully analyze and define the components in the original mortar prior to initiating a repair.
Repointing or tuckpointing is the process of removing failed mortar from the joints of a wall and replacing it with new mortar. Tuckpointing a historical building or structure with no regard to the architecture and craftsmanship can cause irreversible damage. The trades people who work on historical buildings must have knowledge of architecture to plan and execute a proper restoration that maintains the building’s integrity. Each building as well as mortar and type of mortar present its own set of rules. Mortars for repointing projects, especially those involving historic buildings are custom mixed to ensure the proper physical and visual qualities.
Roofs
According to NPS, not only is a weathertight roof important to the long-term preservation of the structure, but it is important to identify, retain, and preserve roofs, including their decorative features to maintain the overall historic character of the building.
The process of renovating the roof system on a historical building is one that requires acute attention, care, and cooperation with the appropriate government entities. When conducting a thorough physical investigation of the roof and its structure, understanding the construction history and the following areas is crucial:
• Deck type and condition, as some historical decks may no longer be structurally sound.
• Deck load capacity to ensure a new roof and any insulation does not exceed load capacity.
• Deck uplift resistance, since older decks may rely on gravity for uplift resistance and are not always adequately attached for current uplift resistance.
• Rooftop equipment supports that may be deteriorated and not adequately attached for uplift or seismic requirements.
• Wall substrate condition and roof drainage characteristics.
Floors
Wood is one of the most essential materials used in American buildings of every period and style. Most wood flooring is made of tongue-in-groove construction. The upper and lower grooves or ‘tabs’ are about 6.3 mm (0.25 in.) thick. Some original wood flooring made of lower-grade pine had a hardwood veneer that was usually milled at just 13 mm (0.5 in.) thick. The strips of hardwood are usually narrow (typically 31.7 to 38 mm [1.25 to 1.5 in.] wide) and face-nailed to the floor.
If the historic building’s tongue-in-groove or veneer wood floors have already been sanded once or twice, re-sanding them may not be an option. A typical groove is 6.3 mm and a typical sanding removes 3.2 mm (0.125 in.), so a tongue-and-groove floor can only take two sandings before the groove will be sanded off and expose the tongue and nails. If the floors cannot take another sanding, consider a light screening instead. Screening is done with a drum sander that has a light buffer pad rather than abrasive sandpaper. This method removes layers of old wax and lightly buffs any scratches in the wood, but it does not diminish the depth of flooring.
If the wood flooring has damaged boards, pieces of wood flooring from secondary areas of the building may be salvaged, such as from the floor of a closet. Remove the damaged boards and carefully fit the replacements in. Secure the new board with nails and finish it to match its appearance to the already existing floorboards.